What is a Digital Twin?
The digital representation of physical objects is widely used in the industrial context. Digital twins are advanced successors to CAD models, popular due to their usability in manufacturing processes. Using dedicated software, manufacturers can run tests and simulations on digital twins, combining large datasets. With the reduced need for physical prototypes on design and testing stages, the process can be executed faster and more cost-efficiently.

The concept of digital twins reached a wider audience in the 21st century, but the idea itself made an impact over 50 years ago. In 1970, Apollo 13, the seventh manned mission of the Apollo space program left Earth. The crew faced onboard malfunctions caused by an explosion leading to the rupture of an oxygen tank. Ground control supported the crew remotely, preparing an improvised solution with the equipment available aboard the craft, backed with the most advanced (at the time) simulators. Once the patch was approved, the crew recreated the solution in space, coming safely home from the endangered mission.
However, far from today’s understanding of digital twins, what saved the Apollo 13 crew was its prototype version. The representation of target conditions enabled mission control to rapidly adjust to occurring events, providing a successful solution.
How do digital twins work?
Working with digital twins requires collecting real-time data describing the object to be represented – its parameters, functions, dimensions, physical condition, etc. The gathered and structured datasets are integrated through data collecting tools for further analysis. The software of choice generates the digital representation to undergo further operations – ready to mirror real machines and objects. From this point on, it’s up to end-users how they wish to utilize the digital potential in their workplace.
Industrial adoption
Digital models allow designers to try out and compare countless possibilities, many of which could be out of reach using traditional measures. With the growing adoption among industrial companies, 3D representation of physical assets accompanies products during the whole lifecycle.
The process enables the assessment of assumptions prior to purchasing materials necessary for the physical units. Because of the immense possibilities, digital twins are highly valued in the automotive and aviation industry, streamlining the design and manufacturing process of engines and fuselages.
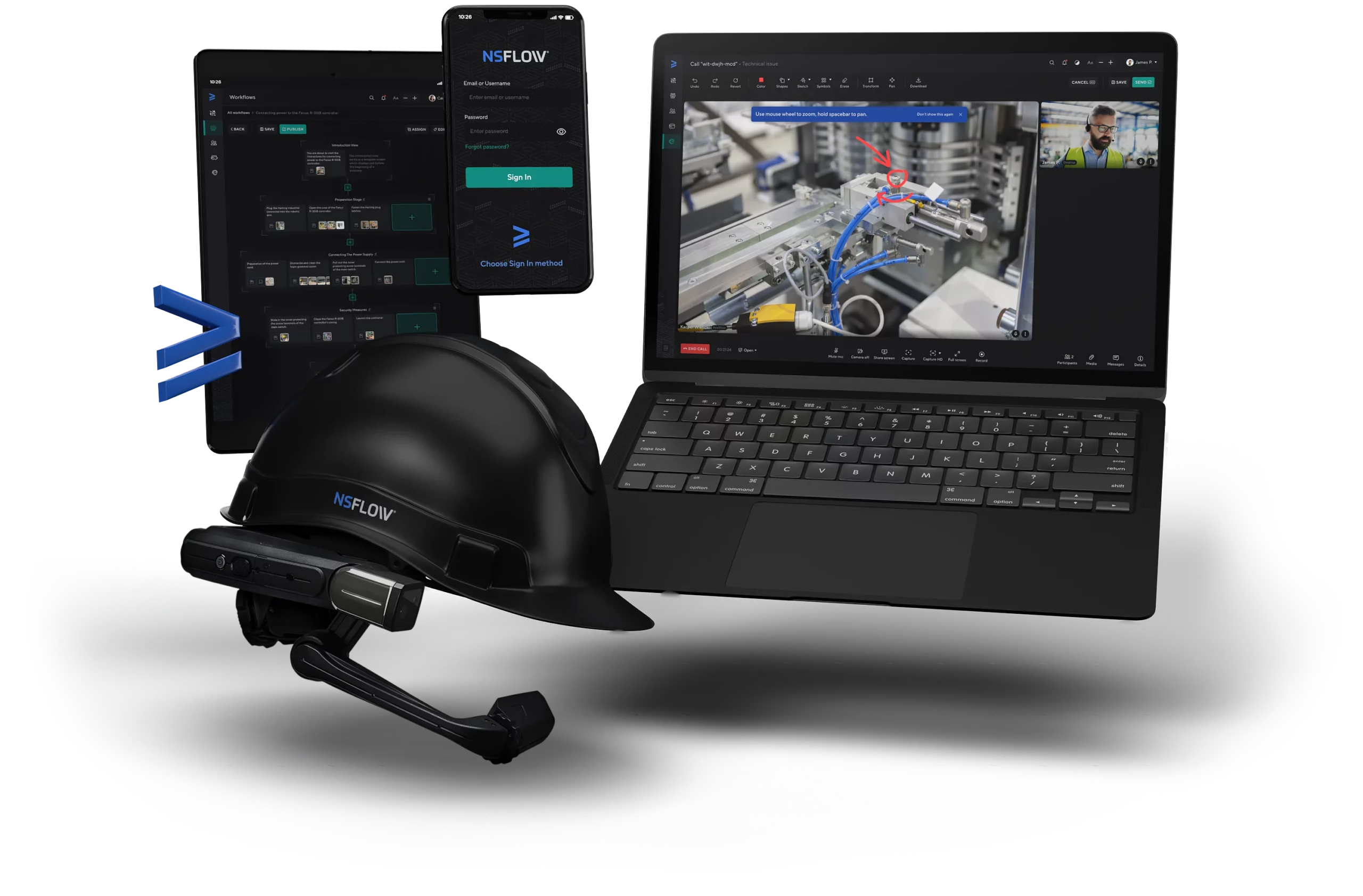
presentation to try
Nsflow in action
Digital twins are commonly used in maintenance prediction
One of the first adopters of digital twin software for physical assets was General Electric. The tech giant uses virtual models to predict the degradation of their GE90 engine known for powering Boeing 777 aircrafts. High-fidelity simulation software creates virtual models of components and complex systems. The 3D digital representations allow users to experience the environments and conditions the components and systems will be subjected to in operations. Boeing themselves achieved a 40% improvement in parts and systems quality thanks to simulations and digital twins.
Manufacturing
Another aviation-related example of digital twin technology is the cooperation between the U.S. Army Aviation and Missile Command and Wichita State University, whose aim is to “open a new door to aviation maintenance and sustainment”. Or, simply put, improving the process of manufacturing parts for the military helicopter, UG-60, the popular Blackhawk.
Converting 2D drawings into 3D parametric models and scanning a physical example will help to produce necessary parts anytime they’re needed, unaffected by inconveniences of the supply-chain issues. The solution enhances the training of military mechanics and technical inspectors’ skills, without jeopardizing the integrity of physical helicopters used. The benefit? Increased exposure to vital parts, convenient repetitions of maintenance tasks, and no harm done to the real machine.
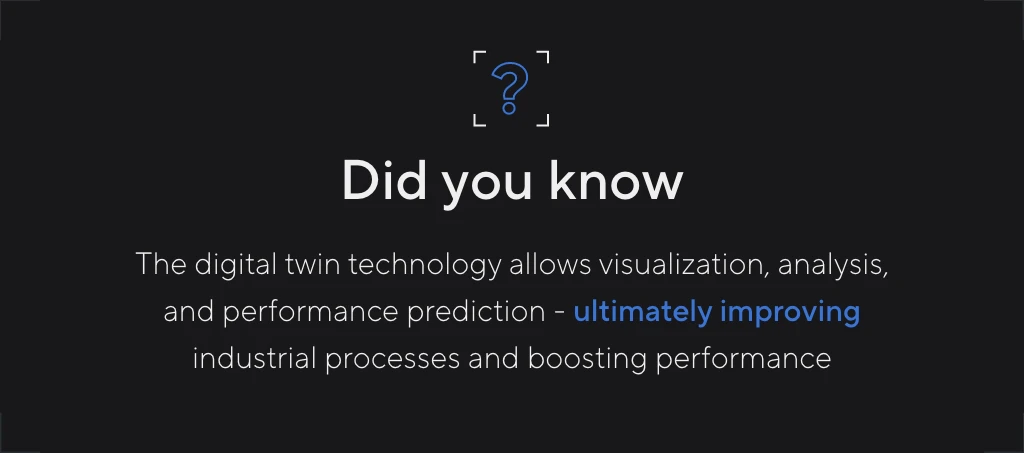
Benefits of using digital twins in industrial companies include
- maintenance optimization
- reducing downtimes
- cost reduction
- creation of connected products and services
- monitoring assets
- reduced risks
The digital twin concept brings involved parties closer to the build, improving connectivity. It can be achieved by using various, numerous technologies. In addition to the above-mentioned benefits, the concept allows storing complete documentation about the object within the digital twin’s structure and collaboration within a digital twin to the needs of various projects execution, related to the object.
Augmented reality enhancing digital twins
AR carries an undoubtable potential for industrial processes, and one of the fields where it blooms fully is the usage of digital twins. Taking advantage of 3D models and computer-generated visuals representing real-time data improves the quality, security, and continuity of manufacturing processes.
Users equipped with AR devices have access to digital representations of machinery and other on-site physical objects. Employees using augmented reality can operate without the need for stopping the work and disassembly of the build.
Digital twins are the future
The potential for digital twins in industrial areas is endless. Granting industry professionals access to real-world data and a chance to experience first-hand the working environment, digital technology will continue its victorious march in manufacturing. The adoption of digital twins and its impact on reducing costs through minimizing downtimes with predictive maintenance and streamlining other industrial processes will only increase in the upcoming years.
Digital twins are disrupting industrial processes, together with augmented reality opening doors for modern and efficient operations. Do you wish to read more about AR and how it can improve your processes? Download the free ebook in which we gathered answers to the most common questions regarding the adoption of AR in industrial environments.
Are you ready to employ digital twins in your company? Try our free demo, and see how AR can drive industrial change in times of Industry 4.0.