In Plant Engeenering 2020 Survey industrial maintenance specialists indicate the age of machines (34%) and mechanical failure (20%) as direct reasons to take machines out of use. This group also pointed out operational errors (cited by 11% of surveyed maintenance professionals), lack of time for maintenance (9%), and poor equipment design (8%) as key factors that negatively affect maintenance performance.
To keep your factory machinery running smoothly and lasting longer, all industry managers should optimize a maintenance workflow. Such improvements will also extend the life of other equipment used daily in production plants and improve the operation of the entire factory infrastructure. All this is aimed at shortening machine downtime, which generates costs related to their temporary exclusion from use. So the rule is simple – if you can’t eliminate something, improve it. And in this guide, you will learn how to optimize your maintenance workflow in 4 steps.
Best Technologies To Optimize Workflow In The Maintenance Process
Maintenance workflow is how a company performs maintenance. It is the process of planning, carrying out, and reporting all maintenance procedures. Maintenance workflow may be ineffective or optimal. Of course, the latter is important to all companies that employ advanced technologies, among which the key ones are predictive maintenance (PdM), the Internet of Things (IoT), and augmented reality (AR). How exactly do they work, and how do they help optimize maintenance workflow in the industry?
Predictive Maintenance (PdM) in the maintenance process
Predictive maintenance uses data analytics and machine learning algorithms to predict equipment failures before they occur, enabling proactive maintenance interventions. By analyzing historical data patterns and current operating parameters, PdM helps to optimize workflow in the maintenance process through proactive interventions, thereby preventing costly downtime and increasing overall equipment reliability. This is confirmed by the data. According to the Industrial Maintenance 2020 report, PdM is most often indicated as an effective method of minimizing downtime, which was indicated by almost 80% of respondents.
Source: Industrial Maintenance 2020. Status, Trends And Forecasts Report
Integration with the Internet of Things (IoT) to optimize workflow
Internet of Things technology connects machines and equipment to networks to collect real-time data on performance, usage, and environmental conditions. This connectivity enables real-time data collection on various parameters, such as performance, usage patterns, and environmental conditions. IoT-enabled systems provide invaluable insight into equipment health, facilitating predictive maintenance strategies, and optimizing maintenance schedules for maximum efficiency.
Implementation of Augmented Reality (AR) in the maintenance process
Augmented reality technology provides technicians with interactive instructions, visualizations, and remote assistance during maintenance tasks. This immersive technology increases efficiency and accuracy, enabling technicians to diagnose problems effectively and complete tasks more accurately, ultimately reducing downtime and increasing productivity.
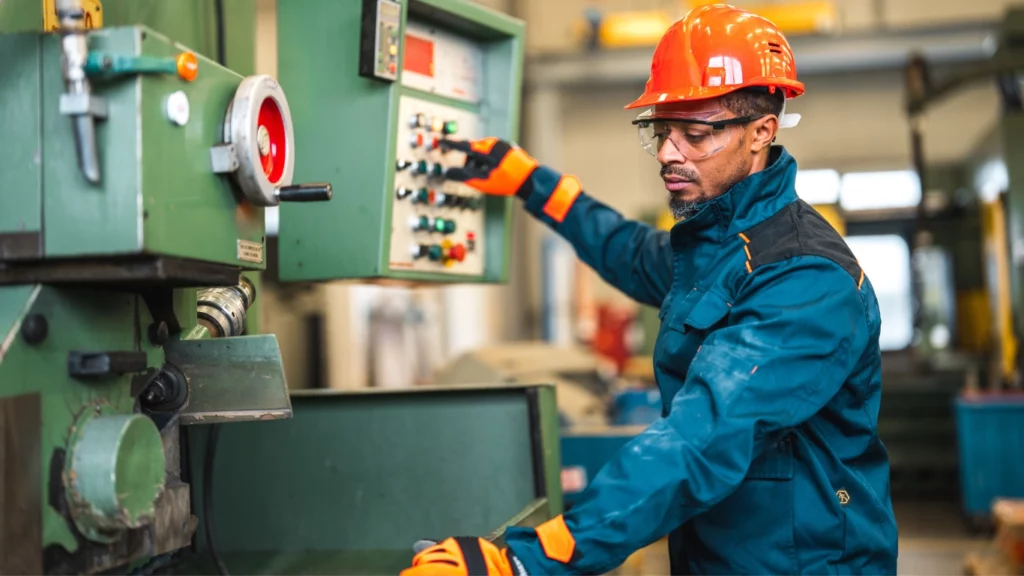
How To Optimize Workflow In Maintenance In 4 Steps
It is best to organize your optimization strategy and consider the sequence of steps. If companies want to optimize workflow in the maintenance process, they should consider, among other things, industrial training for maintenance technicians, assessment of current risks, implementation of appropriate technologies (predictive maintenance, IoT, AR, VR, AI), and ongoing monitoring of machine condition. Below, you will find a quick guide on how to optimize workflow in maintenance in 4 steps:
Step 1: Assess Current Practices
First, maintenance managers should assess existing procedures and systems to identify inefficiencies, bottlenecks, and areas for improvement. These include maintenance schedules, work order management, resource allocation, and communication channels. They need to find factors contributing to downtime or reduced productivity. Assessing current risks to optimize workflow allows professionals to identify areas requiring attention or restructuring.
Optimize Current Practices Assessment with Nsflow Digital Workflow Software
Nsflow’s digital workflows software offers a significant advantage in assessing current maintenance practices by providing a centralized data collection, analysis, and collaboration platform. Maintenance managers can leverage the platform’s features to:
- Repository Of Tasks And Procedures—Use the Nsflow platform to create a centralized repository of maintenance tasks, procedures, and historical data. This will enable easy access to detailed instructions for current and future employees and streamline the assessment process by providing a clear overview of existing practices.
- Interactive Reporting And Analytics – Nsflow’s software generates interactive reports and analytics dashboards, facilitating insights into maintenance performance metrics. Maintenance managers can analyze work orders, downtime, and resource utilization data to identify patterns and improvement areas.
- Collaborative Workspace – On Nsflow digital workflow software, maintenance teams can collaborate in real-time, sharing observations, insights, and suggestions for improvement.
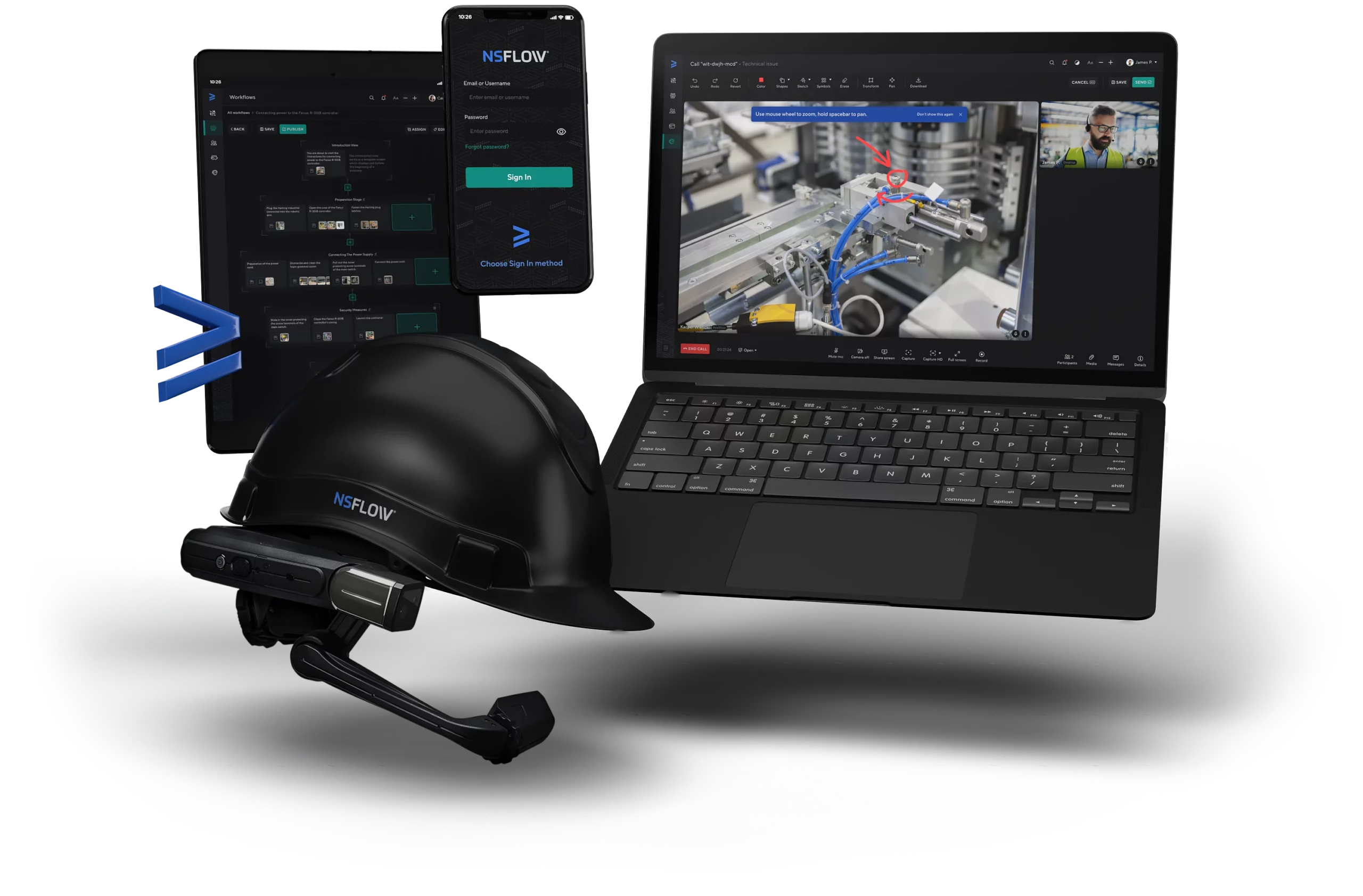
presentation to try
Nsflow in action
Step 2: Implement Predictive Maintenance
The next step to optimize workflow is implementing a predictive maintenance strategy. By continuously monitoring equipment health, industrial companies can anticipate potential problems before they become costly failures. This helps minimize downtime and extend the life of your equipment. Additionally, it focuses maintenance efforts where they are needed most. Predictive maintenance requires the installation of IoT hardware along with AI-based analytics software. This will inform maintenance managers about equipment performance, usage patterns and environmental conditions.
Improving Predictive Maintenance with Nsflow Digital Workflow Software
Nsflow’s digital workflow software provides a comprehensive data collection, analysis, and decision-making platform. In this way, companies can obtain valuable data on equipment and conduct remote inspections, remote support sessions, and industrial AR training. Here’s how:
- Integration of IoT Devices – The Nsflow platform seamlessly integrates with IoT devices, including augmented reality (industry-grade AR glasses, cameras, sensors, actuators, helmets, tablets).
- Advanced Analytics Capabilities – The Nsflow platform enables large-volume analytics that maintenance managers can use for predictive analytics modeling. This allows you to sequence and schedule maintenance activities.
- Automated Work Order Generation – Nsflow digital workflow software can automatically generate work orders based on predictive maintenance triggers, streamlining the planning and delegation of maintenance tasks. This allows maintenance workers to work faster, minimizing the risk of unexpected machine downtime.
Step 3: Conduct Maintenance Training
Optimizing maintenance workflows must also include high-quality industrial training for maintenance technicians, onboarding new employees, and regular hands-on training. At this stage, organizations should invest in AR training to familiarize them with the necessary skills and knowledge to perform maintenance tasks correctly. Thanks to appropriate software and augmented reality technology, such training can now be conducted remotely.
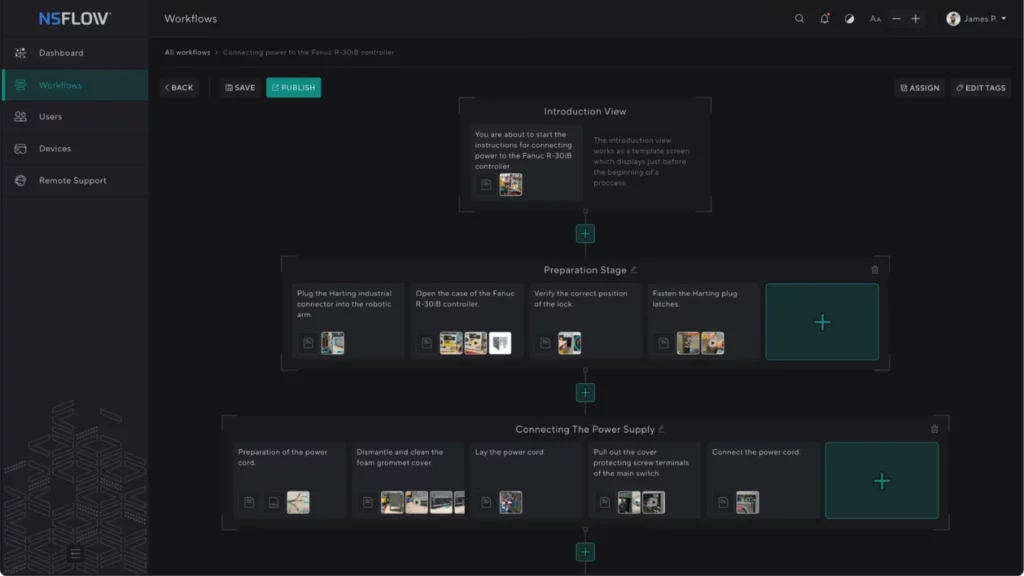
Maintenance Training with Nsflow
- Interactive Training Modules – With these, instructors can create interactive training modules and simulations that recreate real-world maintenance scenarios. Technicians can use these modules via AR devices and learn in a safe, simulated environment before entering the field.
- On-Demand Training Resources – This feature of Nsflow offers on-demand access to training resources, including how-to videos, interactive tutorials, and knowledge bases. Technicians can use the materials whenever they want, consolidating and standardizing their knowledge and refreshing their skills.
- Assessment and Certification – The platform supports assessment and certification features, allowing companies to track and evaluate technicians’ learning progress.
Step 4: Monitor And Improve
The final step in helping to optimize workflow in the maintenance process should be establishing mechanisms to monitor and improve your systems continuously. This includes establishing key performance indicators (KPIs), collecting feedback from technicians, analyzing performance metrics, and identifying further optimization opportunities.
Workflow Optimization Improvement with Nsflow Digital Workflow Software
The digital workflow software from Nsflow offers a centralized platform for data analysis, collaboration, and continuous improvement, making monitoring and improving maintenance procedures easier. Here’s how to use these functions:
- Performance Analytics – Industrial companies can use advanced analytics to track key performance indicators such as maintenance downtime, asset reliability, and technician productivity. Performance dashboards will provide real-time visibility into maintenance operations, enabling organizations to identify trends and patterns that may require attention.
- Feedback Mechanisms – Because Nsflow supports feedback mechanisms (surveys, surveys, and suggestion boxes), technicians can share their experiences with the maintenance workflow. Organizations can collect and analyze this feedback to identify areas for improvement and prioritize improvement efforts accordingly.
- Process Automation – Nsflow digital workflow software helps optimize workflow in the maintenance process by automating routine maintenance tasks so that technicians can focus on more strategic activities. By streamlining repetitive processes and eliminating manual intervention, organizations can improve efficiency and reduce the risk of human error.
Optimize Workflow And Keep Your Maintenance Data Secure
Finally, it is worth adding a few words about the security of maintenance data. There are two main ways to store sensitive content and data – in the cloud or on internal company servers (on-premises storing). But, there is a third option – a Nsflow Box. It is a hybrid offering the best cloud and on-premises services, and it is easy to install on a plug-and-play basis. It can be installed in server rooms, mounted on DIN rails, or integrated into machinery, which provides manufacturing companies with independence from external cloud providers.
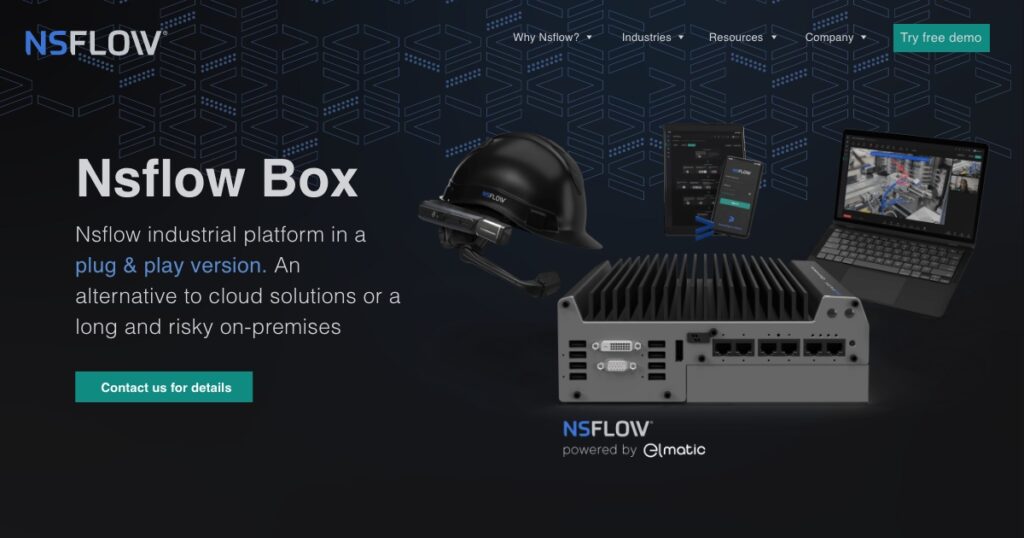
Do you want to experience the digital workflow module in your company? Sign up for a free demo and discover all its possibilities without obligations.