The paperless approach to manufacturing
Paperless manufacturing is defined as incorporating software solutions to assess and execute industrial processes, gathering and utilizing data that has been generated along the way. Going paperless is becoming one of the dominant trends in industrial companies, enabling cost reductions, supporting lean initiatives, and promoting continuous improvement.
Manufacturing processes designed for turning paperless include but are not limited to:
Office and HR matters
Training
Inspections, maintenance
Reporting
Invoicing
Protocols
Audit trails
Documentation and technical specifications
Task allocation
On-the-job instructions
Worksheets
Operation and maintenance documentation
Tracking the flow of materials, semi-finished products, and products (Kanban)
Control of the aging process
Control of entries/exits, visiting cards
Control of working time
Design and prototyping
Why paperless?
Paperwork is not the root of all evil (though some office people would kindly disagree), but it does cause some hassle. For example, carrying out inspections in the traditional way can entail the following pieces:
– an inspection schedule hung on a board in the service department,
– an inspection order printed out by the service technician, including the details of the facility and the plant/machine for inspection,
– a checklist with the steps of the inspection procedure to be taken by the service technician to the site,
– documentation of the machine/plant in question with further details of its operation or maintenance guidelines,
– service log for the service technician to complete during the inspection, entering information about the items he has verified and their condition,
– an inspection report based on the service record for the technician to complete in the office after returning from the site, which, later on, has to be sent to the client as proof of the completed inspection,
– and let’s not forget about the paper invoice for the inspection sent out at the end of the process.
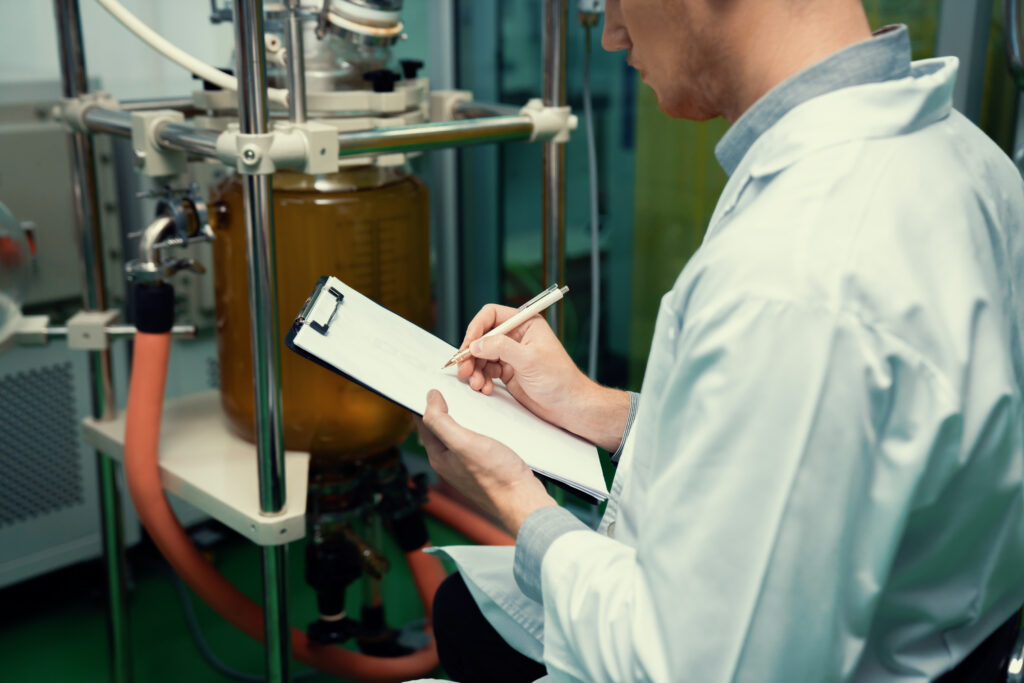
Benefits of paperless manufacturing
Efficiency
Going digital allows for better resource management. All relevant information and documents can be distributed instantly across the company. Access to essential files is open 24/7 from any location, which means no process will be halted due to hampered availability. Transferring paperwork online equals no more delays in executing tasks caused by missing documentation, no more waiting for the traditional mail to deliver manuals or paperwork to the decision-makers.
Cost reduction
Spending reduction is associated not only with cutting on paper, printers, and toners (and staples, paper clips, folders, punched pockets, binders, you name it). It’s worth remembering that all the meticulously crafted paper documentation requires dedicated storage spaces, often along with safety deposit boxes, security, and dedicated disposal procedures carried out by external providers. Going paperless involves certain expenses to establish the infrastructure and related matters, but in the long run, operational costs of paperless manufacturing are reduced compared to traditional approaches.
Sustainability
Reducing paper documentation is beneficial not only for the company’s accounting. Smaller demand for physical assets (paper, ink, dedicated office paraphernalia, fuel for their transportation, etc.) translates into reduced environmental impact. Of course, digital tools aren’t 100% green, as electricity doesn’t grow on trees, and neither does the IT infrastructure. However, in a world where more and more power is generated from renewable energy sources, utilizing software solutions over physical assets contributes to sustainable resource usage.
Improved flexibility
The ability to centralize the content and its editing within the organization, which results in immediate employee access to documents in force. As a result, companies optimize their operational efficiency, as processes can be executed dynamically.
Automation potential
The paperless concept has great potential for automating internal flows, related processes, and events involving documentation (e.g., employees used to fill in, deliver, sign, print, and scan). In the digital-based environment, most of these manual actions are redundant and things can happen almost on their own.
Knowledge management
Preparing multiple versions of the same documentation, but in the form of files drafted for a specific action, situation or event is way more convenient in the digital form. For example, in the case of a 200-page machinery documentation, we have to use it in various situations – during training, repair, maintenance, or inspection of the machine. A digital version allows for dividing such an extensive manual into 10, 20, or 50 bite-size instructions, each tailored to the specific situation in which it’s applicable. Such an approach makes it easier for employees to use documentation, reduces the risk of mistakes, and saves time when searching for information.
Better metrics assessment
Shifting away from the paper-based approach towards the digital form enables easier measuring of processes previously based on paper, which is difficult to assess from a birds-eye-view. With digital tools, we precisely know who used a resource, when, and for how long, concluding this, identifying inefficient processes, and making improvements.
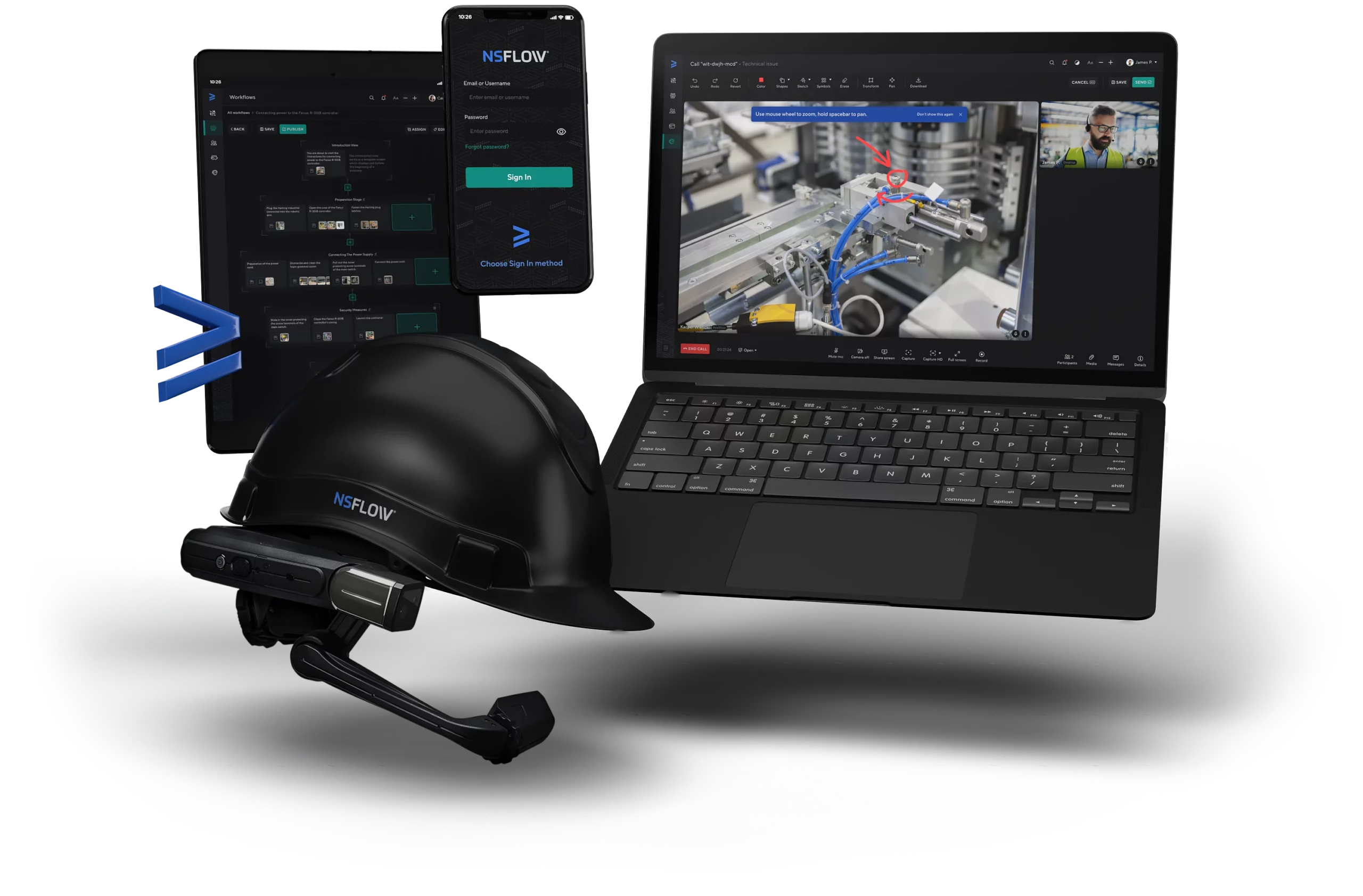
presentation to try
Nsflow in action
Disadvantages of going paperless
Every silver lining has its cloud, and while we’re all for clouds when it comes to improving industrial operations, we also know that the paperless concept has some downsides.
Security matters
Paper documentation provides certain risks (it’s easier to get lost or stolen during transport, it might be mistakenly placed in a shredder, burnt in an unfortunate accident, etc.). However, paperless documentation contains dangers as well. Digital documents can be vulnerable to hacking, viruses, and other security breaches. Without proper security measures, sensitive information can leak, endangering operational continuity and the company’s reputation.
Hardware malfunctions
In extreme cases, paper-based processes can be executed even by candlelight. Of course, that’s an extreme case, but physical documents rely on technology to a lesser extent. Going paperless makes the process dependent on power, internet access, software updates, etc. While industrial processes, in general, are rather energy-consuming, in this approach, events like server downtimes can impede personnel from executing their tasks without access to vital files.
The human factor
The organizational shift toward digitalization may create barriers to information sharing and in-house collaboration, as some staff members may lack the skills to access electronic documentation. Going paperless calls for attention during the implementation and execution phases to ensure personnel has the necessary resources to execute digital processes efficiently and error-free.
Legal matters
Legal regulations on data storage vary from country to country. Hence, regulatory requirements for retaining documentation may entail additional efforts and resources to ensure full compliance.
Technologies used in paperless manufacturing
The paperless concept goes way beyond just scanning paperwork, switching to shared drives and online calendars. The digital transformation of manufacturing in going paperless relies on the following:
Manufacturing Execution Systems (MES)
Software systems that help manage and control the production process. MES provides real-time information about the status of production processes, which can be used to make informed decisions about scheduling, resource allocation, and quality control.
Electronic Document Management Systems (EDMS)
EDMS helps manage the flow of documents and information within a manufacturing company. One can use them to store, manage, and share documents such as work instructions, standard operating procedures, and quality control records.
Barcode and RFID technology
These technologies are used to track and manage inventory and production processes. For example, barcodes and RFID tags can be attached to raw materials, work-in-progress, and finished goods to track their movement through manufacturing.
Extended reality (augmented, virtual, mixed reality)
XR technologies can be used to provide workers with visual aids and training materials, substituting paper documentation. Digital workflows and guides are convenient to update and distribute company-wide and accessible 24/7 to all cleared employees.
Digital twins
The digital representation of physical objects is one of the most promising technologies used in the manufacturing industry. A physics-based model reflects the assets, including their properties and behavior. As a result, digital twins not only boost time-to-market. Tangible advantages cover improved customer satisfaction, product quality, productivity, and cost-efficiency.
How to go paperless?
The shift from paper-based to paperless manufacturing is a process that requires some preparations and insights to be appropriately executed. From understanding existing processes and the data generated to choosing the right software provider, gathering requirements, launching the solution in-house, and monitoring the process. While it may appear as too much hassle, we’re sure that going paperless is worth the effort.
Paperless facilities see benefits including shorter lead times, better traceability, elimination of tasks of low value-added, and, in the long run – improved operational efficiency.
Ready to manage, coordinate, and execute your industrial processes with digital solutions and digital only? We’re here to help and address your concerns – let us know how we can help you with going paperless.