Digital thread who?
The digital thread in manufacturing refers to the seamless flow of digital information throughout the entire lifecycle of a product, from its design and engineering phases to manufacturing, distribution, and even post-sales support. It involves the integration and synchronization of data from various stages, processes, and systems involved in the product’s journey. Digital threading aims to provide a comprehensive and interconnected view of the product, enabling improved visibility, traceability, collaboration, and data-driven decision-making.
At its core, the digital thread captures and connects relevant data and information from different sources, including design specifications, engineering changes, manufacturing instructions, quality control data, supply chain details, and maintenance records. This integrated flow of data allows stakeholders to follow the product’s lifecycle and access crucial information at each stage. It ensures that everyone involved in the manufacturing process, including designers, engineers, manufacturers, suppliers, and service teams, can access accurate and up-to-date information, enabling better collaboration and informed decision-making.
What is the purpose of using a digital thread?
Using a digital thread in manufacturing has a clear purpose: to improve visibility, traceability, collaboration, and data-driven decision-making throughout the product’s lifecycle. It’s all about capturing and integrating data from different stages, processes, and systems to create a smooth flow of digital information. This enables companies to get a full picture of the product’s journey and make well-informed decisions based on up-to-date data, ultimately leading to better efficiency and higher product quality.
One great advantage of the digital thread is its ability to foster collaboration and communication across teams and stakeholders. By centralizing and sharing data in a digital format, teams can work together more effectively, minimizing errors, delays, and miscommunication. For instance, design teams can team up with manufacturing teams to ensure that product designs are perfectly optimized for production. Maintenance teams can access relevant data and instructions precisely when needed, enabling them to carry out timely and effective maintenance tasks. The digital thread breaks down silos and promotes collaboration, bringing teams together to achieve common goals, empowering companies with a holistic view of the product’s lifecycle, equipping them to make informed decisions based on real-time data, and encouraging effective teamwork.
What is the digital thread in Product Lifecycle Management (PLM)?
In the scope of PLM, the digital thread involves the integration of digital information and processes across the entire lifecycle of a product. PLM systems act as the backbone of the digital thread by providing a centralized platform for managing product data, documents, and workflows. By connecting various PLM modules such as CAD (Computer-Aided Design), CAM (Computer-Aided Manufacturing), CAE (Computer-Aided Engineering), and PDM (Product Data Management), the digital thread ensures a seamless exchange of information and a holistic view of the product.
The digital thread in PLM facilitates collaboration between different departments, such as design and manufacturing, by enabling real-time data sharing and synchronization. Design changes or updates made in one phase of the product lifecycle are automatically propagated to subsequent stages, eliminating the need for manual data transfers and reducing errors, ultimately leading to increased efficiency, reduced time to market, and enhanced product quality.
What are digital thread components?
The digital thread relies on a combination of components and technologies to effectively connect and manage data throughout the product lifecycle. One key component is the Internet of Things (IoT), which enables the collection of real-time data from sensors embedded in manufacturing equipment or products themselves. This data is then transmitted and analyzed to gain insights into performance, quality, and maintenance needs, supporting predictive maintenance and optimizing production processes.
Cloud computing plays a vital role in the digital thread by providing scalable and secure storage solutions for vast amounts of data generated during the product lifecycle. Cloud-based platforms also facilitate collaboration by enabling geographically dispersed teams to access and share information in real-time. Moreover, big data analytics and artificial intelligence are essential components for extracting valuable insights from the massive volumes of data generated by the digital thread. These technologies can identify patterns, detect anomalies, and optimize processes, leading to improved decision-making and operational efficiency.
Standardized data formats and interoperability are fundamental to the success of the digital thread. By adopting industry standards such as STEP (Standard for the Exchange of Product Model Data) or PLMXML (Product Lifecycle Management eXtensible Markup Language), manufacturers ensure that data can be seamlessly exchanged and interpreted across different software applications and systems. Interoperability between various tools, such as CAD and CAM software, allows for smooth transitions between design and manufacturing stages, reducing errors and enabling efficient data transfer.
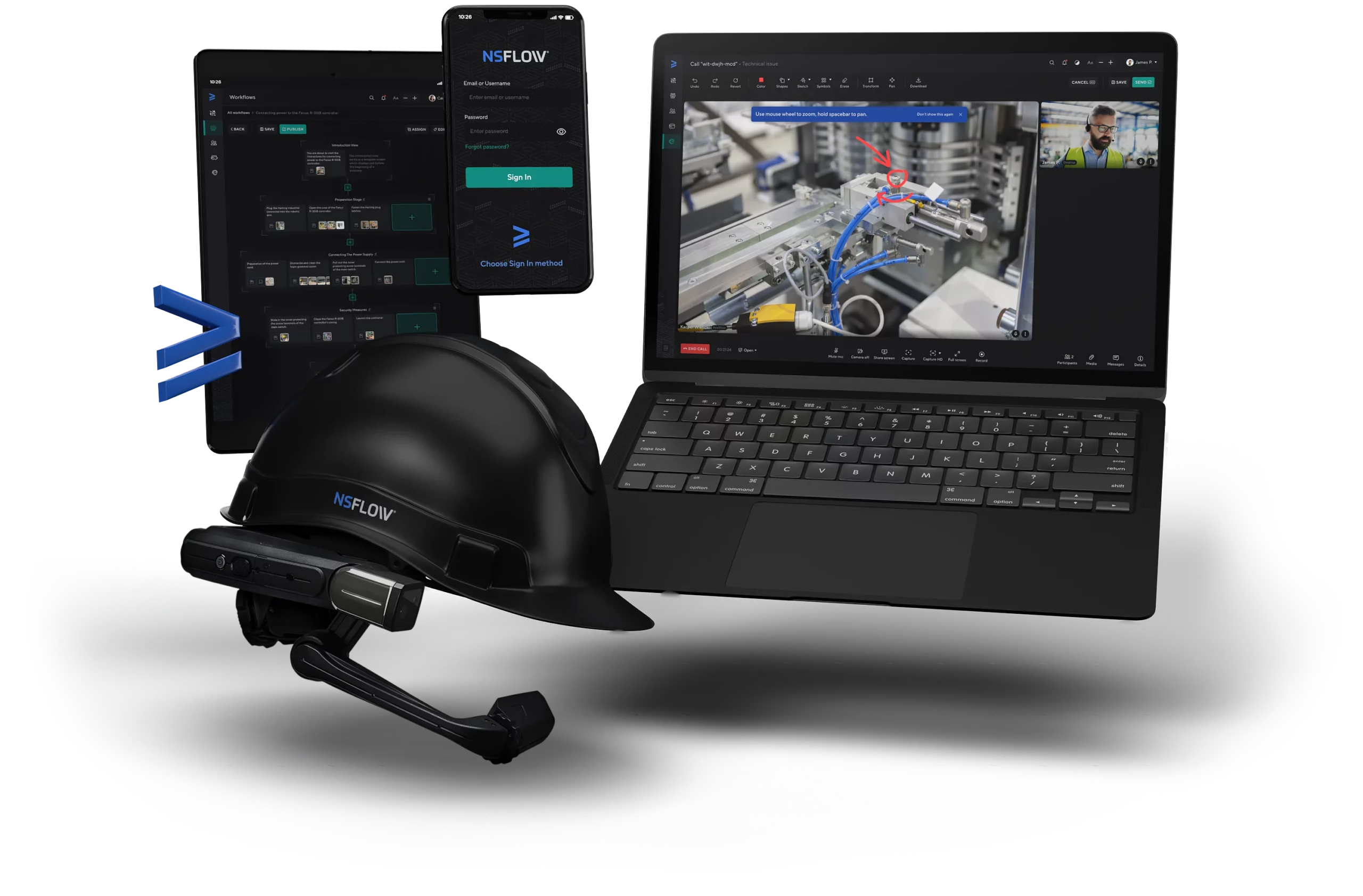
presentation to try
Nsflow in action
What is the digital thread for Smart Manufacturing?
The digital thread plays a pivotal role in enabling the realization of smart manufacturing initiatives. By connecting various data sources and systems across the manufacturing ecosystem, the digital thread facilitates automation, real-time monitoring, and predictive maintenance. It allows manufacturers to capture data from sensors, machines, and production lines, providing valuable insights into performance, quality, and efficiency. With real-time visibility into these metrics, manufacturers can optimize production processes, identify bottlenecks, and make data-driven decisions to enhance productivity.
Through the digital thread, manufacturers can implement advanced analytics and machine learning algorithms to analyze the collected data and uncover hidden patterns or anomalies. This enables predictive maintenance, where equipment health and maintenance requirements are monitored continuously. By predicting potential failures or maintenance needs, manufacturers can schedule proactive maintenance activities, reducing unplanned downtime and optimizing maintenance costs.
Additionally, the digital thread enables greater agility in response to changing customer demands or market conditions. With real-time visibility into product data and manufacturing processes, manufacturers can quickly adapt production schedules, modify designs, or introduce product variations to meet customer expectations. This flexibility enhances customer satisfaction, reduces time to market, and improves overall competitiveness in the rapidly evolving manufacturing landscape.
What is a model-based digital thread?
The model-based digital thread revolutionizes manufacturing by utilizing digital models, simulations, and virtual replicas to enhance the production process. By creating and managing digital twins, manufacturers can test and optimize designs before physical production, reducing the reliance on costly physical prototypes. This approach enables virtual simulations for evaluating design alternatives, testing assembly processes, and optimizing production sequences. With the model-based digital thread, manufacturers can ensure smoother production ramp-up through virtual commissioning, validating machine behavior before installation.
One significant advantage of the model-based digital thread is its ability to capture and share knowledge. By integrating design and manufacturing knowledge within digital models, expertise and best practices can be preserved and shared across projects and teams. This promotes innovation, accelerates learning curves, and drives continuous improvement in manufacturing processes. With the model-based digital thread, manufacturers can make informed decisions, reduce costs, and enhance overall efficiency, ultimately leading to improved product quality and customer satisfaction.
Digital thread example
In the automotive industry, the implementation of a digital thread can be observed throughout the entire lifecycle of a car model. Starting with the design phase, engineers create detailed 3D CAD models that outline the components, dimensions, and assembly requirements of the vehicle. These design specifications are digitally captured and become an integral part of the digital thread. Any revisions or modifications made during the design process are recorded, creating a comprehensive history of design iterations.
As the car transitions to the manufacturing phase, the digital thread continues to play a significant role. Manufacturing instructions, including assembly steps, tooling requirements, and quality control guidelines, are linked to the digital thread. This ensures that accurate instructions are provided to the manufacturing teams. Throughout the manufacturing processes, crucial data related to production, such as machine settings, inspection results, and process parameters, is associated with the digital thread. This information contributes to traceability and quality control efforts, enabling manufacturers to monitor and optimize their production processes effectively.
The digital thread extends beyond the manufacturing facility to include the integration of supply chain data. Supplier information, including component specifications, certifications, and delivery schedules, is integrated into the digital thread. This integration enhances visibility and traceability throughout the supply chain, enabling manufacturers to ensure the availability of the right components at the right time. The digital thread also plays a role in maintenance and servicing once the car is sold. Service and maintenance records, maintenance schedules, repair history, and customer feedback are linked to the digital thread. This comprehensive overview of the car’s maintenance history supports proactive maintenance planning and enables timely addressing of potential issues.
The takeaway
The digital thread in manufacturing represents a transformative concept that enables enhanced collaboration, traceability, and agility throughout the product lifecycle. By implementing a digital thread, manufacturers can realize improved operational efficiency, accelerated time to market, and enhanced product quality. From PLM integration to smart manufacturing and model-based approaches, the digital thread empowers manufacturers to unlock new levels of innovation and competitiveness. Embracing the digital thread is not only a necessity but also an opportunity for manufacturers to thrive in the dynamic and increasingly digitalized manufacturing landscape.