The manufacturing industry faces a constant challenge of integrating new employees efficiently, given the technical expertise and safety standards required. Onboarding in this sector is not just about familiarizing newcomers with their jobs, but also training them in various processes, technologies, and safety protocols, all of which take time and resources. Reducing onboarding costs without compromising on the quality of training is therefore a significant concern.
In a globalized world where competitive advantage can be achieved by efficient resource management, onboarding cost in the manufacturing sector becomes an essential factor to manage. A streamlined and efficient employee integration process can not only reduce costs but also enhance productivity and retention rates, resulting in a healthier bottom line for the company.
Understanding onboarding costs in manufacturing
Onboarding a new employee in manufacturing involves various costs. From advertising job openings and screening potential candidates to extensive training and provision of essential equipment, the expenses can add up quickly. Understanding these cost components is crucial in identifying areas where efficiency can be improved.
Manufacturing, unlike many other sectors, requires a unique set of skills. The high demand and competition for skilled workers result in an increased cost to hire new employees. Also, the highly regulated nature of this industry requires continuous training and certifications, which further escalates onboarding costs. Therefore, improving the efficiency of the hiring process and effective training become paramount to controlling expenses.
Challenges in employee onboarding in manufacturing
The manufacturing industry poses unique challenges in employee onboarding. The complexity and diversity of operations, the need for safety training, the requirement for ongoing technical training due to fast-evolving technologies, all make onboarding in manufacturing a complex and resource-intensive process. Moreover, the initial productivity loss as new hires get up to speed contributes significantly to the cost of a new hire.
The concept of ‘onboarding time’ is particularly important in manufacturing. This is the period between a new hire’s first day and the time they become fully productive. The length of the onboarding time can significantly impact productivity and costs, making it a key metric for companies aiming to reduce their onboarding expenses.
Strategies for efficient employee integration
Efficient employee integration goes beyond the induction process. It involves making new hires understand the company culture, equipping them with the necessary tools and skills, and ensuring they feel welcomed and valued. Using a structured onboarding program, assigning mentors, and leveraging feedback can help streamline the process and reduce onboarding time and costs.
The adoption of technology can also play a pivotal role in efficient integration. From digital onboarding portals to online training modules and virtual reality platforms, various tools can aid in reducing costs. For instance, an automated onboarding software can help manage paperwork efficiently, reducing the administrative load and accelerating the onboarding process.
The role of training in cost reduction
Training is a crucial part of the onboarding process, especially in the manufacturing industry. Well-designed training programs not only equip new hires with necessary skills and knowledge but also foster engagement and reduce turnover, indirectly cutting costs. By developing modular, self-paced online training resources, companies can reduce the costs associated with in-person training and allow employees to learn at their convenience.
Many manufacturing companies have successfully managed to reduce their onboarding costs through effective training programs. These companies use a mix of hands-on training, classroom instruction, online modules, and on-the-job coaching to create a holistic learning experience. By constantly evaluating and improving these training programs based on feedback and performance data, they ensure the effectiveness and efficiency of their training processes.
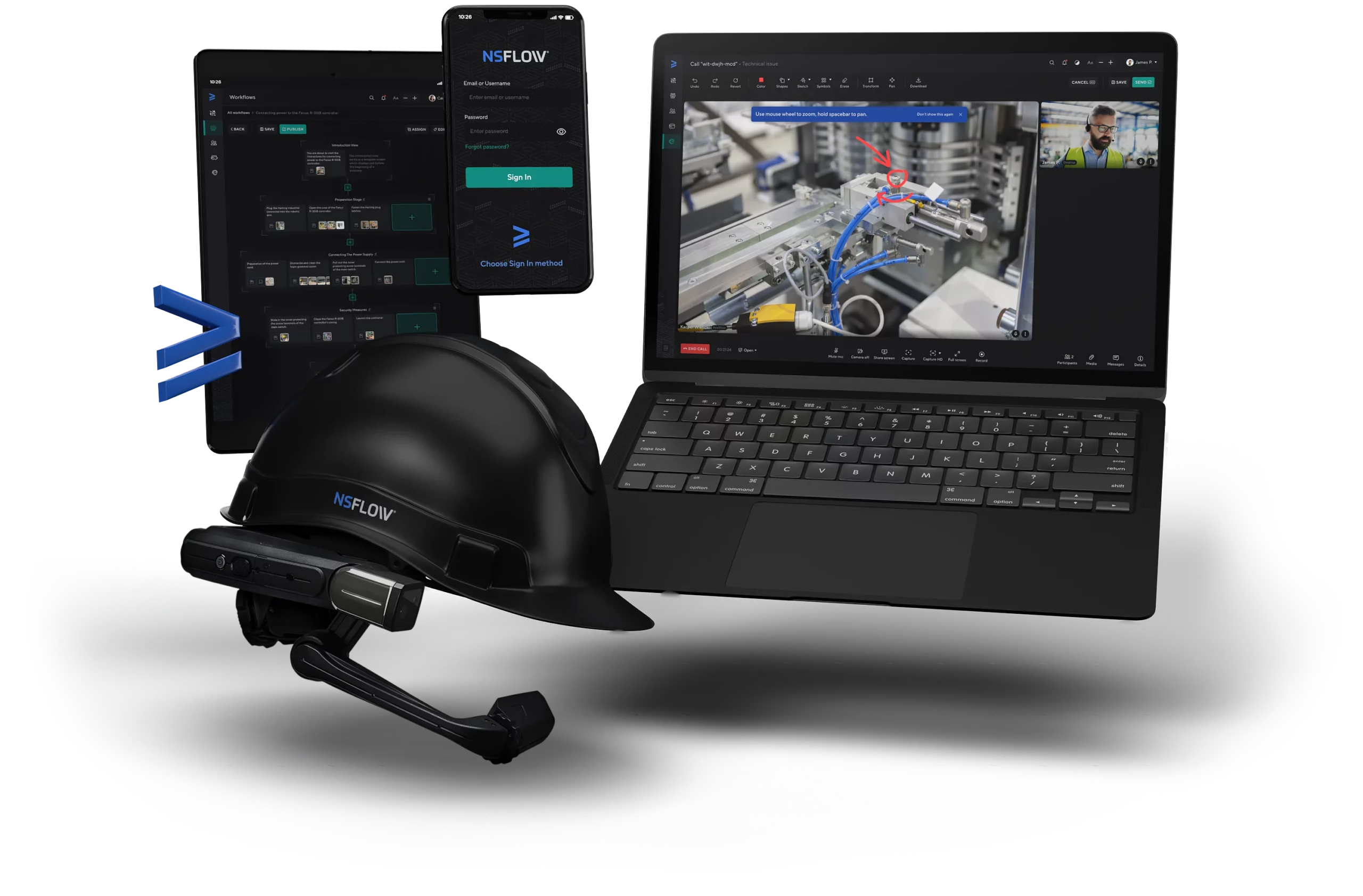
presentation to try
Nsflow in action
Technology and its role in onboarding
The use of technology in the onboarding process can prove to be a game-changer. For example, mobile applications for onboarding help leveraging AI for efficient onboarding
Artificial Intelligence (AI) can bring a transformational shift in the onboarding process. AI-powered chatbots, for instance, can answer new hires’ common queries, thereby reducing the time HR personnel spend on resolving these issues. Additionally, machine learning algorithms can tailor training programs to individual learning patterns, making the process more effective.
Predictive analytics, another branch of AI, can help identify patterns and trends from past onboarding programs, highlighting areas that need improvement. This data-driven approach can significantly enhance the effectiveness of the onboarding process and lead to substantial cost savings in the long run.
Future trends in employee onboarding
To wrap up, the article could explore future trends in employee onboarding. This might include further advancements in AI and technology, changes in onboarding processes due to remote work, and the increasing emphasis on employee experience during onboarding. As the landscape of work continues to evolve, staying ahead of these trends can ensure a company maintains efficient, cost-effective onboarding processes.
Remember, reducing onboarding costs doesn’t mean compromising on quality. Instead, it’s about finding smarter, more efficient ways to welcome new employees into your organization and equip them with the skills and knowledge they need to excel in their roles. The strategies and technologies outlined in this article provide a roadmap to achieving just that.
The takeaway
Efficient employee integration in manufacturing is crucial, not just from a productivity standpoint but also from a cost perspective. By leveraging technology and adopting innovative strategies, manufacturing companies can significantly reduce their onboarding costs while still providing new hires with a comprehensive and engaging onboarding experience.
As industries continue to evolve, companies that adapt and optimize their onboarding process will gain a competitive edge. The focus should not only be on reducing the cost of onboarding new employees but also on creating a positive first impression and setting new hires up for success. The latter inevitably leads to a more engaged and loyal workforce, which in itself is a cost-saving measure in the long term.