Downtime in manufacturing refers to any period during which a system or machinery is unavailable or unable to operate as intended. It’s an unavoidable reality of the industry, but if unmanaged, it can lead to substantial financial losses. This article will delve into this crucial topic and explore effective strategies to mitigate its impact.
The cost of downtime in manufacturing is not just about immediate losses due to halted production. It also includes potential revenue losses from delayed deliveries, damage to the company’s reputation, and the cost of repairs and recovery. The goal of this article is to provide insights on how to manage and reduce these costs.
Understanding downtime in manufacturing
Downtime in manufacturing can be classified into two types: planned and unplanned. Planned downtime includes scheduled maintenance, updates, or upgrades, while unplanned downtime often results from equipment failure, power outages, or human errors. While planned downtime can be managed, it’s the unplanned events that can significantly disrupt production.
Apart from the immediate loss of production and sales, downtime can lead to a cascade of adverse effects. This includes opportunity costs such as lost business due to unfulfilled orders, potential penalty costs related to service level agreements (SLAs), and a decrease in overall productivity as workers idle. The resulting backlogs when systems are up and running again can also lead to overtime costs. Furthermore, in a production line, a single machine failure can halt the entire production, magnifying the cost of downtime.
The cost of downtime also includes less tangible but equally damaging impacts. For instance, frequent and prolonged downtime can harm a company’s reputation, leading to loss of customer trust and potential future sales. It can also provide a competitive edge to rivals. Furthermore, if the downtime affects critical operations like customer service, order processing, or delivery, it can lead to customer dissatisfaction and churn. It is crucial for businesses to factor in all these direct and indirect costs while calculating the cost of downtime, and more importantly, in strategizing their downtime prevention and mitigation plans.
Downtime in equipment can be triggered by numerous factors such as wear and tear, incorrect operation, or software issues. Machine downtime, in particular, is a frequent offender, often due to insufficient maintenance. Addressing these causes proactively can go a long way in avoiding disruption.
Take the case of a leading automobile manufacturer, for instance. A sudden machine breakdown led to an unplanned halt in production, delaying deliveries and impacting their market reputation significantly. The event underscored the urgent need for preemptive strategies to tackle such situations.
The financial impact of downtime
Calculating downtime in production is crucial to understanding its true cost. It involves determining the duration of the downtime, quantifying the production loss during this period, and adding any additional costs like repairs or labor.
For instance, if an assembly line producing $5,000 worth of goods per hour halts unexpectedly for 5 hours, the direct cost of downtime is $25,000. But, this doesn’t account for other potential costs, like expedited shipping for delayed orders or overtime pay for workers.
Indirect costs of downtime also include intangible factors like customer dissatisfaction, potential loss of future business, and a decrease in the company’s market reputation. These costs, while hard to quantify, can significantly impact a company’s bottom line in the long run.
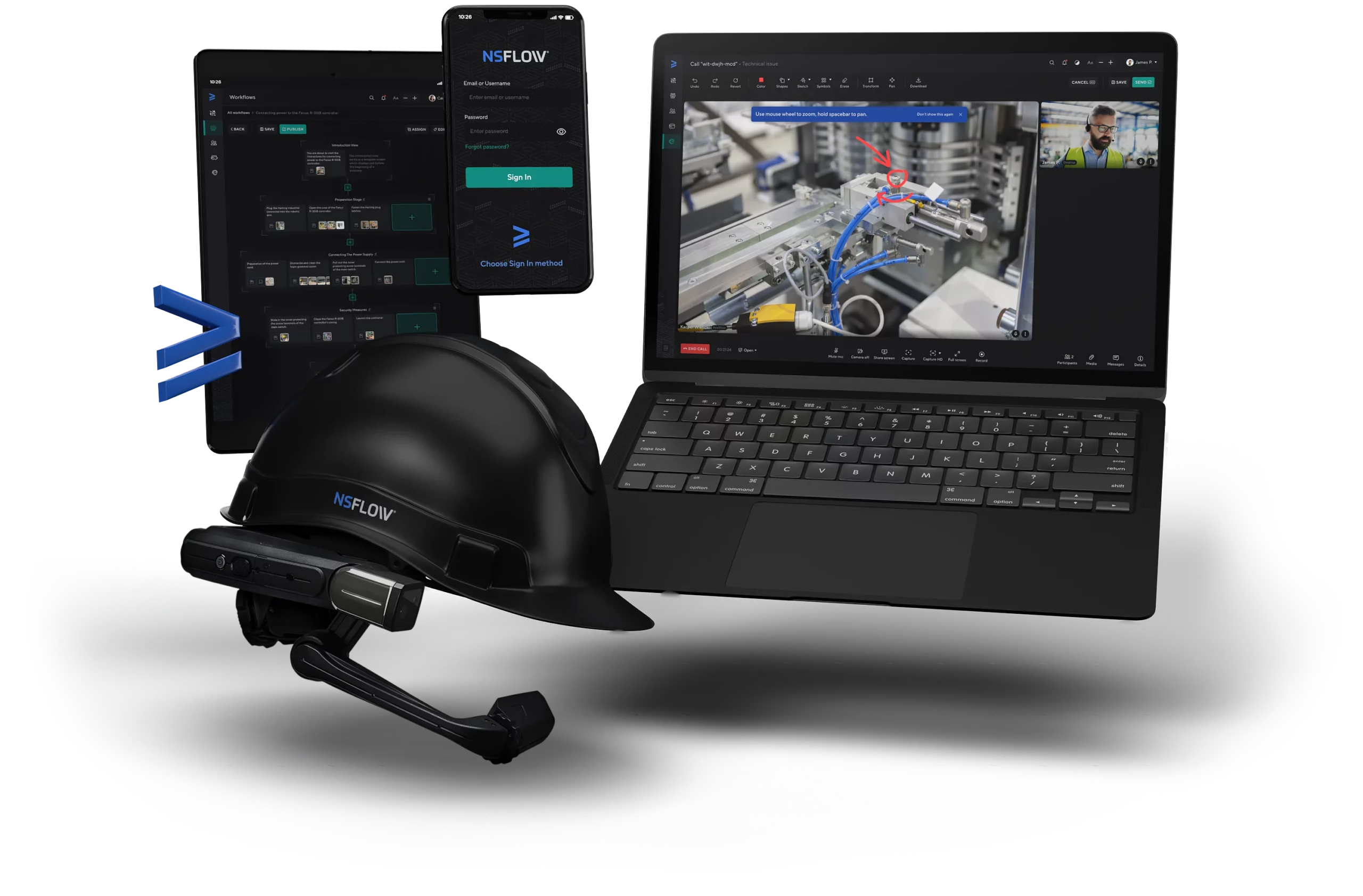
presentation to try
Nsflow in action
Downtime reduction strategies
There are several strategies to minimize production downtime. These include proactive equipment maintenance, real-time monitoring, use of quality equipment, and having a robust contingency plan. These strategies can significantly decrease both the occurrence and impact of downtime.
Proactive maintenance involves regularly scheduled inspections and upkeep to prevent equipment failure. It includes routine checks, part replacements, and software updates, all of which can prevent major malfunctions and subsequent production halts.
Reliable equipment monitoring can serve as an early warning system for potential issues, enabling companies to address problems before they cause downtime. Additionally, having a contingency plan in place can help to quickly rectify situations and resume production when downtime does occur.
The role of technology in preventing downtime
Technological solutions like IoT devices, predictive analytics, and AI have revolutionized downtime prevention, and augmented reality is no exception. These tools can monitor machine health in real-time, predict potential issues, and even automate maintenance tasks.
Predictive maintenance, fueled by machine learning and AI, can detect patterns that humans might miss, predicting potential failures before they happen. This allows for maintenance to be performed just in time, preventing unexpected production halts.
Empowering staff with the latest technologies, such as Augmented Reality (AR), can be instrumental in downtime reduction. AR can facilitate superior machine operation and problem recognition, enabling quick and precise corrective actions. It offers an interactive platform where employees can practice scenarios and become adept at handling real-life issues. An open communication culture where new technology adoption and issue reporting are encouraged is crucial.
Adopting a culture of continuous improvement through predictive and preventive maintenance is pivotal to mitigating downtime. Regular predictive analysis helps in foreseeing potential downtime incidents and formulating preemptive strategies. Learning from these predictions and implementing corrective changes helps in proactively managing equipment health, thus reducing the incidence and impact of unplanned downtime.
A unified approach to downtime reduction, involving all team members, is of utmost importance. This collaborative responsibility extends from top management to production floor workers. The combination of human vigilance and AI-driven predictive maintenance can lead to quicker identification and resolution of potential disruptions. In an environment powered by technologies like AR and predictive analytics, downtime incidents can be managed more efficiently, minimizing their overall impact on the business.
Leveraging AR for staff training is another transformative approach to downtime reduction. AR creates immersive training experiences, where employees can interact with a virtual replica of the machinery, learning its intricate workings and potential fault points. This technological aid not only accelerates the learning curve but also increases safety, as trainees can practice risk-free with virtual machines. Furthermore, AR can provide real-time data and diagnostic information to machine operators, allowing them to preemptively identify issues and reduce unplanned downtime.
The takeaway
This article has provided a deep dive into the cost of downtime in manufacturing and presented effective strategies to prevent it. From understanding what causes downtime to implementing advanced technology for prevention, we’ve covered significant ground.
The potential savings and efficiency gains from reducing downtime are immense. It not only affects the bottom line but also improves a company’s reputation and customer satisfaction. As the manufacturing sector continues to evolve, the challenge of managing downtime will remain. However, with ongoing learning and adaptation, companies can turn this challenge into an opportunity to continuously improve and optimize their manufacturing processes.
To fully grasp the importance of improving manufacturing processes and reducing downtime, we encourage you to explore further resources. Industry reports, case studies, and technological advancements in the field of manufacturing can provide additional insights into downtime management. Remember, the quest for knowledge and improvement is a never-ending process in the world of manufacturing.