The manufacturing industry faces various challenges. Aside from lengthy and costly supply chains, transfer of production facilities to own or neighboring countries as a means of savings, and the constant search for advanced technologies to improve processes, another core area to deal with is the workforce. To be even more specific, highly-skilled workers. Employee turnover can endanger operational continuity and as such, requires particular attention from managers. Truth is, talent is scarce and employers need to fight for it.
What causes a shortage of labor?
Generational change and other misfortunes give industrial managers a headache.
Risks of employee outflow
The ongoing generational change takes its toll. In the upcoming years, most of the so-called Baby-Boomers will retire. This generation carries many longtime employees, who mastered their skills perfectly but often didn’t raise their replacement. Market success and operational continuity depend not only on the company’s physical assets but on what’s intangible: knowledge. Their retirement means most of their expertise will leave the company together with them, forcing businesses to tackle the problem of fading tribal knowledge.
Global changes
Most probably, everyone who tried to answer the “where will you be in 5 years?” question in 2016 turned out to be wrong. The pandemic and war changed the world we know, and industries also shifted significantly. A sudden growth of remote work opportunities, and greater demand for new services, but at the same time, snowballing burnout among the workforce are non-negligible. Recent years brought to attention the Great Resignation movement, also known as the Great Reshuffle or the Big Quit, a global trend of professionals voluntarily resigning from their jobs. While the tendency began even a decade earlier, the wider public became aware of a higher-than-usual number of employees quitting due to a lack of satisfaction in their current jobs. The Great Resignation is an alarming trend, requiring business owners to respond with changes in their processes to retain a skilled workforce in the changing market.
What can companies do to keep experts aboard and invite new ones?
As they say, in love and manufacturing, no holds barred. Depending on who you ask, answers will vary. From investing in employer branding, and focusing on media presence to providing a unique working experience, companies have a wide array of improvements to choose from. We’re all for utilizing the possible tech solutions in favor of your operations – in this case, retaining your experts and attracting new ones.
What are the most widespread methods for eliminating labor shortages?
How does technology help in tackling the labor shortage? Various solutions can aid the process of retaining skilled workers, and since augmented reality is our thing, we’ll focus on its usability.
Augmented reality offers previously unknown potential for aggregating, standardizing, and distributing knowledge. With such support, no employee is left out in the dark when it comes to learning and researching information. No more tedious paper copies, extensive manuals to flip through anytime an unusual procedure needs to be examined, no more issues with files update across the company – everything is accessible 24/h to every employee. Labor shortage solutions need to answer not only the business requirements but also should be beneficial to employees.
AR-powered training
Incorporating augmented reality into training processes provides a number of benefits. AR-powered training has its charm as a future-forward novelty, utilizing state-of-the-art technology, but also comes with tangible advantages. It requires less direct support from instructors, reducing their workload and allowing them to oversee larger groups of trainees simultaneously. Digital instructions guide course participants through necessary steps, showing subsequent actions to perform and verifying if tasks are completed correctly. The course execution is saved in the platform for future analysis, enabling managers to utilize the data for optimizing learning processes. Advanced reporting provides conclusive information on trainees’ performance, the number of errors, and potential bottlenecks in the process.
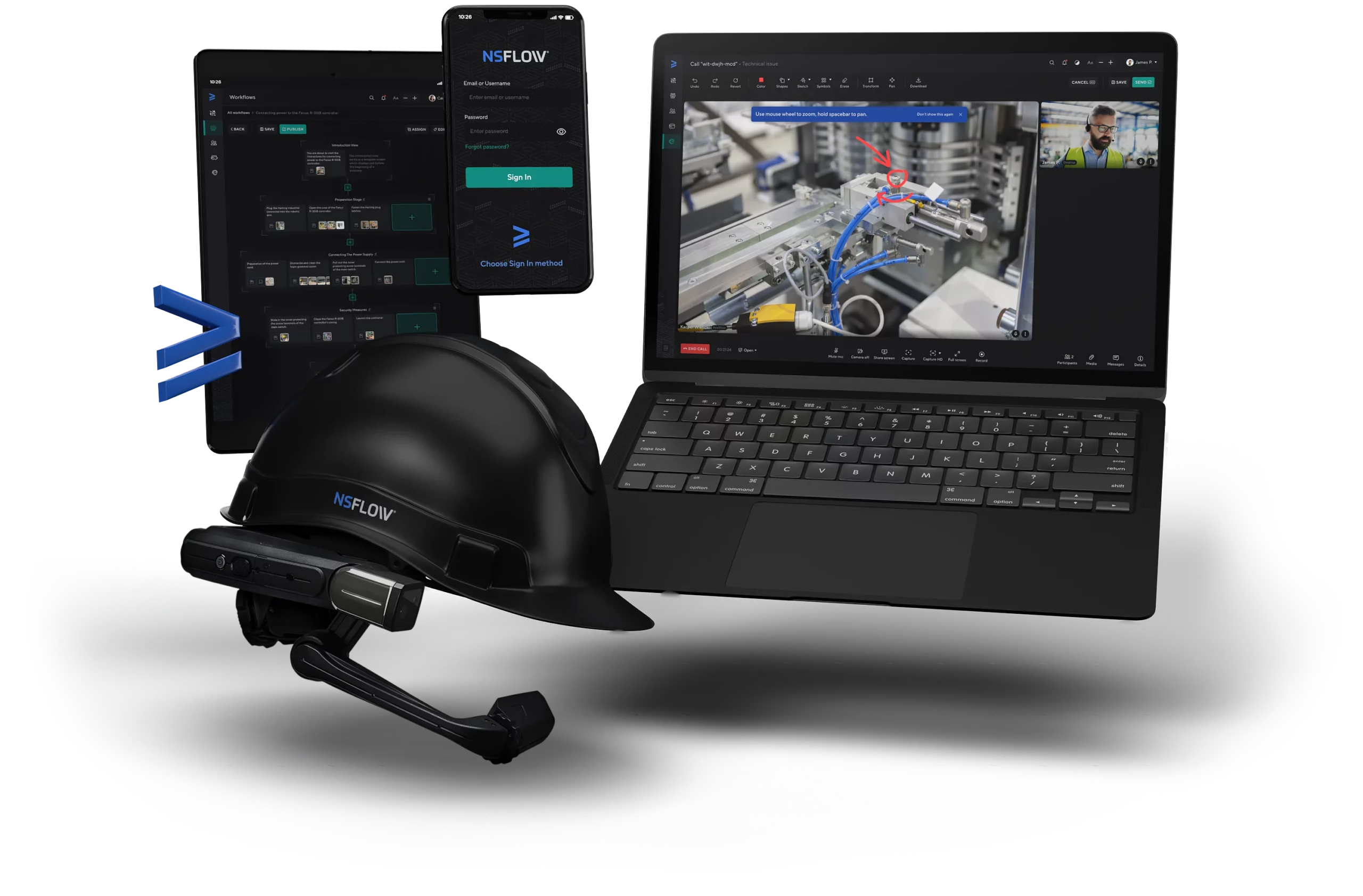
presentation to try
Nsflow in action
Building the brand image
Industrial companies transform digitally to face the challenges of the modern-day world. Traditional businesses also have their place in the market but when it comes to global operations and wide-scale production, at some point, tradition must meet innovation. Incorporating new technologies is the way to secure internal know-how and optimize the manufacturing process and build the brand image.
Companies in times of Industry 4.0 can win experts by offering a competitive salary (probably most experts truly detest this catchphrase) and by becoming innovation and thought leaders in their field. When choosing between similar positions in different organizations, many specialists select the offer backed by the newest yet proven technologies, promising development and growth opportunities.
Remote access
While desk jobs turned out to be relatively easy to perform at the home office, for many enterprises (often despite their previous hesitance in allowing employees to work remotely), industrial positions were a tougher nut to crack. Manufacturing facilities run production lines requiring direct supervision in most cases. Luckily, augmented reality enabled the facilitation of processes, reducing the need for the on-site presence of professionals. In addition, implementation of AR allows for the execution of complex procedures, previously impossible to execute remotely like Factory Acceptance Tests (FAT).
Knowledge management
Securing internal know-how is crucial to training new generations of employees. Lack of knowledge transfer standards results in information chaos, severely affecting the skill-building process. Employees who undergo well-executed onboarding processes are more likely to be satisfied with their training and are more willing to remain in the company. Technological solutions like augmented reality enable managers and trainers to provide new hires with digital training tailored to the position’s requirements. With AR, every employee can learn and undergo hands-on training, having access to all necessary information with no need to muddle through extensive paper manuals.
How can we fix labor shortages?
Technology’s relevance in workforce retention will only continue to grow. State-of-the-art solutions offer significant relief in resolving challenges faced by industrial enterprises daily. Industries with labor shortages need to transform to adapt to the new reality and offer a workplace attracting new candidates. While business observers note the labor market is facing temporary difficulties, the market still belongs to the employees. Meaning companies can’t expect candidates to beat down their doors just because there are vacancies. Specialists, from technicians to high-profile experts, are confident enough to search for jobs suiting their needs and wants best. Hence, transforming companies digitally sounds like one of the best options to secure employers’ attractiveness.