Importance of quality management in manufacturing
Manufacturing processes require meticulous quality assurance to deliver the expected results. Operations cover activities performed throughout the production process to prevent defects, reduce waste, and ensure that the final product meets customer requirements. Quality control is a vital component of any manufacturing process that aims to deliver consistent output and maintain customer trust and loyalty, reduce costs, and preserve competitiveness in the global market.
Best practices to prevent errors in manufacturing
Delivering error-free, high-quality products is a serious matter and requires attention to detail, along with a number of good practices.
Knowledge management
One of the core practices to prevent errors in manufacturing is to invest in the training and education of employees. Workers provided with the necessary skills and knowledge can operate machinery correctly, handle materials safely, and identify potential issues early on. Additionally, training can increase employee engagement, motivation, and productivity, leading to better-quality products and fewer errors. Companies that prioritize employee training and education often have higher employee retention rates and better safety records, which translate into cost savings and increased customer satisfaction.
Automation
Automation is an essential tool for manufacturers looking to improve quality control. By leveraging advanced technologies (like augmented and virtual reality) and automated systems, manufacturers can achieve greater efficiency, accuracy, and consistency in their production processes, ultimately driving better business outcomes and delivering superior products to their customers.
Automated systems can perform repetitive tasks with greater accuracy and consistency than humans, which reduces the likelihood of errors. Operating tirelessly 24/7 means that manufacturing operations can continue also with minimal human input to ensure continuity. Automated systems can identify defects or variations in the production process, enabling manufacturers to resolve issues before they become major problems. This can help reduce waste, rework, and the risk of product recalls, ultimately improving customer satisfaction and brand reputation.
Regular maintenance of equipment
Equipment that is poorly maintained or outdated can be a major source of errors and downtime. By scheduling regular maintenance and inspections, manufacturers can identify and correct potential issues before they result in costly downtime or safety hazards. Additionally, regular maintenance can help to prolong the lifespan of equipment, which can ultimately result in cost savings over time. Therefore, regular maintenance of equipment (including predictive maintenance) is one of the essential practices in manufacturing operations.
Testing and inspection of raw materials
The quality of raw materials has a significant impact on the quality of the final product, and any defects or errors in the raw materials can result in substandard products. By testing and inspecting raw materials before their use in production, manufacturers can identify any potential issues early on and avoid costly rework or customer complaints. Additionally, testing and inspection can help to ensure that raw materials meet specific quality standards and that suppliers are meeting contractual obligations.
Implementation of Standard Operating Procedures
The implementation of Standard Operating Procedures (SOPs) is one of the critical actions for preventing errors in manufacturing. SOPs are detailed instructions that outline the steps involved in a particular task or process. By implementing SOPs, manufacturers can ensure that employees are following standardized procedures proven to be effective and efficient. SOPs can help to prevent errors by providing clear guidance on how to perform tasks correctly, reducing the likelihood of mistakes and variability in the production process. Additionally, SOPs can help to improve safety by ensuring that employees are following proper procedures for handling equipment and materials.
SOPs can be used to monitor and measure the performance of the production process, helping to identify areas for improvement and facilitate continuous improvement. By regularly reviewing and updating SOPs, manufacturers can ensure they reflect the most effective and efficient practices for the best results.
Implementation of Statistical Process Control (SPC)
SPC is a proven solution for ensuring consistent output in manufacturing. SPC involves monitoring and controlling the production process using statistical techniques to detect and correct variations in the process. By collecting and analyzing data on the production process, manufacturers can identify trends and patterns to improve efficiency, reduce errors, and ensure consistent output. SPC can also help manufacturers quickly identify and correct issues, reducing the likelihood of defects or errors in the final product.
Continuous improvement and process optimization
Continuous improvement and process optimization involve an ongoing cycle of monitoring, analyzing, and making improvements to production processes in order to enhance product quality and increase efficiency. The process entails data collection and analysis to identify areas for improvement, followed by the development and implementation of targeted solutions to address these issues. These solutions may involve changes to equipment, technology, or personnel, or the implementation of new process controls, quality standards, or training programs. Once changes are implemented, the process begins again with ongoing monitoring and analysis to ensure that improvements are sustained over time.
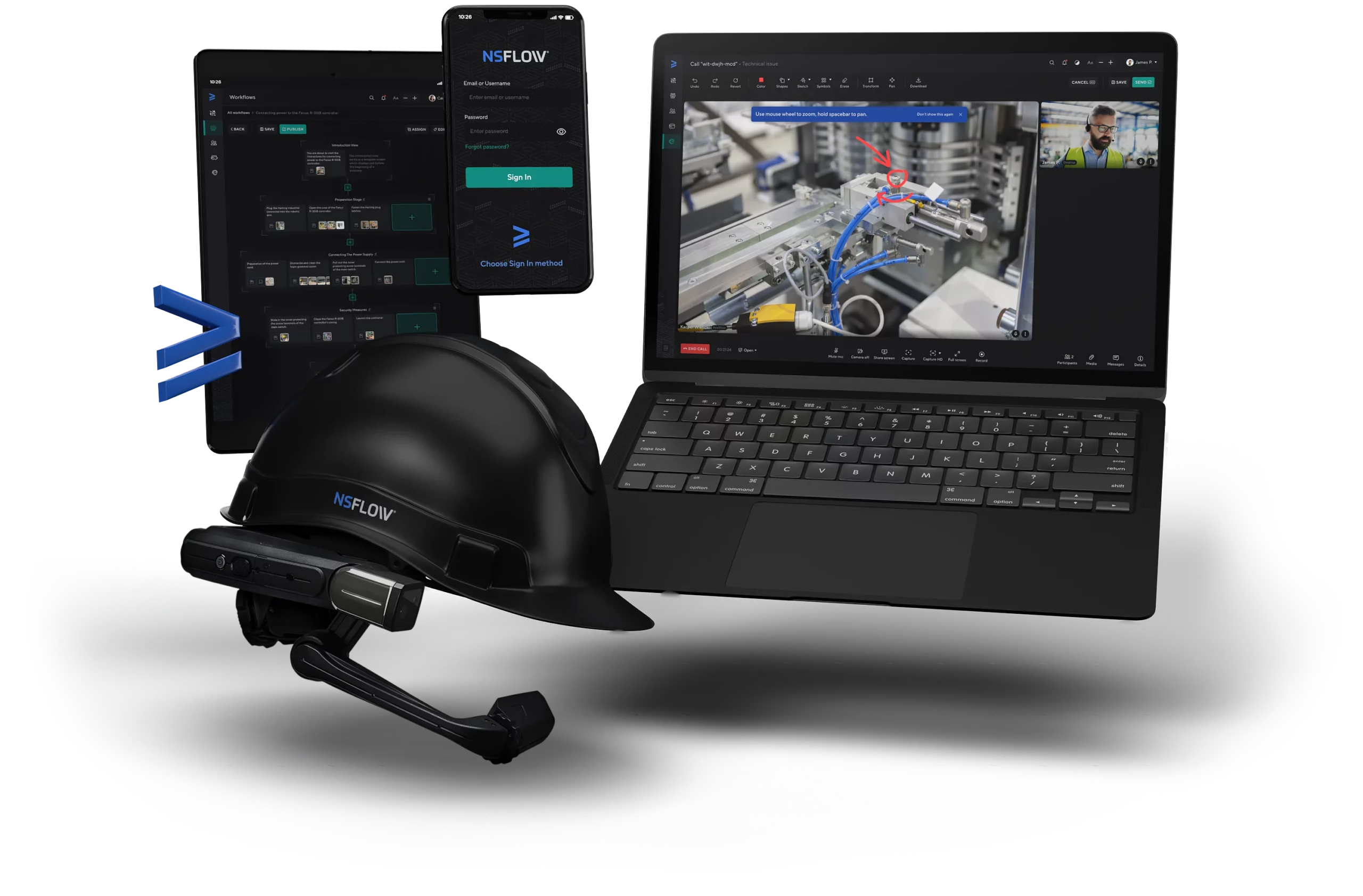
presentation to try
Nsflow in action
Ensuring consistent and error-free manufacturing – tools and techniques
A short recap of popular solutions employed in quality control in industrial enterprises
Control Charts
Statistical tools used to monitor and analyze process variations in manufacturing. By plotting process data over time, control charts can help manufacturers identify trends, patterns, and abnormalities in their production processes, enabling them to make timely adjustments and improvements.
Pareto Analysis
A technique used to identify and prioritize the most significant factors contributing to quality issues in manufacturing. Through analyzing data and determining the frequency and impact of specific issues, manufacturers can focus on the most critical areas for improvement, ultimately reducing waste, improving efficiency, and enhancing product quality.
Fishbone Diagrams
Also known as Ishikawa diagrams, fishbone diagrams are visual tools used to identify and analyze the root causes of quality issues in manufacturing. Using the tool for organizing potential causes into categories and subcategories, manufacturers can systematically investigate and address the underlying factors contributing to quality problems, ultimately improving process performance and product quality.
Failure Modes and Effects Analysis (FMEA)
FMEA is a proactive approach to quality control that involves identifying potential failures and their effects on product quality, safety, and performance. FMEA streamlines the assessment of the likelihood, severity, and detectability of potential failures allowing manufacturers to develop strategies to prevent or mitigate the impact of these failures, ultimately improving product reliability and customer satisfaction.
Kaizen
Kaizen is a continuous improvement methodology that involves making small, incremental changes to manufacturing processes over time. By involving all employees in the improvement process, Kaizen encourages a culture of ongoing improvement, ultimately leading to greater efficiency, productivity, and product quality.
The importance of quality control in manufacturing
Without quality control, manufacturing processes may result in substandard products that can harm consumers, in consequence damaging the reputation of the company, and leading to legal and financial implications. These risks make for sufficient reasoning for executing top-notch quality control to ensure customer satisfaction, reduce costs, and maintain competitiveness in the global marketplace.
As the manufacturing industry continues to evolve, quality control will remain a critical aspect of production, and industrial enterprises must continue to adapt and innovate to meet the changing needs in the dynamic market.
Easier said than done? We’re here to help you with supporting industrial processes with digital solutions. Augmented reality improves the execution of various processes and quality control in manufacturing is no exception here. Reach out to learn more about the potential of AR in industrial quality management.