Over the past 3-4 years, the industrial maintenance and inspection sector has experienced a rapid digital transformation, a trend further accelerated by the global pandemic. A once niche practice, remote inspections have now become more prevalent. The latest statistics project that the global digital control market will surge to USD 39.2 billion by 2030, underscoring remote control technology’s significant impact and growing importance.
The increasing popularity of remote inspections naturally leads to questions about their benefits to the industry. In this article, we delve into the advantages of remote inspections, providing insights on what preparations to make, how to overcome technical limitations, and how to conduct a remote inspection step-by-step.
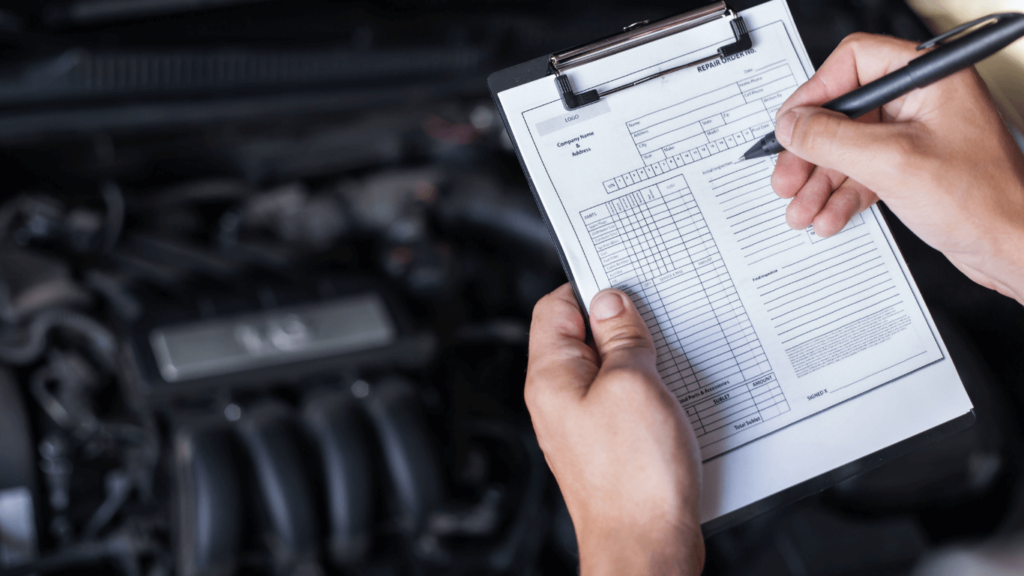
The Importance Quality Control And Maintenance Strategy In Manufacturing
For multiple reasons, quality control and proactive maintenance are essential pillars of manufacturing success. They enable companies to deliver high-quality products consistently, minimize maintenance costs, facilitate compliance with regulations and standards, optimize supply chain performance, and enhance customer satisfaction, leading to increased orders.
Inspection is an important element of the complex quality control process in industry. However, to maintain good performance at the lowest possible costs, more and more companies are turning to remote inspections, using the benefits of modern technologies such as MR, VR, AR, artificial intelligence, or satellite technology.
For this reason, investing in quality control and maintenance strategies is essential for manufacturers who want to thrive and increase profits in today’s competitive industrial environment.
A Remote Inspection In Practice – How It Works?
Simply put, a remote inspection is a procedure that enables the monitoring and control of the condition and operation of machines, facilities, or processes from a distance. Inspectors do not have to be physically present at the site because they use technology and remote communication equipment. Devices like smart glasses and cameras allow them to collect visual data, measurements, and other inspection information through communication with the on-site workers. Data collected in this way enables professionals to observe, analyze, and evaluate the condition, performance, and compliance of assets or facilities without the need to travel and without direct physical access.
AR technology typically uses cameras and sensors and can include images, videos, depth information, and other relevant environmental data. On-site workers and technicians transmit this information to experts working remotely and evaluate the captured data in real time, providing necessary feedback to on-site workers.
Challenges And Constraints During Remote Inspections
One concern that machinery service professionals may have about remote inspections is the potential lack of detail in the images compared to on-site inspections. However, this fear is unfounded, as advanced imaging technologies address these concerns.
For example, implementing AR solutions allows for the visualization of equipment and interaction with it. Platforms like Nsflow facilitate real-time communication and collaboration between inspectors and subject-matter experts. With features such as live video, screen sharing, and instant messaging, inspectors can receive guidance and feedback from remote experts, enhancing visibility during inspections.
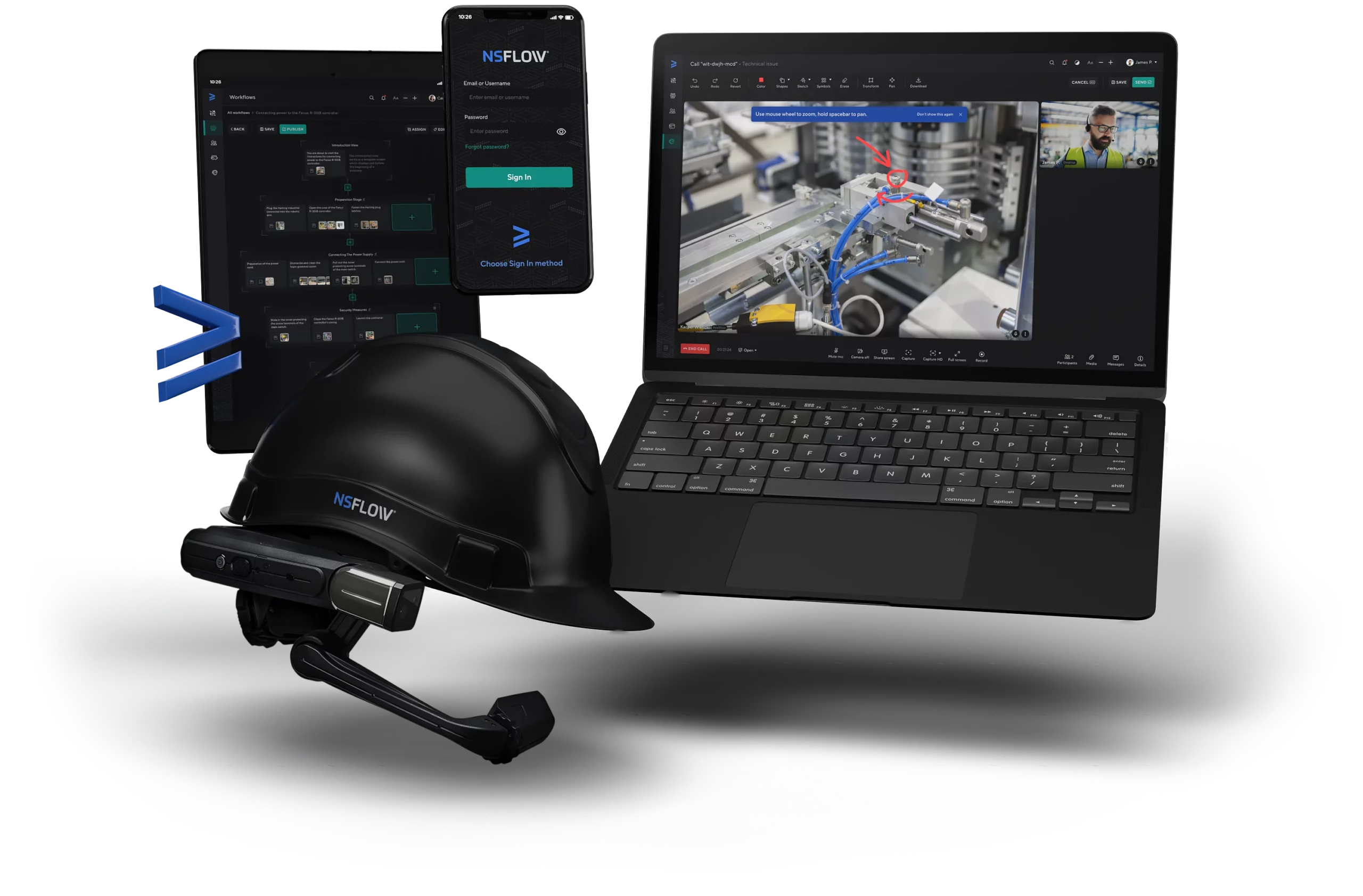
presentation to try
Nsflow in action
While introducing remote inspections in challenging industrial environments, such as offshore or underground works, may raise concerns, these can be effectively addressed. By preparing the ecosystem for new systems and combining remote and on-site inspections, we can overcome technological limitations and data access issues. Solutions like offline data storage, satellite communications, and mobile inspection units can conquer connectivity limitations in remote areas.
Additionally, companies can implement end-to-end industrial AR training with digital workflow schemes and technical remote support to enable inspection staff to solve problems effectively. Establishing explicit access permissions and security protocols and working with local partners facilitates remote access to equipment and facilities.
Why Should Maintenance Employ Remote Inspections?
We would like to list the following main benefits of remote inspection that maintenance managers and machine maintainers should take into account:
- financial savings by reducing travel, accommodation, and inspection site visit expenses,
- remote inspections facilitate better data collection and analysis, leading to optimized maintenance schedules and predictive maintenance strategies
- improved efficiency thanks to the ability to perform more frequent (because cheaper) inspections, which leads to faster identification of problems and their speedier resolution.
- remote inspections increase safety by reducing the risks of sending personnel into hazardous environments.
- availability of equipment and facilities located in remote or difficult-to-access areas.
- real-time monitoring capabilities allow for proactive maintenance, minimizing downtime and maximizing productivity.
- more sustainable manufacturing and maintenance practices by lowering carbon emissions and providing safer working conditions.
How To Prepare A Remote Inspection?
Planning a remote inspection requires careful consideration of various factors to ensure its success. From technological analysis to training protocols and security measures, each preparation stage is crucial in optimizing the effectiveness and efficiency of remote inspections in industrial settings. Some of the most essential stages of this process include:
Technological Analysis
Planning a remote inspection requires careful consideration of various factors to ensure its success. Firstly, a technological analysis should be carried out to determine whether the current systems can be interconnected or replaced by new solutions. If the analysis yields positive results, companies and institutions must choose equipment and technology to ensure optimal results throughout the project.
Developing Standard Operating Procedures (SOPs)
Preparing for remote company inspections also involves developing Standard Operating Procedures (SOPs). This step entails establishing transparent and standardized procedures for conducting remote inspections, covering aspects such as equipment setup, data collection, communication protocols, and reporting requirements. SOPs help ensure consistency, efficiency, and compliance with quality standards.
Training and Education
Another crucial stage in preparation is providing training and education. Companies should offer comprehensive training and education programs to employees involved in remote inspections, including inspectors, maintenance personnel, and relevant stakeholders. It’s essential to ensure that staff are proficient in operating remote inspection tools, interpreting data, and adhering to safety protocols.
Choosing Technologies for a Remote Inspection
Among the technologies available, augmented reality (AR) platforms are valuable tools for remote inspections. Then, one employee is on-site, and the other can conduct the inspection remotely. What is essential is that an employee may be on-site and guided by the remote inspector, being his “hands and eyes.”
Utilizing AR technology, inspectors can perform their duties safely and efficiently within a controlled environment, significantly reducing the need for employees to travel to inspection sites. Industrial-grade AR glasses provide inspectors with immersive visualizations and real-time data overlays, enhancing their inspection capabilities and resulting in significant cost savings, including travel expenses.
Artificial intelligence also expands the possibilities and improves the quality of remote inspection. AI primarily automates some processes and allows automatic assessment of the condition of elements based on vision or sensor data, reducing the need for “manual” work and reducing costs. AI capabilities enable proactive maintenance strategies, ultimately increasing equipment reliability and minimizing downtime.
Security Measures
Safety is paramount in remote inspections, so preparation should involve implementing robust security measures to protect sensitive data and ensure compliance with data privacy regulations. This may entail deploying encryption protocols, access controls, and secure communication channels to safeguard information transmitted during remote inspections. Many companies prefer not to store their data in the cloud, and platforms like Nsflow offer on-premises or hybrid solutions, such as the Nsflow box, to address these concerns.
How To Conduct A Remote Inspection?
We will explain remote inspection using the example of Nsflow, a platform offering a unique digital workflow training module. By following these steps and leveraging the capabilities of Nsflow’s digital workflow module, companies can conduct efficient and hands-on remote inspections, optimizing maintenance and quality control processes for enhanced productivity and reliability.
Creating a Digital Inspection Procedure
The first step in conducting a remote inspection with Nsflow is to create a new digital inspection procedure within the platform. This procedure is given a descriptive name, such as “periodic inspection,” and is designed to encompass all necessary inspection tasks.

Utilizing the Workflow Creator
Once the inspection procedure is established, the workflow creator within Nsflow is accessed to develop it further. This intuitive interface allows users to add elements to the procedure, such as checklists, voice notes, text fields for comments, numeric fields for sensor data, and multimedia content like photos and videos.
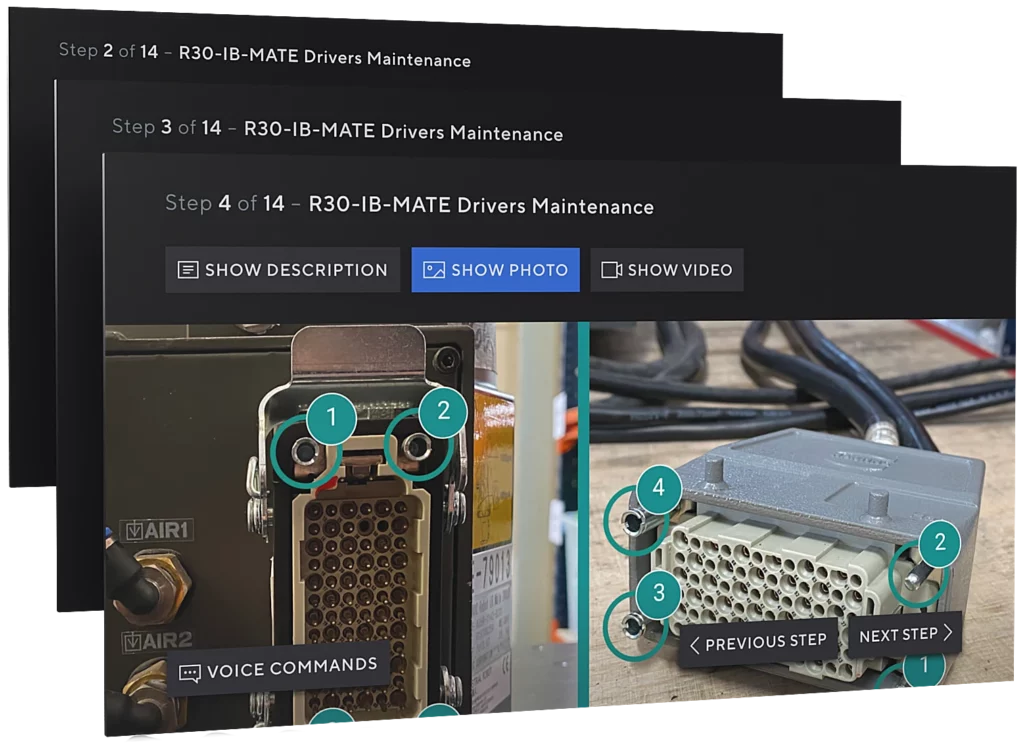
Generating Reports and Integrating with Superior Systems
After completing the inspection, Nsflow’s system can automatically generate a comprehensive report detailing the findings. This report can be easily accessed within the platform and shared with relevant stakeholders. Additionally, Nsflow seamlessly integrates with superior systems such as SAP, enabling the transfer of necessary data for further analysis and action.
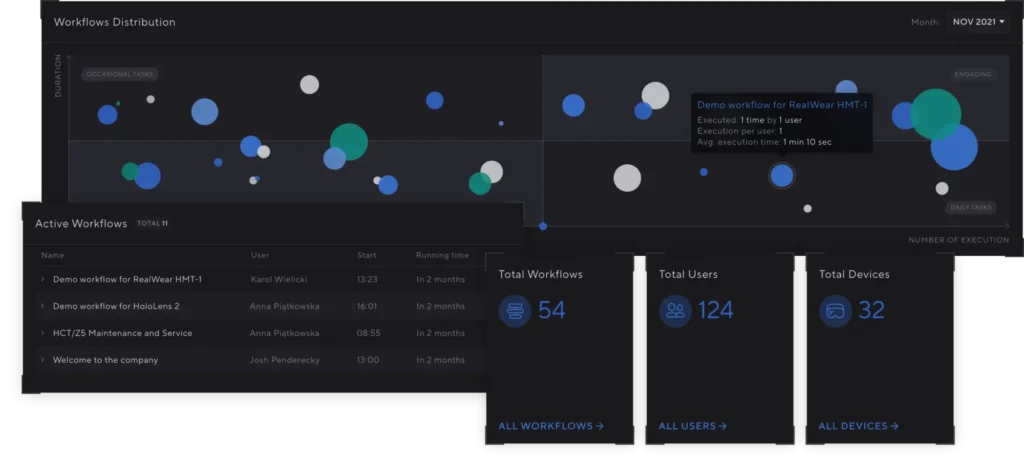
Crafting Instructions with the Creator Tool
The Creator tool within Nsflow empowers users to craft detailed instructions for inspection procedures. By defining each step and incorporating multimedia content through drag-and-drop functionality, instructions become clear and easy to follow. Multimedia elements, including photos, videos, and audio recordings, enhance comprehension and facilitate remote inspections.
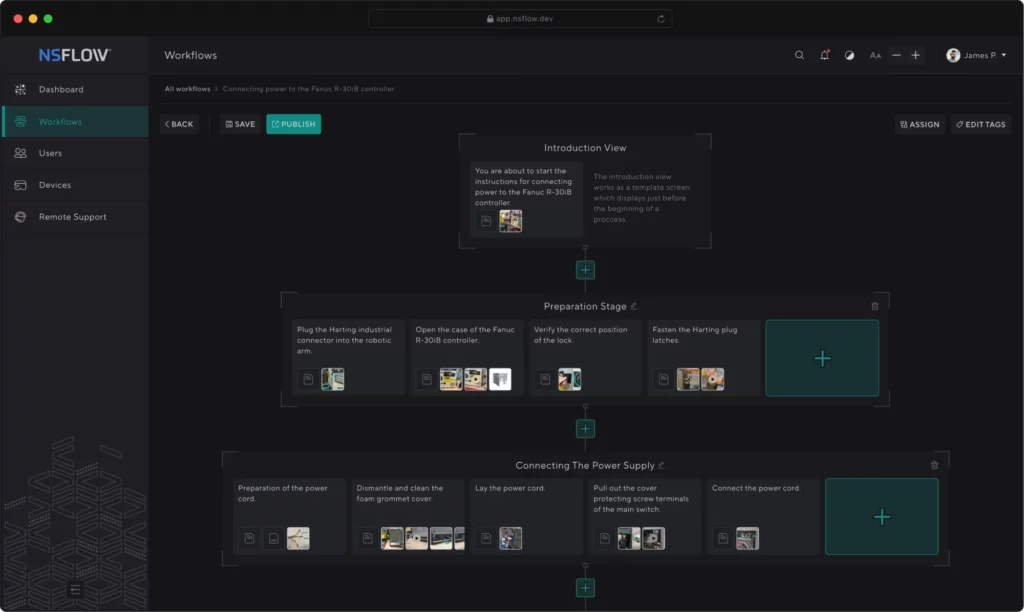
Leveraging AR Capabilities for Enhanced Visualization
Nsflow’s digital workflow module offers advanced augmented reality (AR) capabilities. It allows users to incorporate static or animated 3D models displayed as realistic holograms, enhancing visualization and providing a deeper understanding of inspection tasks.
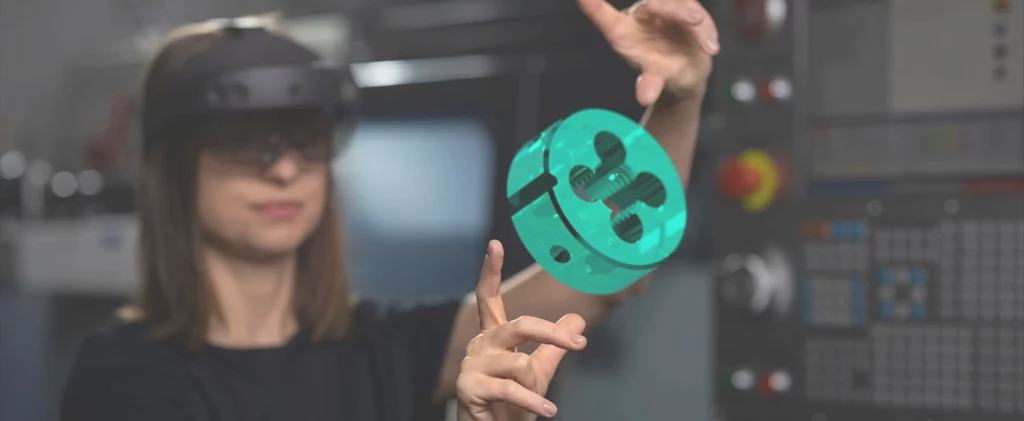
Conducting Remote Inspections On-Site
Once instructions are prepared, personnel on-site utilize the Nsflow application on their smartphones or tablets to access the digital inspection procedure. Here, inspectors have two options: they can either follow the workflow on their own or participate in a remote inspection session under the supervision of a remote instructor.
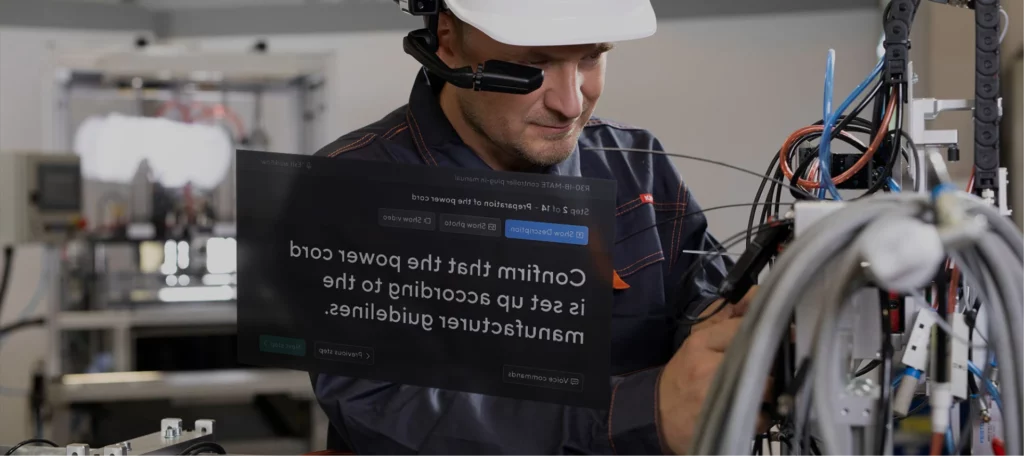
How To Optimize A Remote Inspection?
To ensure smooth and productive remote inspections, it’s worth following these tips:
- Quality connection – People on both sides of the screen must ensure the good quality of the Internet connection in their units, and the camera on the phone used by the employee “showing” the remote inspector around the production plant should offer the highest image resolution possible.
- Technology testing – Before choosing a remote inspection software provider, testing and learning it is good. Nsflow offers a free demo of its platform, which allows you to experience the capabilities and operation of the platform in the conditions in which it is intended to work daily.
- Backup plans – If you are unsure your connection will be uninterrupted, prepare emergency measures and backup communication channels. They will come in handy in case of technology failure or connectivity problems.
- Data security – remember that not all remote inspection platforms work only in the cloud. Companies can choose an on-premises solution, where the entire platform is installed on external computers and access to data is only possible from inside the organization. Nsflow box, in turn, is a solution that combines the best features of on-premises software and the cloud version.
- Feedback and Improvements – After each remote inspection, participants should receive feedback to highlight areas for improvement and refine the process for future inspections.
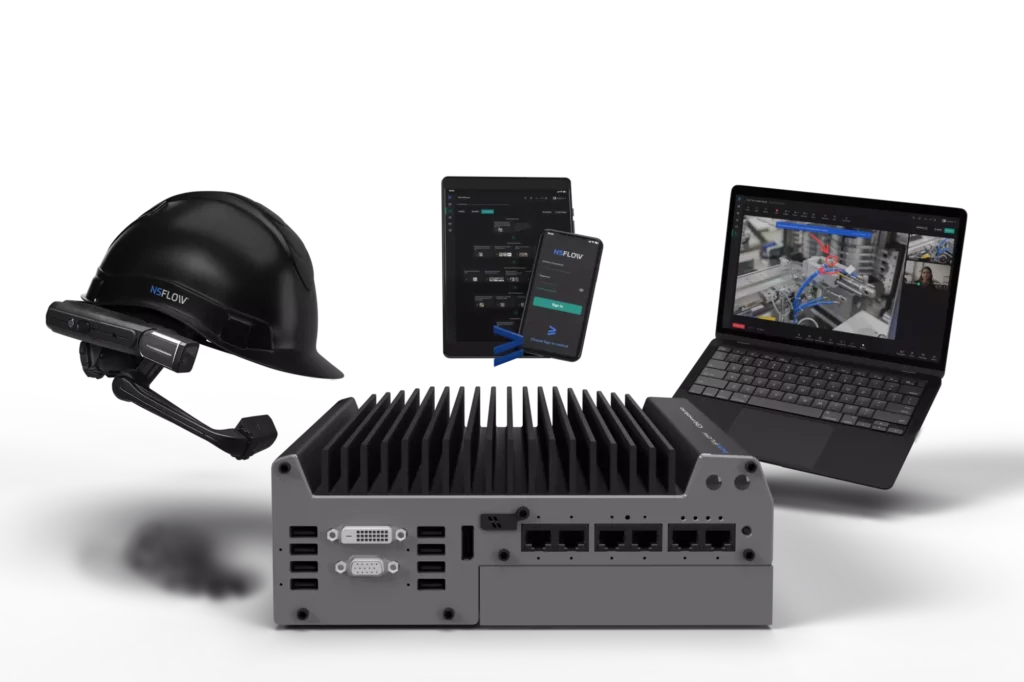
In conclusion, conducting correct remote inspections in the industry involves meticulous planning, leveraging appropriate technology, and fostering effective stakeholder communication. Companies can maintain operational integrity, enhance safety standards, and optimize machine performance from a distance by ensuring thorough preparation, utilizing appropriate inspection tools, and adhering to established protocols.