Digital transformation in manufacturing
The noticeable switch of manufacturing companies toward digital technologies originates from the constant need for greater production efficiency, better quality, less waste, and maintaining operational efficiency. Changing the approach from the popular “made-to-stock” to “just-in-time” production allows for minimizing inventory and warehousing costs. The “just-in-time” model can be achieved relatively easily by introducing digital solutions and information processing systems.
The “just-in-time” model takes into account planned downtimes, but could the process become even more efficient? Avoiding interruptions in production is vital for the efficient achievement of manufacturing objectives.
Everything maintenance
Predictive maintenance (PdM) is a condition-based maintenance type relying on data from monitoring tools and sensor devices. With advanced PdM systems, the assets’ status, health, and performance are tracked to predict undesired events. As a result, maintenance experts are unburdened from direct supervision of processes, thanks to alerts rising from analysis and prediction fueled by extensive datasets.
Breakdown maintenance is an example of a reactive approach, where maintenance and service are performed once machinery has stopped working due to malfunctions or wear of parts. This type of maintenance aims at responding to occurring breakdowns.
Another approach to avoiding production obstacles is preventive maintenance. In short, it focuses on fixing things before they break – based on preset rules and recommendations. Preventive maintenance bounds technicians and engineers to respond according to guidelines, even though there may not be an actual need yet (but there’s no information available about the current state). Without waiting for the malfunction to occur, maintenance technicians perform regularly scheduled actions to meet the needs of the machinery in question. A popular example of preventive maintenance in everyday life is changing the oil in cars. Most car manufacturers advise users to perform the operation once in an assumed while (e.g., every 12 months or 15000 kilometers). Drivers aren’t supposed to wait until something bad happens to the engine and should follow the instructions, even though seemingly everything is fine.
Preventive maintenance in manufacturing isn’t the go-to approach, as halting the lines to replace expendable parts or change oils also means downtime (however, in this case, a planned one). Predictive maintenance requires more financial investment in the implementation phase but allows for significant savings in the process. On the other hand, preventive maintenance is less costly as a process but can result in more downtimes overall, entailing costs as well. The difference is noticeable in the long run, as halting the production process affects operational continuity.
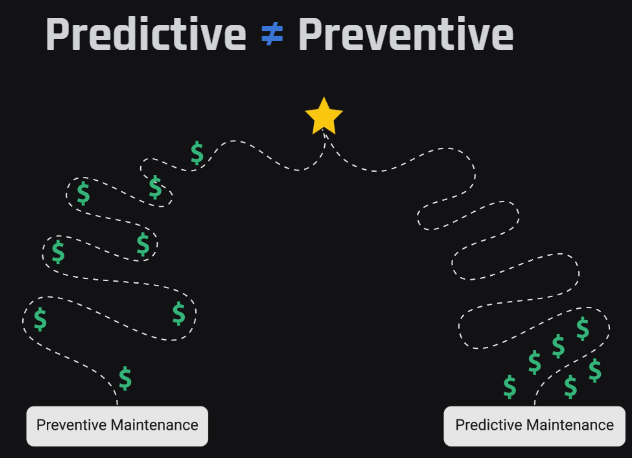
So, if the machine could safely and efficiently work a little longer until the slightest symptoms of an upcoming need for service or maintenance occurs, why not let the line work a little longer uninterrupted? And now for the solution that makes the above approach possible instead of just wishful thinking.
Digital twins
The digital representation of physical objects is one of the most promising technologies used in the manufacturing industry. Being one of the factors driving transformation toward Industry 4.0, digital twins not only boost time-to-market. Tangible advantages cover improving customer satisfaction, product quality, productivity, and cost-efficiency.
Digital twins (DT) are all about the data, from computational models to analysis, diagnosis, and prognosis. A physics-based model is utilized to reflect the assets, including their properties and behavior. Such a model aids maintenance experts and manufacturing engineers in seeing past the machine’s hood and, judging from its behavior, responding accordingly.
The state-of-the-art solution supports predictive maintenance processes. Digital twins can be upgraded through integration with already present systems in production facilities (SCADA, IIoT, MES, etc.). The synergy of industrial systems with digital twins enables more efficient execution of processes and, as a result, greater performance.
How do digital twins work?
The digital representation of physical assets requires data that it will visualize. So, instead of (or: atop of) building CAD projects and cardboard prototypes, manufacturers can launch digital models to test the machinery’s behavior.
Digital twins can be incorporated in the Failure Mode and Effects Analysis (FMEA), allowing technicians and engineers to constantly monitor equipment and processes, collecting data on the actual performance for comparison with expected performance. Being a more and more popular monitoring solution, DTs improve flexibility and, as a result, help adjust the manufacturing facility to the dynamic market and its requirements.
The digital model can be created as a prototype for machine/equipment development, and serve this role in the early stages prior to launch. Once the machine/equipment is ready to operate, the digital twin can continue to monitor its operations, becoming a part of the predictive maintenance approach.
Digital twins are also created to support processes related to already existing and operating machines and be used in, e.g., employee training. Depending on the needs and capabilities, digital assets can be modeled using CAD projects or by performing a 3D scan and can require the installation of additional sensors and beacons for data acquisition. This means that even old machines can be monitored digitally, reducing the workload of maintenance personnel in supervising equipment performance.
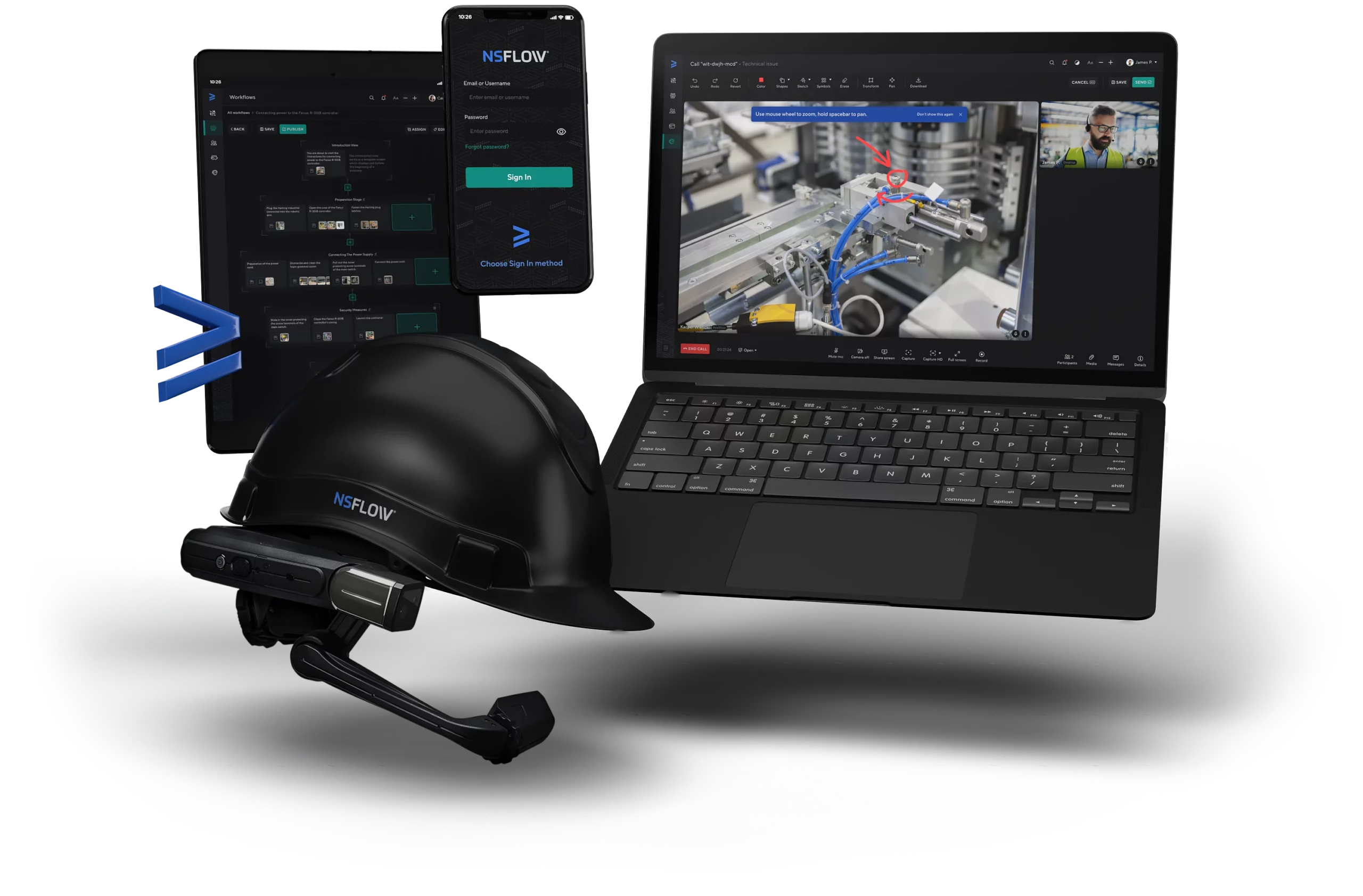
presentation to try
Nsflow in action
Are digital twins worth the hassle?
We mentioned in the introduction that digital twins could improve cost efficiency, but how exactly do virtual models help with savings?
Fewer prototypes
Many parameters, functionalities, and characteristics can be assessed in digital models. The prototyping process can be significantly shortened and cheaper in execution without the need for a physical representation of the examined object.
Fewer errors
Engineers and technicians can identify machinery or equipment errors before malfunctions occur. Detecting failures in early development stages allows for the elimination of anomalies prior to launching the product or process.
Monitoring & feedback
Digital twins streamline processes through the opportunity for instant communication of detected abnormalities and malfunctions. With DT, every action performed with the assessed object can be immediately corrected in case of errors made by operators. Negative results are reflected by data gathered in the DT, visualizing the trouble spots on the virtual model.
Digital twins facilitate change management, enabling easier machine or production line modifications, compared to traditional models. With the use of DT, engineers can verify the results of applied changes and their impact on other systems – in a faster and more cost-efficient way.
Reduced carbon footprint
Digital twins allow not only for savings but also for environmentally aware changes in industrial processes. With the reduced need for traveling between locations to supervise physical assets, fewer prototypes, and documentation, the carbon footprint decreases.
The future of digital twins
The concept itself is already a legal adult when considering human years. While we don’t know for sure how to convert it into technology years, we’re sure that its whole life is ahead of it. The application of digital twins is growing among industrial companies, with giants like BMW and Airbus incorporating the concept into their facilities. What needs to be said is that digital twins aren’t a solution just for huge manufacturing entities and large factories. The concept can be successfully adopted in every industrial company with machinery parks and production lines. There are no limitations for digital twins in supporting on-site technicians and engineers in tackling challenges in their daily work.
While DT can be created and operated without augmented reality, adopting AR solutions in industrial environments enables achieving tangible results and carries great potential for future uses. Are you interested in launching digital twins in your facility? Let us know, and we’ll be happy to advise you on the process.