We’ve brought up the Industry 4.0 topic a few times already. While in this article we have decided to explore one of the core aspects of the Fourth Industrial Revolution – the application of digital technology in manufacturing.
What is meant by digital manufacturing?
Although it may sound a tad surprising, the digital manufacturing definition describes the process of digital technologies’ inclusion into the production industry. It’s a well-thought-out combination of computer systems supporting services, products, and processes (e.g., supply chains).
How does digital manufacturing work?
With digital solutions, production plants develop an integrated approach to manufacturing. Technology has all it takes to connect systems and processes along the lifecycle, from product design to production and servicing end-products. There is no brief answer to the question “how does it work” since several different technologies are applied in various areas. Digital manufacturing starts with retrieving data from the carried-out processes and comparing it with insights on recognized challenges and possible bottlenecks. Once the workflow-related issues are identified, possible solutions can be considered and implemented in the organization. The observation and analysis, however, do not cease once digital production is activated – collecting data and drawing conclusions are necessary to maintain the best results along the way.
The three dimensions of digital production
Digital manufacturing is not a one-trick pony but rather a multidimensional approach, including:
Product Life Cycle
Digital solutions accompany the product starting with its design and are followed by sourcing, production, and service life. Data acquired along the journey serves a crucial role in shaping the product life cycle, from design guidelines and accepted deviations to working on the end results.
Smart Factory
This approach focuses on the automation of production processes, enhancing operations and information technology with business intelligence. As a result, manufacturing plants benefit from real-time data in factory processes, their management, optimization, performance, and improvement.
Value Chain Management
The third aspect of digital manufacturing is oriented toward optimal process integration, enhancing customer satisfaction, and optimizing inventories along the supply chain. All are meant to deliver the goods and services in an improved and more efficient way.
Examples of digital technology in manufacturing
Solutions gaining popularity across production enterprises:
Additive manufacturing
The process of building physical objects one layer at a time. The umbrella term covers several additive technologies including material jetting, powder bed fusion, and material extrusion. tarting with a CAD model and a batch of building material under the watchful eye of dedicated software, allows companies to save on prototyping, and creating intricate items, especially when comes to small production. Additive manufacturing also streamlines the recreation and optimization of legacy parts.
Augmented reality (AR)
AR and its sister technologies (virtual and mixed reality) brought a new quality to digital production. Supplementing the real-world environment with digital add-ons helps create an efficient and safe approach to employee training and onboarding, followed by the convenience of access to machinery at distant locations. With remote support and real-time communication with experts, there’s virtually nothing that’ll impede technicians from maintaining production lines and eliminating downtimes.
Digital twins
Using computer-generated visualizations of products and machinery reduces the need for physical prototypes in the design and testing stages, shortens processes, and downsizes costs. With the dedicated software, simulations and tests can be run with digital twins for a better allocation of resources company-wide.
Industrial Internet of Things (IIoT)
Interconnected smart sensors, instruments, and devices serve a great role in enhancing industrial processes. Seeing through the digital “eyes” allows experts to monitor the machines’ health and parameters, and respond to possible issues before they even occur. IIoT can be a powerful pillar of predictive maintenance aimed at eliminating downtimes and optimizing the manufacturing process.
Big data and analytics
With big data, manufacturers can conveniently track and analyze their processes from the bird’s eye’s view and, as a result, streamline their execution. At the same time, production supply chains, a core aspect of manufacturing efficiency, are overseen to recognize patterns and variables. Collecting and analyzing data is introduced to enhance processes and boost efficiency by fixing issues invisible to the naked eye.
Automation
Fixed automation, programmable automation, flexible automation, and integrated automation – are all meant to allow enterprises to secure their market position by boosting productivity and sustainability by ceding various activities to machines.
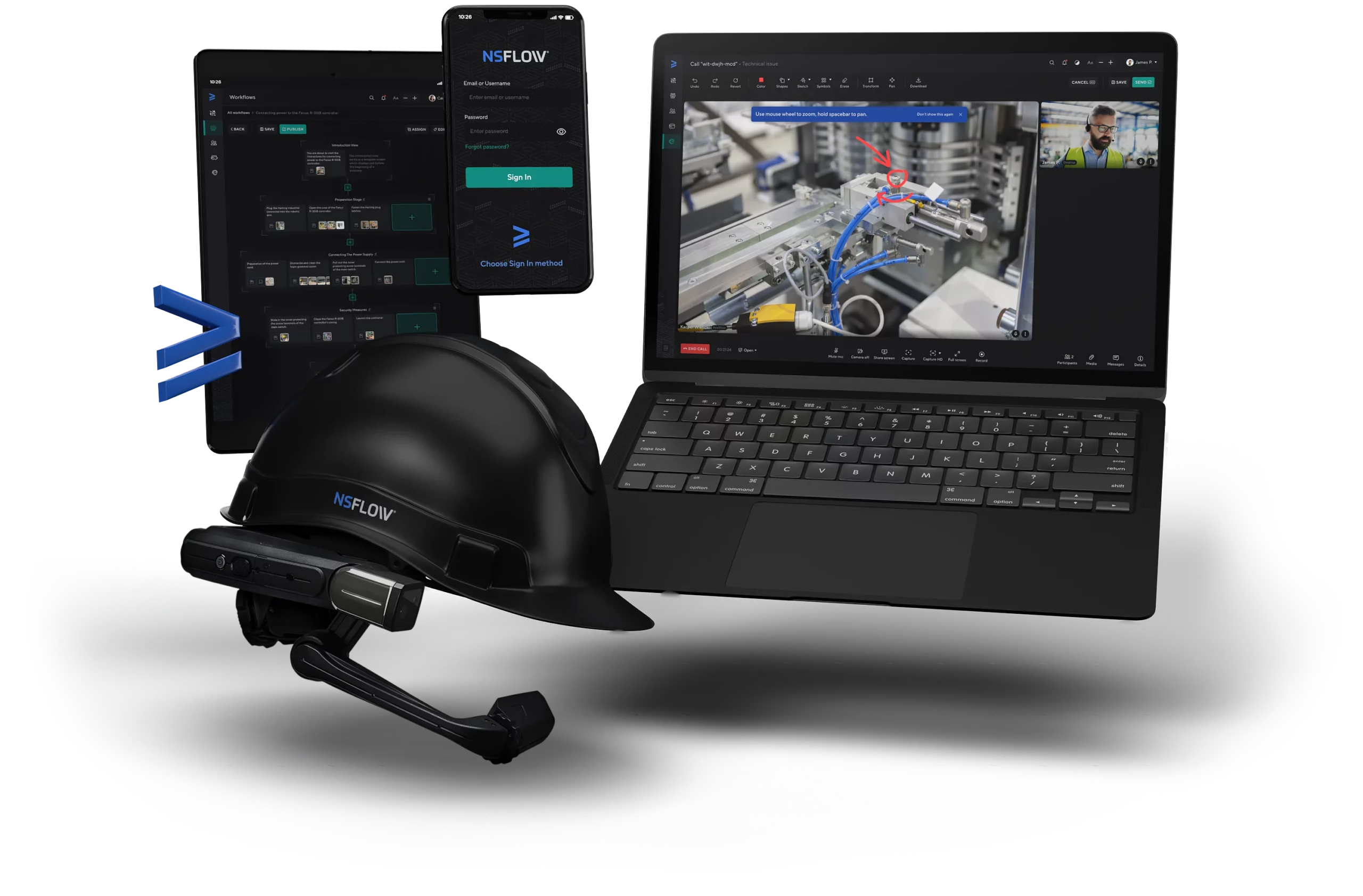
presentation to try
Nsflow in action
What is the need for digital manufacturing?
The term digital manufacturing covers various technologies used across the industry to streamline production processes. The growing desire to transform production plants arises from recognized needs and requirements. With high probability, great majority of factories would use some help with optimizing efficiency, better production scheduling, creating precise forecasts and analyses, and delivering products faster to the market.
How has technology changed manufacturing?
Some aspects are mentioned more often than others, but the general benefit for manufacturing plants is an improvement. Automation of production lines that allows for more error-free, easier to re-program, and adjusted to current requirements manufacturing. Hazard reduction, which is achieved through ceding the most dangerous tasks to digitally operated machinery. Fewer costs thanks to better resource management, reduced number of downtimes and errors, and, last but not least, shortened design processes.
Improved manufacturing is possible with the support of technology and can be achieved even with enhancements considered minor from the enterprises’ perspective. Therefore, even if your production plant is not yet ready to introduce e.g., programmable automation, give augmented reality a shot and see how your processes become more efficient.