Is augmented reality the right tool to boost customer experience?
Answer the public
Mass production, the process of manufacturing large batches of standardized goods using mainly automated assembly lines, answers multiple market needs. Production automation is necessary due to the demand for large quantities of similar products. Or is it? Well, that depends. You probably know the global fast-food chain with a goldish logo, don’t you? A few decades ago, in order to reduce queues, improve customer service, and obviously, their profitability, that business decided to introduce full standardization. Regular bun, 7 grams of greens, one onion slice, a shot of condiments, followed by a patty identical to millions of others sold around the world. All prepared in a default scheme.
Less time spent on making orders, fewer dilemmas while choosing from available options, and naturally, shorter preparation time compared to custom orders. Millions of clients are pleased with the repeatability of results, enjoying the standardization across all facilities. Fast forward a few decades, and you will see that even the most unified, rigorous chains are now accepting order customization; however, to an extent. Other businesses managed to bloom from the customers’ desire for far-reaching individuality and customization. While there’s no one-size-fits-all in this matter, and probably the advocates for each option will die on their hills, it’s hard to deny we live in times where customized production becomes more and more important.
What is mass customization in manufacturing?
The business process of delivering goods and services that meet individual clients’ needs stands on the shoulders of giants: integration, flexibility, and personalization, all of which contribute to delivering bespoke products for similar unit costs to mass production offerings. Mass customization aims to offer growing convenience to clients and meet their non-standard requirements.
Industry 4.0 supports flexible manufacturing and mass customization
The newest technologies drive visible change in production processes. From the Internet of Things to big data, artificial intelligence, additive manufacturing, advanced robotics, and virtual and augmented reality – modern manufacturers are armed with the fourth industrial revolution’s unique tools. AR is one of the game-changers, enabling a boost of operational flexibility and performance leading straight to customization.
This may not be the first guess when it comes to the application of AR in industrial processes, but digital twins play a significant role in product customization (aside from e.g., maintenance). Using technology, manufacturers can create twins of products, already used by clients, and work on these representations. As a result, designers can try out concepts in a more convenient way compared to traditional manufacturing. Digital models backed by advanced software and sensors gather data and configuration details to mirror the looks and behavior of created parts and objects. Creating virtual imagery of physical objects provides immersive, life-like examples more advanced than traditional CAD models. Utilizing the AR-powered approach allows producers to bypass – to an extent – physical prototypes and try out even the most demanding designs. The opportunity opens the way not only for standardization and regular production but also for mass customization and the creation of advanced individual products satisfying specific needs. Digital twin technology is becoming increasingly popular in, among others, the automotive industry, reducing costs on the producer’s side and bringing to life advanced projects in a significantly shorter time.
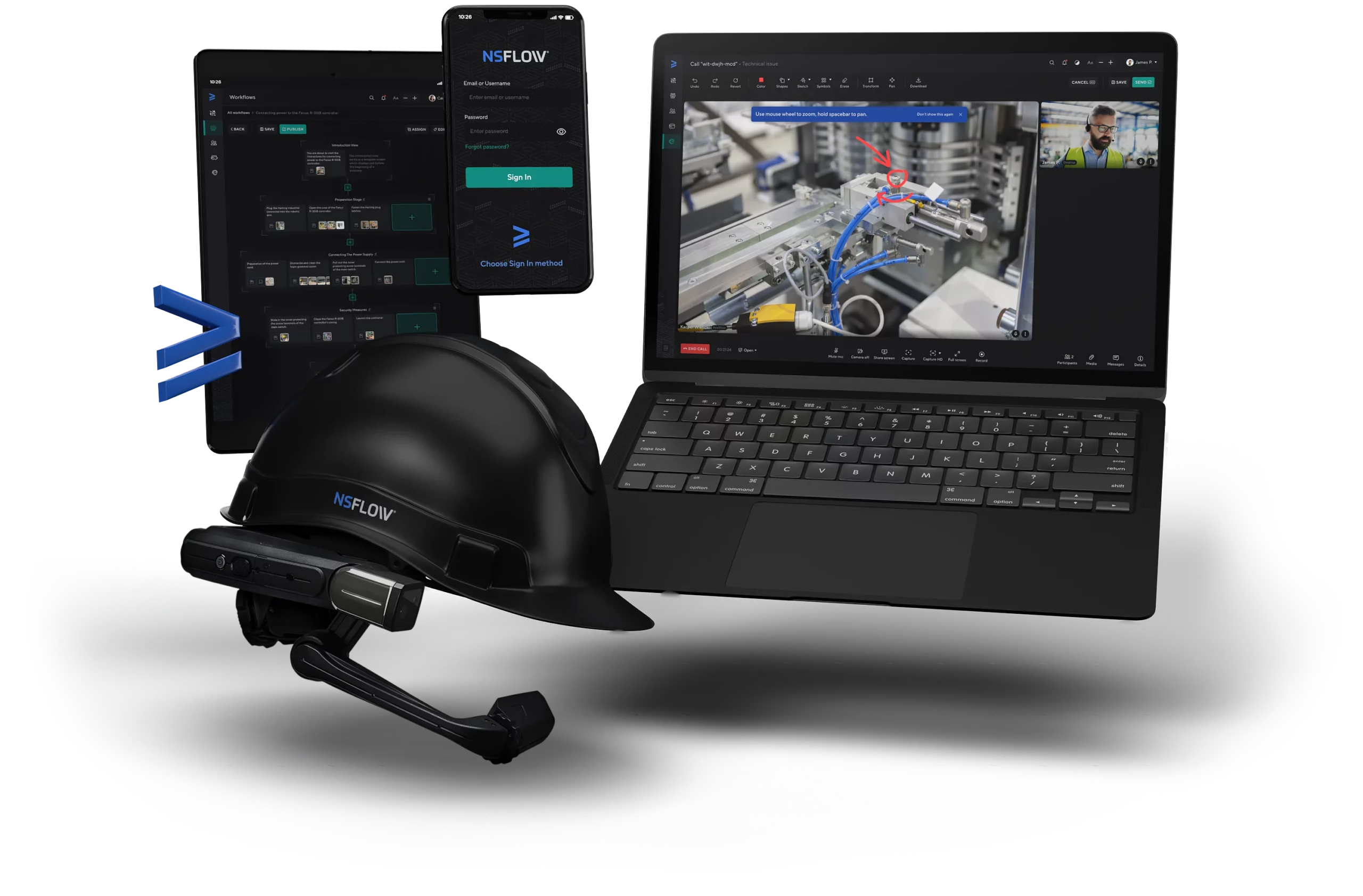
presentation to try
Nsflow in action
Examples of mass customization
Multiple case studies of customized production can be found in the FMCG industry, especially in the clothing and garment field. Global brands known for decades for their recognizable styles turned their focus toward clients oriented on high-quality products and wishing for goods suiting their tastes. From Nike to Gucci and Sergio Rossi, manufacturers developed made-to-order strategies, utilizing mass customization products to deliver individual items on a mass scale.
Utilizing digital transformation technologies like AI, IoT, VR, 3D printing, etc., manufacturers may increase the flexibility of their operations. That includes establishing new approaches for converting design criteria into production directives and improving automation by adding a digital management layer to the current FMS. The manufacturer can benefit from the expanding industries as they advance toward mass customization. Without human involvement, the integrated process can autonomously choose and swap out cutting instruments and provide raw materials and supplies. Workers are present to perform high-value tasks and to control plant operations using tablet-based monitoring tools. These bring in a fresh perspective on the fourth industrial revolution, which is currently in progress and will fundamentally alter both our current understanding of the global economy and the mechanisms controlling the way we create economic value.
Why is mass customization important?
It is crucial to improve the client experience in all areas — from the service they receive through delivery lead times up to product quality — and remain competitive and relevant to your customers.
However, the relationship with your clients may be the most appealing feature of mass personalization and manufacturing flexibility. You may get closer to customers using Industry 4.0 technology, mass customization, and flexible manufacturing approaches. As a result, you will be able to forge a stronger direct connection with customers, build your brand, foster customer loyalty, enhance your understanding of customers and the market, and ensure you keep ahead of rising trends, shifting values, and developing expectations.
Mass personalization enables manufacturers to avoid mass sampling and extensive inventory stockage yet still deliver diverse offers clients like to choose from. Another benefit of mass customization manufacturing is improved management control owing to insights from collected data which can be used in further projects, and reduce lead times. By executing a mass customization strategy, companies can downsize warehouse costs and investment in finished goods in favor of raw materials used only when needed.
The takeaway
Answering the initial question – yes, AR is one of the most efficient tools used for improving customer experience and satisfaction. Fields of augmented reality applications in everyday life continue to grow, and there’s no sign of stopping the process anytime soon. In a world enjoying individuality and low prices in equal measure, mass customization solutions are appealing and will become widely adopted across companies open to digital enhancements.
Looking for an AR improvement to your operations? See what AR can change in your industry. Already read a lot and looking for more details? Let us know, we’re happy to help.