In the last decade, the world has seen the dynamic rise of two distinct technologies: the Internet of Things (IoT) and augmented reality (AR). While each has revolutionized several industries in its own right, few have dared to envision what combining their might could accomplish. As these technologies start to converge, we’re getting a glimpse into a new era of smart manufacturing that promises unparalleled efficiency and innovation.
IoT, with its ability to connect devices and systems, has offered industries a chance to achieve intricate, automated orchestration like never before. On the other side, AR, often misconstrued as just an entertainment tool, has been silently revolutionizing sectors like healthcare, real estate, and indeed, manufacturing. Let’s dive deep and explore the phenomenal potential of these two technologies when combined.
The promise of this integration is not just about a shift in manufacturing processes. It is about redefining how the industry functions at a fundamental level, ushering in a new paradigm that could shape the future of production for decades to come.
Understanding the fundamentals
IoT in modern manufacturing
The Internet of Things, at its core, is the interconnected nature of devices and systems, enabling them to collect and exchange data. In manufacturing, this concept transforms into a network of devices, from raw material trackers to end-product quality check systems, all communicating seamlessly.
With the adoption of IoT in manufacturing, processes have become smarter, more efficient, and remarkably adaptive. Devices across the production chain can relay information in real-time, making it possible to monitor, analyze, and optimize operations on-the-fly. The era of waiting for end-of-day or end-of-week reports to make crucial decisions is fading rapidly.
While the potential of IoT in manufacturing is vast, it’s not just about connecting devices. It’s about harnessing the power of the data they produce. Analyzing this data can yield insights into efficiency improvements, predictive maintenance, and even entirely new production methodologies.
Augmented reality: beyond gaming and entertainment
Augmented Reality is often overshadowed by its more immersive cousin, Virtual Reality. But where VR transports users to entirely different realms, AR overlays digital information on the real world, enriching our perception. In the manufacturing sector, this has profound implications.
For years, AR was mostly seen as a tool for gamers and app developers. However, the manufacturing sector has identified its potential to provide workers with real-time data, guidance, and visualization tools, all while they remain engaged with their real-world tasks. For instance, an assembler can see component details, assembly instructions, and quality checks all through AR glasses, hands-free.
But it’s not just about overlaying data. AR in manufacturing is about enhancing the worker’s capabilities. Whether it’s by providing training in a simulated environment, aiding in complex machinery repair with step-by-step visual guides, or ensuring quality control by comparing real products to their ideal digital specifications, AR is setting new standards in the industry.
The synergy of AR and IoT: a convergence of digital and physical worlds
Real-time data visualization
The real magic starts when IoT and AR converge. Picture a factory floor where a supervisor, equipped with AR glasses, looks at a machine. Instantly, thanks to IoT sensors on the machine and the augmented reality data processing capabilities of the glasses, the supervisor sees real-time performance metrics, potential issues, and even predictive maintenance alerts overlaid on their view.
This instantaneous feedback transforms the way decisions are made on the factory floor. No longer does one need to consult separate systems or wait for reports. The data is available, visualized contextually, where and when it’s needed most. Such capabilities not only streamline operations but also significantly reduce the time taken to identify and address issues.
Moreover, this real-time data visualization is not restricted to supervisors or experts. Frontline workers, maintenance crews, and even external consultants can leverage this synergy of AR and IoT to perform their tasks more efficiently, ensuring that the entire manufacturing process becomes more cohesive and agile.
Enhanced decision making
Combining the visual capabilities of AR with the data-driven insights from IoT takes decision-making in manufacturing to unprecedented levels. With augmented reality Internet of Things insights readily available, decisions become faster, more accurate, and grounded in real-time data.
Imagine a scenario where a machine starts showing signs of wear. Traditionally, this would involve a technician examining the machine, consulting manuals, maybe even seeking expert opinions. Now, with AR and IoT at play, the machine’s performance data, maintenance history, and even potential solutions can be visualized in real-time by the technician, allowing for almost instant diagnosis and action.
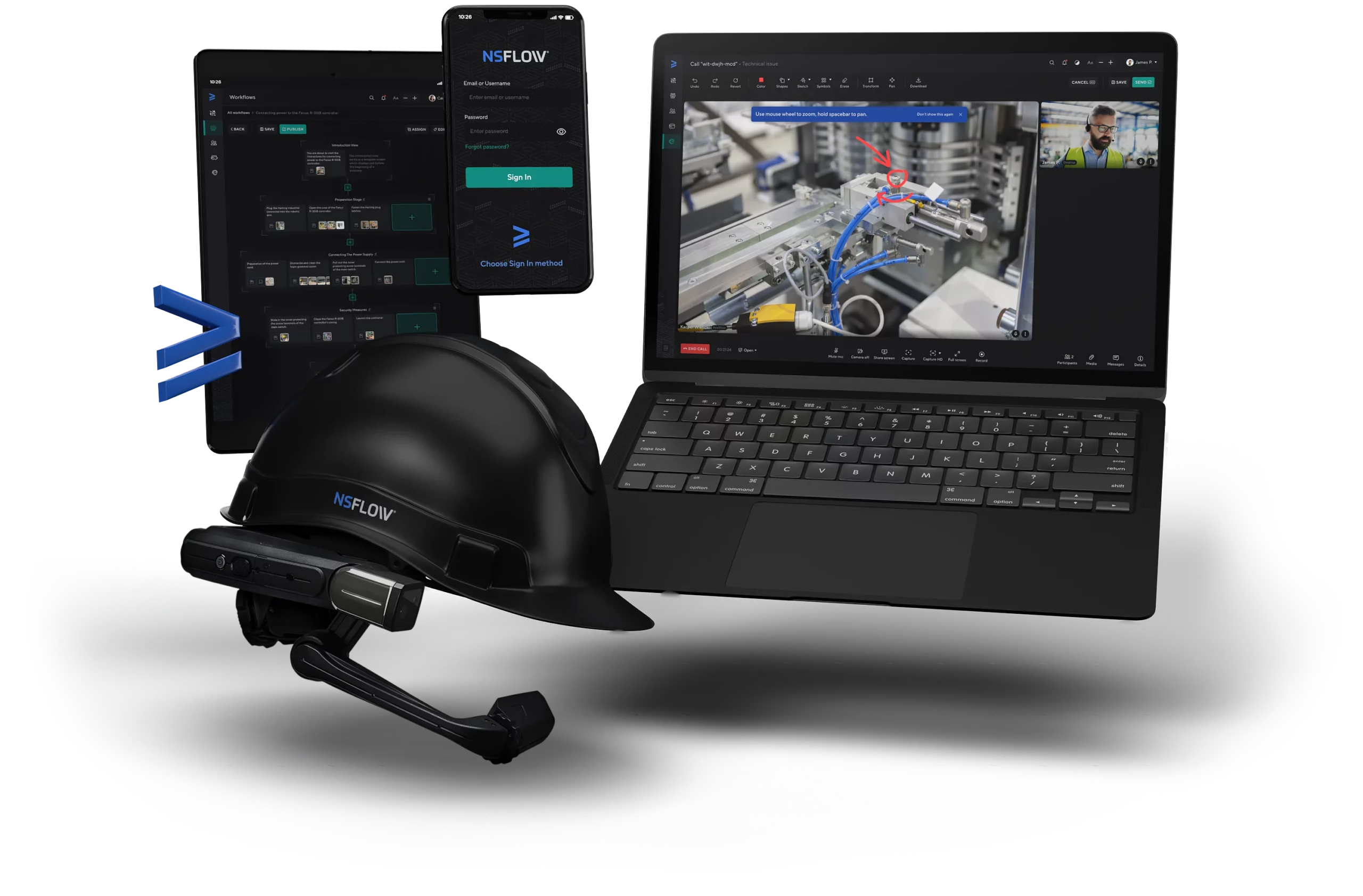
presentation to try
Nsflow in action
Remote expertise and training
The synergy of AR and IoT has a transformative impact on how training and expertise are imparted and leveraged in the manufacturing sector. AR Internet of Things capabilities make it feasible for experts to assist from anywhere in the world.
Imagine a complex machinery breakdown. Instead of waiting for an expert to travel physically to the site, a technician on the ground, using AR glasses integrated with IoT, can stream the live situation to the expert. The expert, in turn, can guide the technician through the repair process, overlaying digital instructions and diagrams onto the technician’s real-world view. This not only reduces downtime but also ensures that the best expertise is always available, irrespective of geographical constraints.
Training, too, undergoes a revolution. New hires or technicians can be trained on equipment and processes using AR simulations, allowing them to learn and make mistakes in a risk-free environment. Furthermore, with the real-time data from IoT sensors, trainers can provide immediate feedback and correction, ensuring a thorough and efficient learning process.
The future: pioneering the next wave of manufacturing innovation
Predictive maintenance and automation
One of the most significant promises of the AR and IoT integration in manufacturing is predictive maintenance. While IoT sensors can pick up on the minutest of changes in machine performance, indicating wear or potential breakdown, AR can visualize this data for operators, making them aware of looming issues even before they manifest.
Moreover, with the power of advanced analytics, the data from IoT can be used to predict when a machine is likely to fail, allowing for maintenance to be scheduled optimally, causing the least disruption. AR interfaces can then guide maintenance crews through the necessary checks and repairs, ensuring that machinery operates at peak efficiency at all times.
The integration also opens the doors to higher automation levels. With machines capable of reporting their status and performance in real-time and human operators equipped with AR tools to understand and act on this data swiftly, it becomes possible to automate more complex and nuanced tasks that previously required human intervention.
Scalability and customization
The marriage of AR and IoT in manufacturing also paves the way for greater scalability and customization in production processes. As consumer demands evolve towards wanting more personalized products, traditional manufacturing setups struggle to keep up. However, with real-time data flow and visual feedback mechanisms, manufacturers can quickly adapt and modify production lines.
For instance, if a particular product variant sees a sudden spike in demand, IoT sensors on the production line can relay this information in real-time. Operators, equipped with AR tools, can then visualize the changes needed on the production line to accommodate this demand and implement them rapidly, ensuring that production always aligns with market needs.
A sustainable manufacturing model
With the world becoming more conscious of sustainability, industries are under pressure to adopt greener practices. The integration of AR and IoT provides a robust framework for achieving this in manufacturing.
Real-time monitoring of energy consumption, waste production, and resource usage through IoT, visualized effectively using AR, can help manufacturers identify inefficiencies and wastage. This not only leads to cost savings but also promotes a more sustainable and eco-friendly production model. Additionally, by optimizing machine maintenance and operations through predictive insights, the overall carbon footprint of manufacturing processes can be significantly reduced.
The takeaway
As the boundaries between the digital and physical worlds blur, manufacturers are provided with tools and insights that were previously the stuff of science fiction. With increased efficiency, reduced costs, enhanced scalability, and a move towards sustainability, the combined power of AR and IoT is set to redefine the future of smart manufacturing. As we stand on the cusp of this new era, it’s clear that the factories of the future will be smarter, more responsive, and more innovative than we ever imagined.