From onboarding to daily work and operating machinery
What does automation mean in manufacturing?
Automation in manufacturing refers to the introduction of machinery, technology, and control systems that minimize the need for human intervention in various production processes. It’s all about streamlining operations, boosting efficiency, and reducing costs by replacing or assisting human labor with automated solutions.
In practical terms, automation involves using robotic systems like industrial robots to take on repetitive or physically strenuous tasks with unmatched precision and speed. These robots can handle materials, carry out assembly processes, and even perform quality inspections. Another aspect of automation lies in computer-controlled machines, such as CNC machines, which can flawlessly shape and fabricate components based on digital designs and instructions.
Automation extends beyond physical tasks. It involves employing control systems and software to oversee and regulate production processes. These smart systems can manage inventory, optimize production schedules, and ensure smooth material flow throughout the manufacturing facility. By leveraging these automated control systems, manufacturers gain access to real-time data collection and analysis, enabling them to monitor key performance indicators, spot inefficiencies, and make data-driven decisions to improve overall operational performance.
In essence, automation in manufacturing represents a shift in how tasks and processes are approached. It strives to optimize operations, boost productivity, and enhance overall efficiency by harnessing the power of machinery, control systems, and advanced technologies. By embracing automation, manufacturers can achieve greater output, improve product quality, and create safer work environments, ultimately driving success in an increasingly competitive industry.
What are the 4 types of automation?
There are four main types of automation commonly found in the manufacturing industry. Let’s break them down in a more human-friendly way:
Fixed automation
This type of automation involves using specialized machinery and equipment designed to perform a specific set of tasks. Picture assembly lines, conveyor systems, or transfer machines that are dedicated to producing a particular product. Fixed automation works best for high-volume production where the product specifications remain consistent. It’s like having a well-oiled machine that excels at one specific job.
Programmable automation
With programmable automation, we step into the realm of computerized control systems. These systems can be programmed to automate a range of tasks or processes. Unlike fixed automation, programmable automation offers greater flexibility and adaptability. You can modify the instructions or settings to handle different operations or product configurations. Programmable logic controllers (PLCs) are commonly used in this type of automation, giving manufacturers the ability to tackle medium-volume production with some variation.
Flexible automation
Imagine taking adaptability to a whole new level. Flexible automation uses advanced technologies like robotics and computer numerical control (CNC) systems. These systems can be reprogrammed, reconfigured, or retooled to handle different product types, sizes, or variations. The beauty of flexible automation is that it allows manufacturers to quickly switch between product configurations, making it perfect for scenarios where there’s a high mix of products or customization. It’s like having a versatile and agile team that can adapt to different challenges.
Integrated automation
This type of automation is all about seamless integration and coordination. It brings together various automation technologies, control systems, and equipment to create a comprehensive and interconnected system. With integrated automation, different types of automation, like fixed, programmable, and flexible, work together harmoniously. It’s like having a unified team that communicates effectively, shares information, and optimizes processes in real-time. This level of integration enables manufacturers to monitor, synchronize, and optimize their manufacturing operations, leading to improved efficiency, productivity, and decision-making.
What is worth remembering ist that the above types of automation exist on a spectrum, with each type offering different levels of flexibility and control. Manufacturers often utilize a combination of automation types based on their specific production needs. By finding the right balance between efficiency and adaptability, manufacturers can harness the power of automation to drive success in the ever-evolving manufacturing landscape.
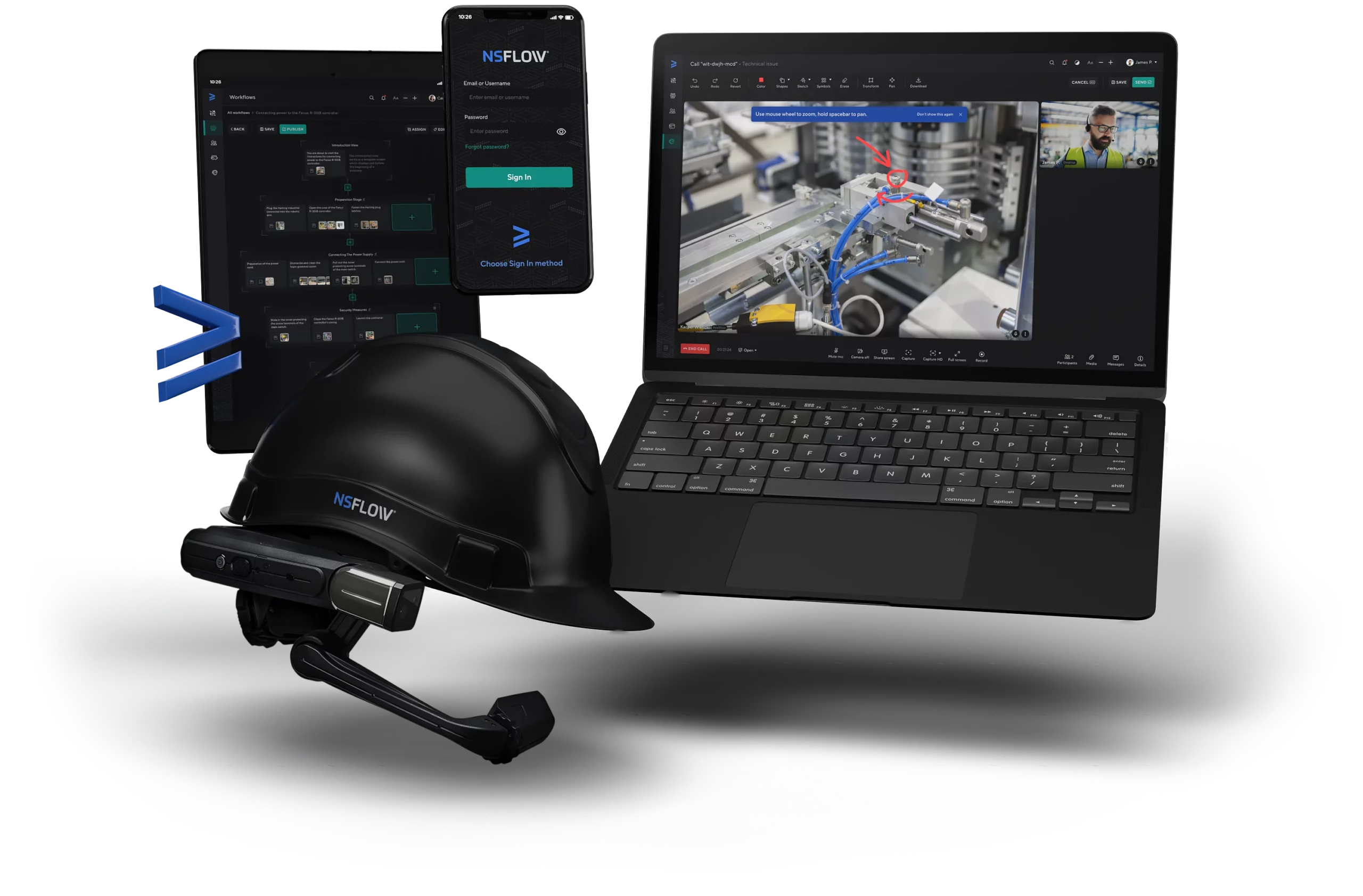
presentation to try
Nsflow in action
What are the types of automation used in manufacturing?
Automation plays a crucial role in the manufacturing industry, offering a variety of approaches to streamline processes and boost productivity. When diving deeper into the types of automation commonly used in manufacturing, we can meet such approaches as:
Robotic automation
Industrial robots have become a staple in manufacturing, performing tasks that were traditionally handled by humans. These programmable machines excel at assembly, welding, material handling, and inspection, delivering speed, precision, and consistency. By deploying robotic automation, manufacturers can improve efficiency, increase output, and reduce the risk of human error in repetitive tasks.
Conveyor automation
Conveyor systems are integral to moving materials, components, or finished products between different stages of the manufacturing process. Conveyor belts, rollers, or automated guided vehicles (AGVs) facilitate the smooth flow of items along predefined paths. Conveyor automation eliminates the need for manual handling, optimizing material handling and logistics, reducing delays, and enhancing overall production efficiency.
Machine vision automation
Machine vision automation employs cameras, sensors, and advanced image processing software to inspect, identify, and analyze objects or products. By automating visual inspections, machine vision systems can detect defects, perform measurements, and ensure compliance with specifications. This technology significantly enhances quality control efforts, reduces the reliance on manual inspections, and improves overall product quality.
Programmable Logic Controller (PLC) Automation
Programmable logic controllers are specialized computers used to control and monitor industrial processes. PLC automation involves programming these devices with specific instructions to automate machinery, equipment, and production lines. By leveraging PLCs, manufacturers achieve precise control, coordination, and sequencing of manufacturing operations, resulting in efficient and reliable processes.
Computer Numerical Control (CNC) Automation
CNC automation relies on computer-controlled machines to execute precise manufacturing operations, such as milling, turning, drilling, or cutting. By following digital instructions and designs, CNC machines shape materials with exceptional accuracy and repeatability. CNC automation improves productivity, reduces human error, and enables complex manufacturing processes.
Internet of Things (IoT) Automation
IoT automation integrates physical devices, sensors, and connectivity to enable communication and data exchange between machines and systems. By collecting real-time data, IoT automation facilitates predictive maintenance, remote monitoring, and optimization of manufacturing processes. It empowers manufacturers with data-driven decision-making, leading to increased operational efficiency and improved resource management.
Assembly line automation
Assembly line automation involves organizing manufacturing tasks into a sequenced flow of operations performed by machines, workers, or a combination of both. This approach optimizes the movement of materials, reduces bottlenecks, and boosts throughput. Assembly line automation often incorporates various automation technologies, including robotics, conveyors, and sensors, to automate assembly processes and achieve high production efficiency.
Manufacturers strategically select and integrate these types of automation based on their specific production requirements and objectives. By embracing automation, manufacturers gain the advantages of improved efficiency, enhanced quality control, increased output, and cost savings, allowing them to remain competitive in today’s rapidly evolving manufacturing landscape.
Why automation is important in manufacturing industry?
Automation plays a vital role in the manufacturing industry due to several compelling reasons. Ceding mundane tasks to smart machines significantly enhances productivity and efficiency. By automating repetitive and time-consuming tasks, manufacturers can achieve faster production rates, reduce cycle times, and optimize overall operational efficiency. Automation minimizes the risk of human error, ensuring consistent and accurate results, leading to higher-quality products and reduced waste. You can also use all in one CRM to streamlined processes and increased productivity, manufacturers can meet customer demands more effectively and gain a competitive edge in the market.
Automation enables cost savings and improved cost-effectiveness. While the initial investment in automation technology may be significant, the long-term benefits outweigh the costs. Automation reduces labor expenses by replacing or augmenting human labor, particularly in tasks that are physically demanding, repetitive, or hazardous. Additionally, automation enhances resource utilization by optimizing material handling, reducing downtime, and minimizing energy consumption. By reducing operational costs, manufacturers can allocate resources more efficiently, invest in innovation, and remain financially competitive in the industry.
Last but not least, automation plays a crucial role in improving workplace safety. By replacing humans in hazardous or physically demanding tasks, automation reduces the risk of accidents, injuries, and occupational health issues. Machines and robots are designed to perform tasks with precision and consistency, minimizing the potential for human error-related incidents. Automation also enables remote monitoring and control, allowing workers to operate in safer environments and minimizing their exposure to potential hazards. The focus on workplace safety not only protects workers but also ensures compliance with regulations and promotes a positive work culture.
The rise of automation in manufacturing is an exciting development, promising significant benefits for manufacturers, workers, and consumers. As we look ahead, it’s clear that automation will continue to play a pivotal role in shaping the future of manufacturing. However, to fully harness the benefits of automation, businesses need to invest in upskilling their workforce, implementing the right technologies, and fostering a culture of continuous learning and innovation. With the right strategy and mindset, automation can be a powerful tool for manufacturers to increase their competitiveness, create better products, and build a more sustainable and resilient future.
Are you curious about incorporating augmented reality into your operations to automate industrial processes? Book your free demo and see for yourself how AR helps with automating everyday tasks.