Hiring costs in manufacturing
The manufacturing industry faces various challenges in hiring and onboarding new employees, including a shortage of skilled workers, high turnover rates, and the need for specialized training. With an aging workforce and a lack of interest in the industry among younger generations, finding qualified candidates with the necessary skills and experience is becoming increasingly difficult. This shortage of skilled workers can result in longer onboarding times and multiplying costs associated with recruitment and training.
The cost of hiring an employee in the manufacturing industry varies based on several factors, including location, job responsibilities, and required skill sets. As a rule of thumb, manufacturing jobs may require a higher level of technical expertise than other industries, which also can translate to recruitment costs, as companies compete for a skilled workforce. Additionally, recruiting costs, such as advertising job openings, candidate screening, and travel expenses, can add up quickly.
While precise estimations are difficult to set, taking into account all the variables, the average cost of hiring a manufacturing employee can range from $4,000 to $8,000 or even more, depending on the position, the job market in the areas, and the level of experience required. To secure operational efficiency, companies need to consider solutions for cost optimizations.
Minimizing hiring costs
To minimize hiring costs, manufacturing companies may choose to work with staffing agencies or use online job boards to find qualified candidates. Outsourcing recruitment can be an effective way to reduce the time and resources required to hire new employees while ensuring that only the most qualified candidates are considered.
Once new employees are chosen, presented with an offer that they accept, and start their new job, companies are faced with another challenge. The average cost of onboarding a new employee can reach astronomical amounts and needs to be taken into consideration and tackled accordingly.
Onboarding costs include:
Hardware and other physical equipment
Software, VPN access, etc.
Time investment from involved departments (IT, HR, managers)
Time investment of training staff
Creation of training curriculum and materials
Others, depending on the company’s requirements
Reducing employee onboarding costs
What can manufacturing enterprises do to decrease the cost of hiring a new employee? In times of Industry 4.0 and the unfolding digital transformation, the answer is fairly simple: leverage digital technologies. Developing efficient and effective training patterns on its own is not enough to execute successful and cost-efficient onboarding.
By utilizing digital platforms, companies can reduce the need for on-site training sessions, saving both time and money. Another way to reduce onboarding costs using digital technologies is by creating a self-paced learning program. This approach allows new hires to learn at their own pace, reducing the need for costly on-site training sessions. Self-paced learning can also help new employees retain information better, as they can revisit materials as needed, improving their knowledge and skills over time.
Enterprises can also use digital technologies to provide virtual or augmented reality training. Extended reality training can simulate real-world scenarios, allowing new hires to practice their skills in a safe and controlled environment. This approach can significantly reduce the need for on-site training, as new employees can learn and practice their skills remotely. AR and VR training can also be used to simulate high-risk scenarios, such as working with heavy machinery, improving safety, and reducing the risk of accidents. Additionally, turning to digital solutions reduces also trainer involvement in the process, enabling further reduction of training costs. With Nsflow, you can unburden your instructions and enable new hires to learn while guided by instructions displayed right before their eyes.
Solutions like Nsflow grant industrial companies with a user-friendly, intuitive tool to create training content in the form of digital workflows. Not only can new hires learn hands-on and receive feedback, but their progress is monitored for spot-on analysis and quick response to occurring training needs.
On top of that, using digital technologies to create standardized training programs can reduce the cost of developing new training materials for each new employee. By standardizing training materials, employers can save time and resources while still providing high-quality training to new hires. Additionally, standardized training materials can be used across multiple locations, improving consistency and reducing the need for costly customized training programs. Digital training content is easy to update and supplement anytime new regulations come into force, requirements change, and new equipment arrives at the plant. No need to print and dispatch paper copies to every team member allows for time and cost savings.
Artificial intelligence can help reduce onboarding costs in manufacturing by automating certain aspects of the onboarding process. For example, AI-powered chatbots can provide new employees with immediate support and guidance, reducing the need for on-site training and support. Chatbots can answer common questions and provide real-time feedback, improving the efficiency of the onboarding process and reducing the need for repeated training sessions.
AI can also be used to improve the accuracy and effectiveness of training programs. By analyzing data on employee performance and behavior, AI algorithms can identify areas where additional training is needed, providing targeted training and support to individual employees.
This approach can significantly reduce the cost of developing and delivering training programs, as employers can focus their resources on the areas where they are most needed. Additionally, AI-powered training programs can be tailored to the specific needs and learning styles of individual employees, improving engagement and knowledge retention, and reducing the need for repeated training sessions.
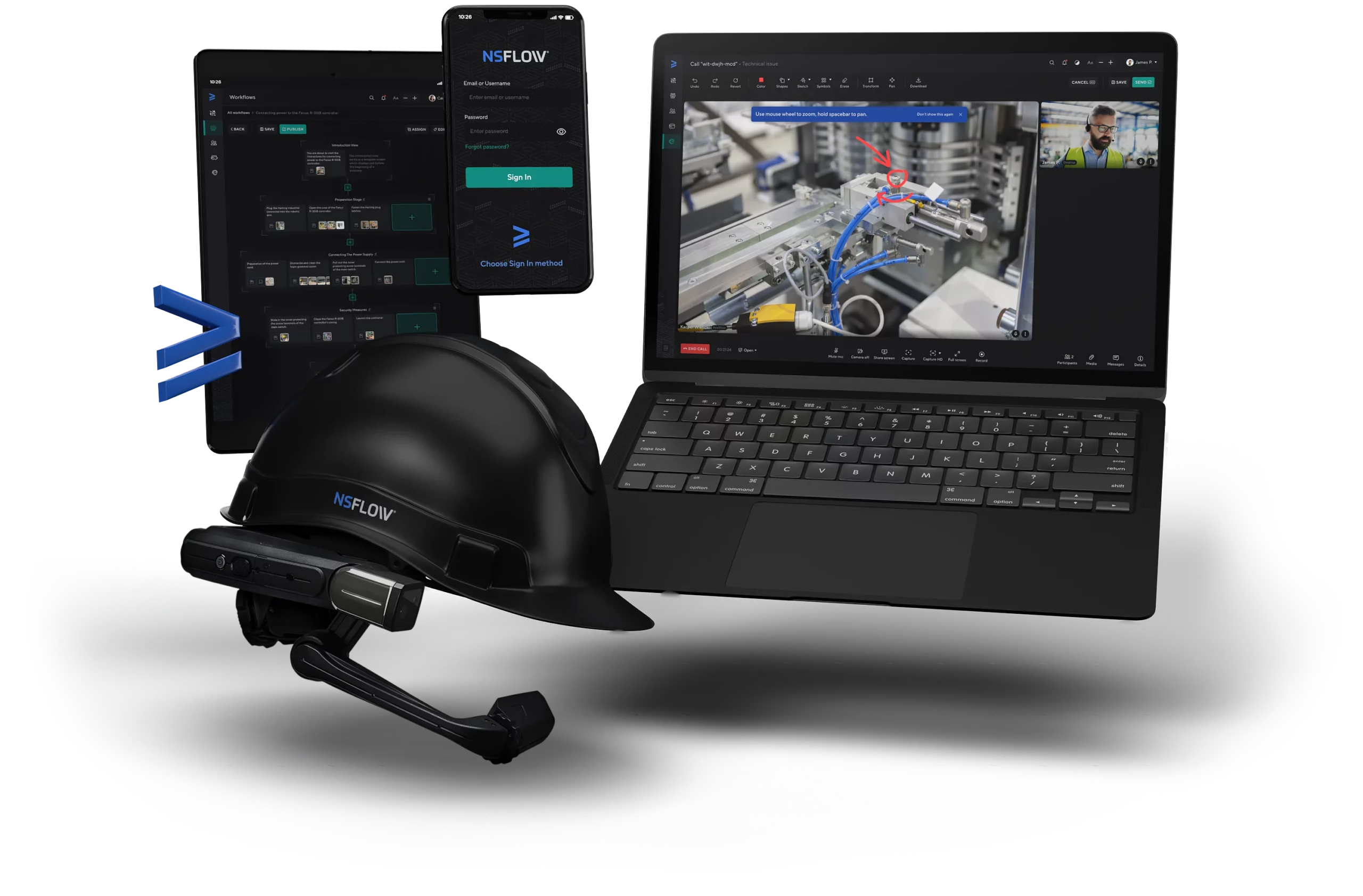
presentation to try
Nsflow in action
The takeaway
With the increasing costs of recruiting and training new employees, reducing onboarding costs is critical to the long-term success of any manufacturing company, allowing enterprises to stay competitive in a constantly evolving industry while still providing high-quality products and services.. By reducing onboarding costs, companies can allocate their resources more efficiently, allowing them to invest in other critical areas such as research and development or marketing. Additionally, reducing onboarding costs can help companies attract and retain top talent by offering more competitive salaries and benefits packages.
The ability to streamline the onboarding process is crucial for reducing onboarding costs. By standardizing training and development programs, employers can ensure that all new hires receive the same level of training and support, which can improve the quality and consistency of their work. Additionally, by reducing the amount of time and resources required for onboarding, companies can get new employees up to speed more quickly, improving productivity and efficiency across the organization.
In the dynamic environment and the ever-changing market, it’s hard to explicitly answer emerging questions on how much does it cost to onboard an employee, we’re sure that there’s always room for improvement. Learn how can Nsflow help your enterprise reduce costs across your operations – from onboarding to OHS and fire safety training to executing processes seamlessly and efficiently.
Got questions? We’re here to help – let us know!