It’s the end of manufacturing as we know it (and we feel fine).
Now that you can’t unhear the 1987’s hit by R.E.M we just paraphrased, let’s get straight to business.
The ongoing Fourth Industrial Revolution, or as we more often call it, Industry 4.0, changes the way processes are carried out. The manufacturing we used to know – heavily dependent on paper documentation, in-person inspections, prone to human error, and burdening employees with repetitive tasks, is becoming a thing of the past. Read more on how Industry 4.0 (re)shapes today’s manufacturing.
Digital transformation
The process of executing organizational change with digital technology. Aimed at creating processes and services or modifying the existing ones. For the better, of course.
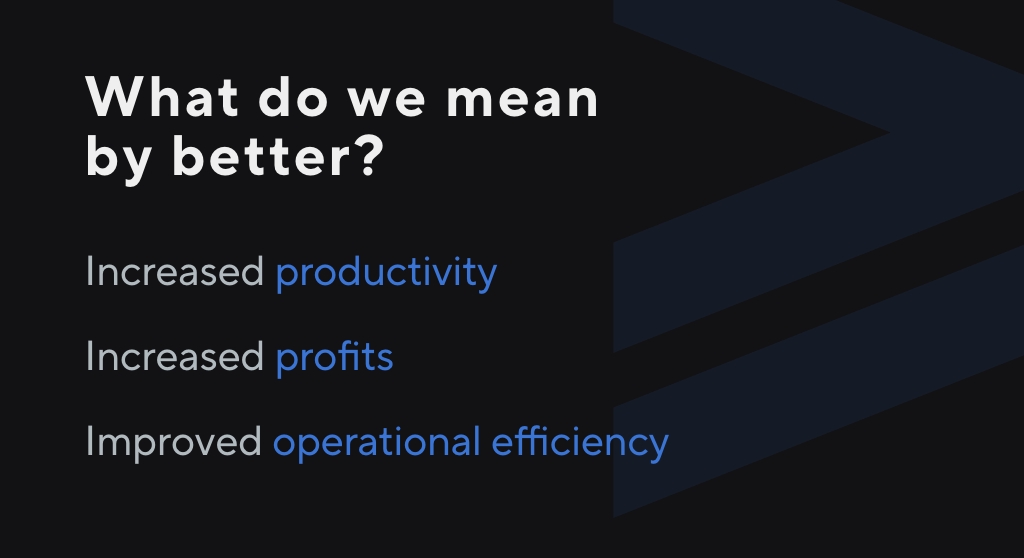
The growing adoption of technologies reflects global trends influencing nearly every industry, manufacturing included. In short, identification of areas suitable for the adoption of digital solutions and their successful implementation is more and more often the key to remaining competitive in modern business environments.
How does digital transformation enter manufacturing?
In the perfect conditions, companies drive the change by adopting the right technology, based on recognized needs and insights. In other situations, however, the changes occur due to external factors. For many companies, the spring of 2020 was the start of an unplanned, unprepared digital transformation.
The change needed to happen as the pandemic stroke, sending thousands and thousands of office employees home to work remotely. Incidentally showing how many companies weren’t ready for the shift, and often chose digital solutions (e.g. communicators) at random. Not every communicator available on the market could handle the sudden increase in the number of users, and, since the choice was in many instances done hastily, some tools weren’t appropriate to tasks assigned.
Manufacturing plants often face greater risks in their operations compared to issues in case the chosen software allows online meetings for a certain number of participants. The technological shift in industrial companies started before recent global changes, and its aim is to secure companies’ interests in the long run by adopting the right solutions.
What areas of modern manufacturing can benefit from adopting digital solutions?
Smart manufacturing
The technology-powered approach is driven by Internet-connected machines employed to oversee the company manufacturing process. Using advanced data analytics and identifying opportunities for automation, enterprises improve plants’ performance. The smart part stands for including interconnected devices, like sensors and beacons, and backing the insights they gather with computing power. Smart manufacturing results in better access to real-time information on the production process, allowing managers to quickly respond to changes, adjust to urgent demands, and correct errors.
Internet of Things
IoT is based on connecting all electronic equipment to the Internet, allowing a dialogue between devices. With the combined potential, IoT solutions provide a greater understanding of occurrences, allowing improvement in carried out processes, e.g. energy efficiency and safety. With easy 24/7 access to critical data and software providing business insights into manufacturing operations, interconnected devices give an advantage over manufacturing plants still relying on analog data-gathering and analysis. The more robust the process, the faster changes can be applied to answer changing needs or respond to occurring events, e.g. downtimes.
Augmented reality
AR is a versatile, powerful ally to manufacturing companies, improving various areas of modern production. Using augmented reality in predictive maintenance enables preventing downtimes by eliminating machinery failures. Unexpected breakdowns become less of a threat in facilities where workers can supervise equipment and access its condition anytime without halting the processes, not necessarily waiting for scheduled inspections.
Employees armed with AR-powered wearable devices are more efficient on the plants’ floor, executing their tasks hands-free. With direct access to aggregated knowledge and real-time communication with remote experts, on-site workers can independently perform tasks previously requiring the presence of other specialists.
Automation
In the upcoming years, manufacturing will become free from obsolete processes. The shift is already visible, as widely used solutions enable automating repetitive tasks, streamlining machining transfer lines, assembly machines, chemical production processes, and conveyor systems. Aside from improving productivity, automation helps to reduce exposure of the workforce to hazardous conditions.
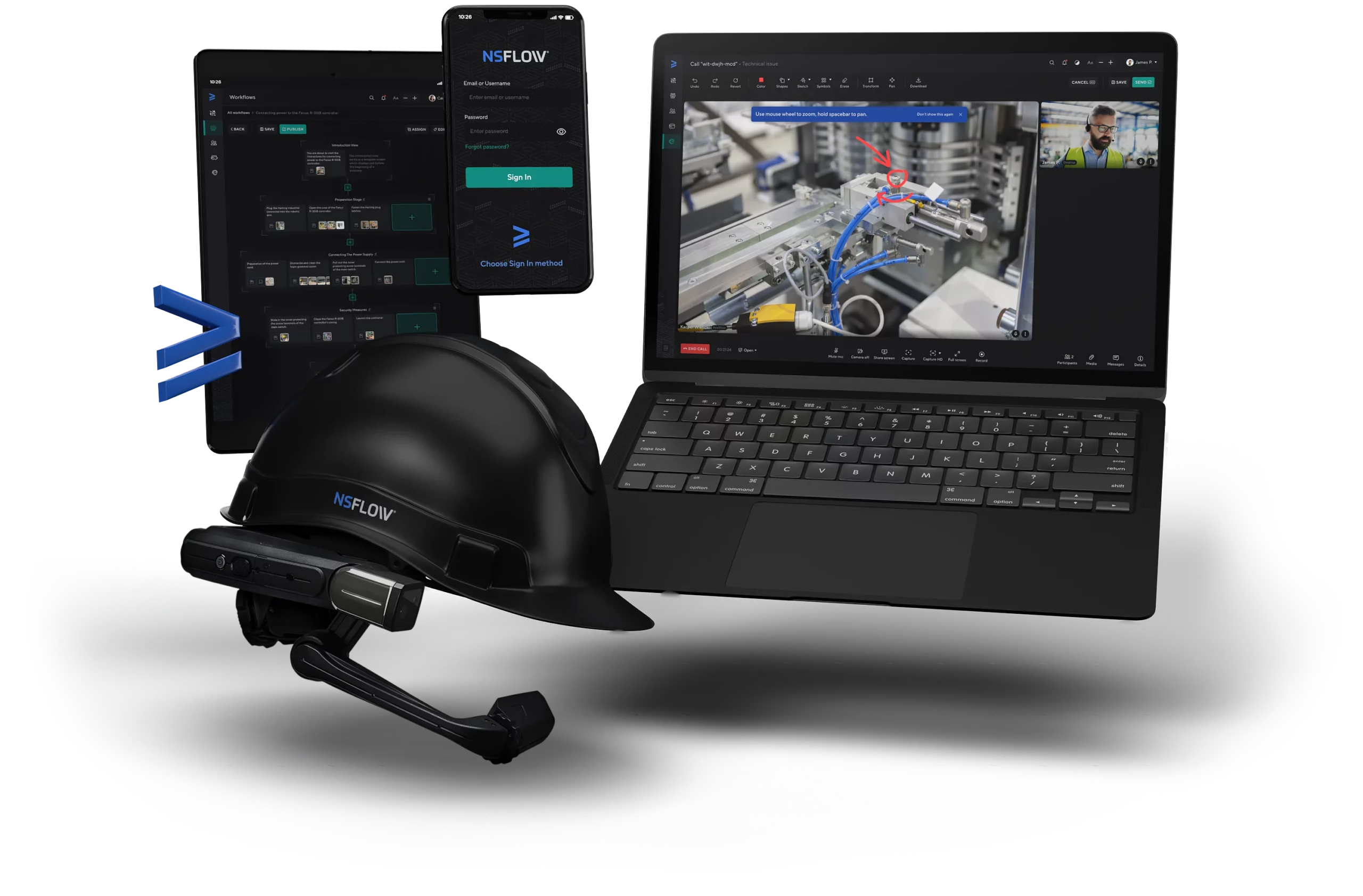
presentation to try
Nsflow in action
What does digital transformation mean for manufacturing employees?
With the growing adoption of digital technologies, the demand for certain positions decreases. Fewer employees are now necessary to fully assemble a car or mix chemical compounds, but that doesn’t mean that the manufacturing field will from now on depend solely on the machines and software powering them. When thinking about Industry 4.0, companies – or their managers, to be precise – often focus heavily on new technologies, paying far too little attention to employees who will take care of operating the implemented systems.
Keeping staff out of digitalization processes will sooner or later compromise operations, especially when management won’t put effort into convincing employees to digital solutions. To accomplish digital transformation goals in manufacturing, companies need to focus not only on technologies but on people who will use them in their professional daily routines. Only this approach allows manufacturing entities to fully benefit from the ongoing digital shift.
The needs change, and so do the requirements. Embracing technologies in manufacturing operations, companies need highly trained staff even more than before.
This may sound a tad ominous, but there’s no escape from digital transformation. The question now is, will companies approach it deliberately, or it will just occur by itself. It’s not hard to guess which attempts at improving and changing processes are more successful.
Do you want to explore further how industrial processes transform digitally? Download the free ebook, and read more about augmented reality in industrial processes.
Finished the ebook and ready for more? Book the free demo, and see how your manufacturing facility can transform digitally with AR.