What is Lean Manufacturing?
Lean Manufacturing is a methodology for minimizing waste and maximizing efficiency in the production process. It is a customer-centric approach based on the principles of continuous improvement and the elimination of non-value-adding activities. The goal of Lean Manufacturing is to create more value for customers with fewer resources, less effort, and less time. This is achieved by optimizing the flow of materials, information, and people through the production process, reducing inventory levels, and improving output quality.
The Lean methodology was developed by Toyota in the 1950s and has since been adopted by many other manufacturing companies around the world, including automotive, aerospace, oil and gas, and has proven to be an effective way to increase productivity, reduce costs, and improve customer satisfaction.
Importance of Lean Manufacturing in the business environment
The Lean Manufacturing approach has become increasingly important in the business due to its ability to improve operational efficiency, increase customer satisfaction, and reduce costs. By minimizing waste in the production process, companies are able to streamline operations and optimize their resources, resulting in higher productivity and profitability. Additionally, Lean Manufacturing promotes a culture of continuous improvement, which encourages employees to identify and eliminate inefficiencies in their work, leading to further productivity gains. Moreover, as customers become more demanding, Lean Manufacturing can help companies improve the quality of their products and services, leading to increased customer satisfaction and loyalty. The adoption of Lean Manufacturing can provide a significant competitive advantage for companies, enabling them to stay ahead in an increasingly complex and dynamic business environment.
Principles of Lean Manufacturing
The five principles of Lean Manufacturing are value, value stream, flow, pull, and perfection. The first principle, value, involves identifying the specific needs of customers and providing products or services that meet those needs. The second principle, value stream, focuses on the entire production process, from the sourcing of raw materials to the delivery of the finished product. By mapping the value stream, it is possible to identify inefficiencies and remove them, resulting in a streamlined production process. The third principle, flow, aims to eliminate any interruptions or delays in the production process, ensuring that products move smoothly and quickly through the system.
The fourth principle, pull, is based on the idea of producing only what is needed when it is needed. This is in contrast to traditional mass production, where products are produced in large batches, leading to excess inventory and waste. By producing only what is needed, companies can reduce inventory levels and respond more quickly to changes in demand. Finally, the fifth principle, perfection, involves continuously striving for improvement and eliminating any remaining waste or inefficiencies. This principle is based on the idea that there is always room for improvement, and that companies should constantly be looking for ways to streamline their processes and increase efficiency.
Benefits of Lean Manufacturing
The benefits of Lean Manufacturing are plenty and span across all company’s operations. With support in identifying and eliminating waste in production processes, companies can significantly reduce costs and increase profitability. This is achieved by reducing inventory levels, optimizing workflow, and increasing productivity. Lean Manufacturing also focuses on improving product quality, which can lead to increased customer satisfaction and loyalty. By providing customers with high-quality products that meet their needs, companies can differentiate themselves from competitors and establish a competitive advantage in the market. Moreover, Lean Manufacturing can improve lead times and responsiveness, allowing companies to quickly respond to changing customer demands.
Another benefit of Lean Manufacturing is that it fosters a culture of continuous improvement. By involving employees in the improvement process and encouraging them to identify inefficiencies and waste, companies can tap into their collective knowledge and expertise. This not only leads to better solutions but also creates a sense of ownership and engagement among employees. Furthermore, Lean Manufacturing can help companies adapt to changing market conditions and improve their ability to innovate. Companies can become more agile and responsive to changing customer needs and industry trends, enabling them to stay ahead of the competition – something difficult to achieve without continuous improvement and optimization of their processes.
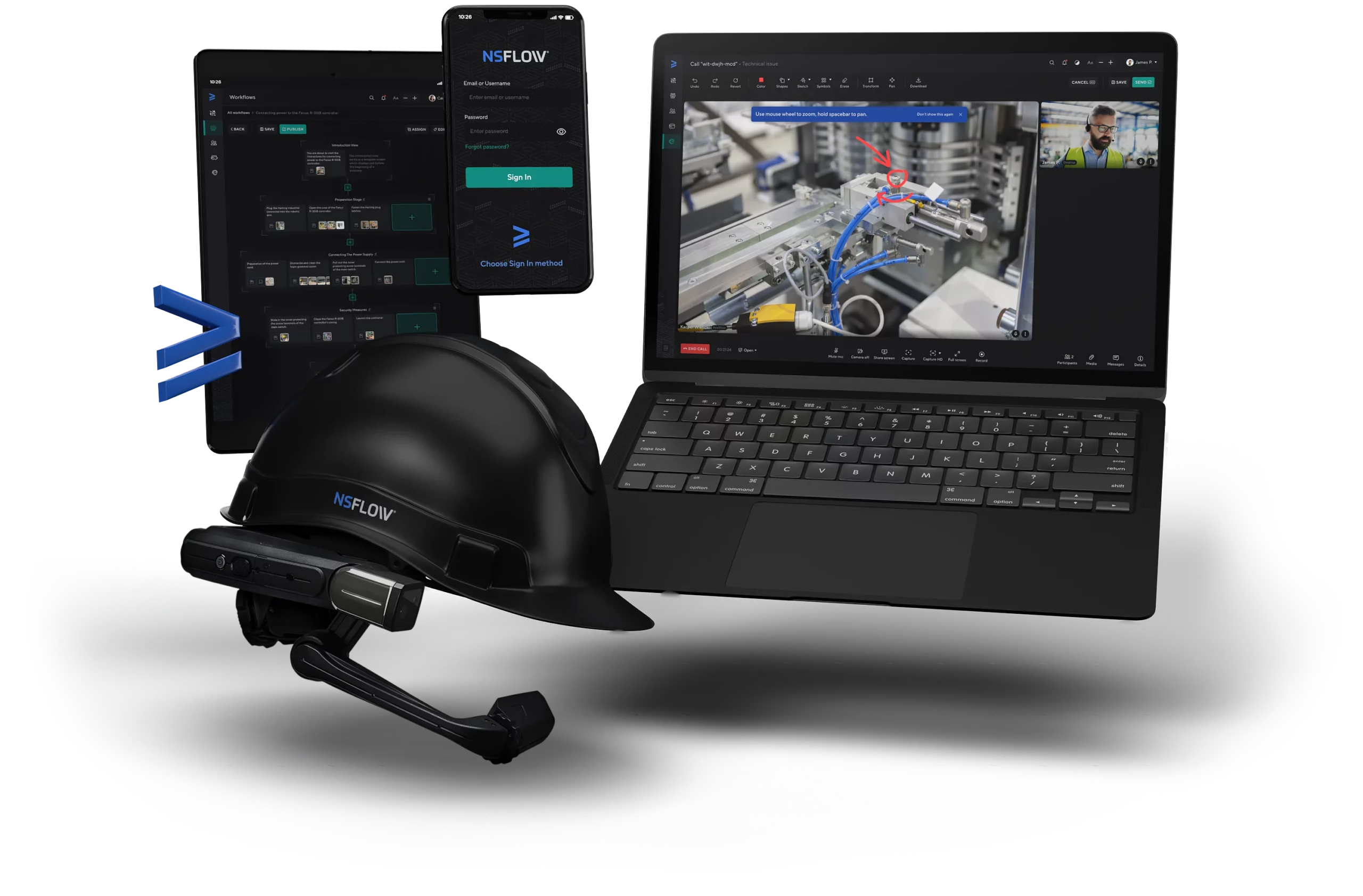
presentation to try
Nsflow in action
Which technologies and tools support Lean Manufacturing processes?
Several technologies support Lean Manufacturing and enable companies to streamline their processes and increase efficiency. Here are some of the most common solutions used in Lean Manufacturing:
Manufacturing Execution Systems (MES)
MES provides real-time visibility into the production process, enabling companies to monitor production activities, optimize workflow, and reduce waste. With dedicated systems, every occurrence in the process is recorded, analyzed, and provides data for further improvement.
Enterprise Resource Planning (ERP) systems
ERPs integrate various business processes, including inventory management, procurement, and financials, enabling companies to streamline operations and reduce costs. ERP provides managers with visibility and tools to identify wasteful processes and solutions to ensure waste elimination, wherever possible.
Collaborative robots (Cobots)
Cobots are designed to work alongside human operators, improving productivity and quality while reducing the risk of injury. With cobots, lean integrators can introduce smaller-scale automation solutions in production plants addressing the SME market’s demand.
3D printing
This technology enables companies to produce prototypes and small-batch production runs quickly and cost-effectively, reducing the need for expensive tooling. Additive manufacturing is a more sustainable approach to product creation, delivering output with less waste in the process.
Internet of Things (IoT)
IoT sensors can be used to monitor and collect data on various production processes, enabling real-time optimization and predictive maintenance. Data obtained from thousands of sensors mounted on equipment and production lines is used to identify sources of waste that went unnoticed in traditional manufacturing processes.
Artificial Intelligence (AI) and Machine Learning (ML)
AI and ML can be used to analyze production data, identify patterns, and predict future outcomes, enabling companies to optimize their processes and make more informed decisions. Algorithms provide manufacturers with data-based insights into operations, leaving no room for speculation.
Augmented reality (AR)
AR provides real-time instructions to on-site workers, allowing them to perform their tasks more efficiently and accurately. The use of AR contributes to improved productivity due to paperless processes and digital tools supporting maintenance and service procedures. Augmented reality allows production plants to reduce unplanned downtime and improve general process execution.
What is the future of Lean Manufacturing in enhancing production efficiency?
Lean Manufacturing is likely to gain even more importance in the future, as companies recognize its benefits and continue to implement its principles in their operations. Its application can lead to higher productivity, increased customer satisfaction, and a competitive advantage in the market.
Companies continue to face increasing pressure to improve efficiency, reduce costs, and provide high-quality products and services. As globalization and digitalization continue to transform industries, manufacturers are to adopt lean principles to stay competitive and adapt to changing market conditions. Lean Manufacturing provides a framework for optimizing processes and reducing waste, which can lead to significant cost savings and productivity improvements.
Furthermore, as sustainability and environmental concerns become more critical, Lean Manufacturing can play an important role in reducing waste and minimizing the impact on the environment. By focusing on reducing waste and improving resource efficiency, companies can reduce their carbon footprint and contribute to a more sustainable future. Additionally, the integration of Industry 4.0 technologies is likely to further increase the importance of Lean Manufacturing, as companies seek to leverage advanced technologies to optimize their processes and make more informed, data-backed decisions in real-time.