Augmented reality is a groundbreaking tool transforming the way industries operate, particularly in manufacturing. AR overlays digital information into the real world, enriching user experience and providing real-time data that can significantly optimize processes.
The manufacturing industry, always on the cusp of technological innovation, has embraced AR with open arms. This adoption isn’t just a leap towards modernity—it’s a necessary evolution to meet the growing complexities of global manufacturing demands. With the convergence of the digital and physical realms, AR promises solutions to long-standing challenges while introducing new efficiencies.
At the intersection of this digital revolution, manufacturers are finding ways to harness AR to drive productivity, safety, and cost-effectiveness. As we delve deeper, we’ll explore how AR is not only fitting into but reshaping the manufacturing landscape.
Understanding AR in the manufacturing context
To fully grasp the impact of AR in manufacturing, one must first understand its essence. In simple terms, Augmented Reality enhances our perception of the physical world by layering it with virtual, contextual data. Unlike Virtual Reality (VR), which immerses users in a fully digital environment, AR integrates and complements our real-world interactions.
Historically, manufacturing has always been a frontrunner in adopting technological tools. From the advent of assembly lines to the introduction of robots, the sector has evolved by integrating technology into its core processes. Now, with AR, manufacturing stands on the precipice of another significant transformation. This tech isn’t just a new tool—it’s a bridge between human skill and digital insights.
In the context of manufacturing, AR’s potential is multifaceted. Whether it’s aiding intricate assembly tasks, facilitating complex equipment repairs, or enhancing worker training, AR promises to be an indispensable asset. As we explore its specific applications, we’ll uncover the depth and breadth of its transformative power.
Safety protocols enhanced by AR
Manufacturing plants, with their intricate machinery and bustling activity, require stringent safety protocols. Traditional training methods, while effective, often expose trainees to potential hazards. AR changes this narrative by allowing for immersive safety training simulations, reducing real-world risks during these sessions. Workers can now practice dealing with hazardous scenarios in a controlled, virtual overlay before they face them in real life.
Another great breakthrough is the advent of real-time safety alerts through AR glasses. Instead of relying solely on alarms or manual inspections, workers receive instant visual warnings about potential hazards or malfunctions. This immediate feedback mechanism can drastically reduce reaction times, minimizing the risk of accidents.
Equipment maintenance and repair are other areas where safety gets a boost from AR. Maintenance staff, equipped with AR headsets, can see visual overlays detailing the safest procedures for handling specific pieces of equipment. They can receive step-by-step guidance on repairs, ensuring that safety protocols are always front and center, even in complex procedures.
Streamlining production with AR tools
The core of manufacturing lies in production, where precision, speed, and quality converge. AR aids this core by providing real-time assembly instructions directly overlaid on the actual products. Workers no longer need to shift their attention between manuals and the task at hand. With AR glasses, they receive contextual, step-by-step guidance, reducing errors and speeding up the assembly process.
Quality assurance is another area reaping the rewards of AR integration. Traditional inspection processes, while thorough, can be time-consuming and occasionally prone to human error. With AR, inspectors get instant visual checks against predefined product standards. Any discrepancies are immediately highlighted, ensuring that only products meeting the highest quality thresholds move forward in the production chain.
Customization is a growing demand in today’s consumer-driven market. AR steps in here as well, assisting workers in customizing products based on individual specifications. Whether it’s a personalized engraving on a product or a specific color pattern, AR can guide workers through the customization process, ensuring each product aligns perfectly with individual client specs.
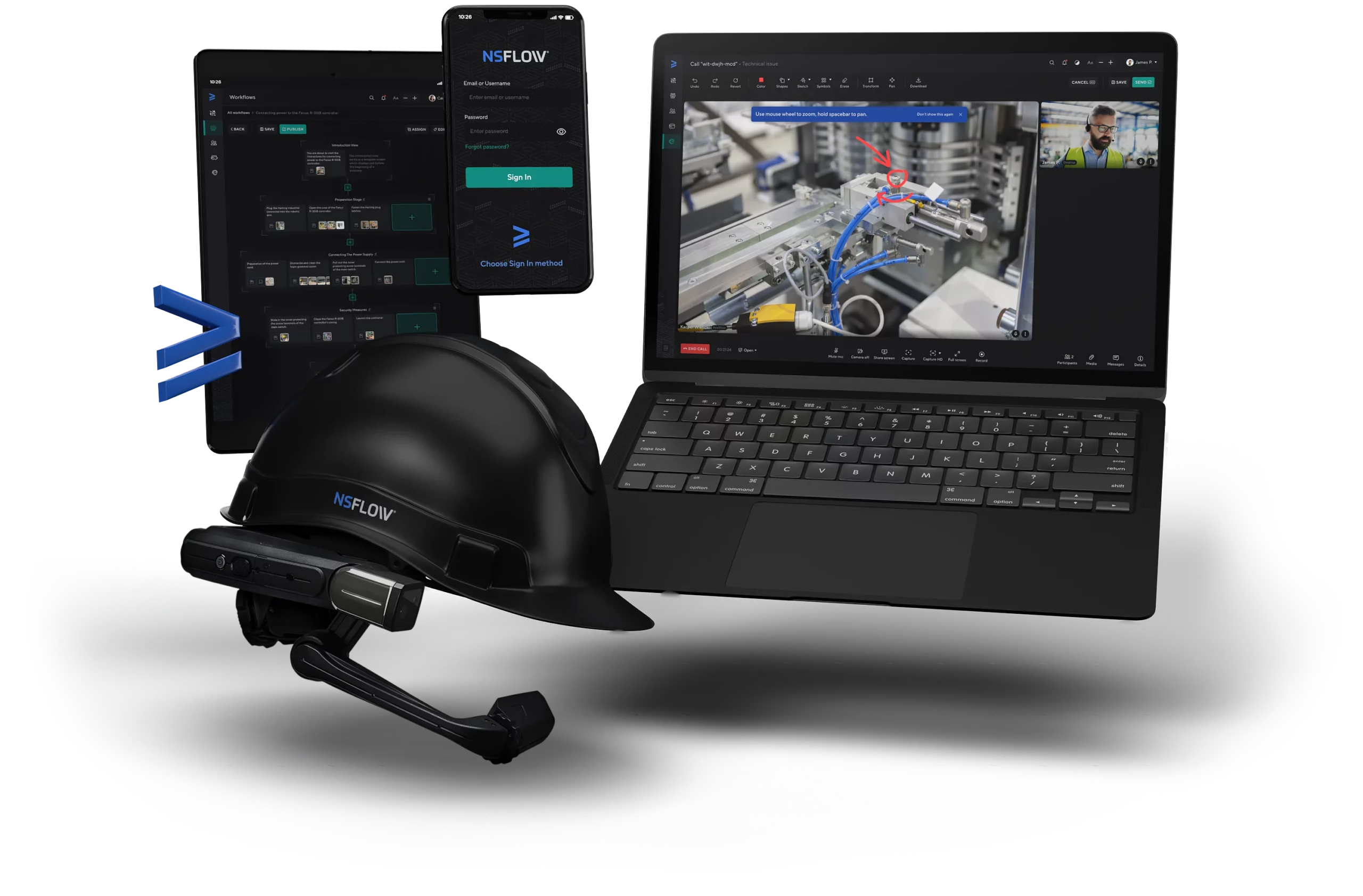
presentation to try
Nsflow in action
Maintenance and repairs revolutionized by AR
Maintenance and repairs have traditionally been tasks requiring deep expertise and often extensive reference to manuals and schematics. AR has brought about a paradigm shift in this area. With the integration of augmented reality in the maintenance process, technicians and engineers can view intricate machine parts, layered with digital information, all in real-time. This translates to more efficient troubleshooting and quicker issue resolution.
Imagine a technician wearing AR glasses, approaching a malfunctioning piece of machinery. Instead of poring over printed manuals or scrolling through digital documents, they can see digital overlays of machine components, instructions, and potential problem areas directly on the equipment. Interactive 3D models can guide them through the repair process, highlighting areas of concern.
Moreover, remote assistance has become a reality with AR. Specialists from anywhere in the world can now assist on-site technicians in real-time. They can see what the on-site technician sees and provide guidance using AR overlays, annotations, and pointers. This not only speeds up the repair process but also ensures that the expertise is available when and where it’s needed most, without the constraints of physical location.
Training and skill development with AR
One of the most transformative benefits of augmented reality in manufacturing is in the field of training and skill development. Traditional training methods often involve theoretical learning followed by practical hands-on experience. AR bridges the gap between the two, offering immersive hands-on training from the get-go.
Trainees wearing AR headsets can be guided through complex manufacturing processes step by step, with instructions and guidelines appearing right in their field of vision. This interactive mode of learning enhances retention and understanding, enabling workers to get up to speed faster and with more confidence.
Additionally, the virtual environment provided by AR allows trainees to practice without consuming real-world resources. This means they can repeat tasks, learn from mistakes, and refine their skills without wasting materials or risking damage to equipment. This virtual “sandbox” environment fosters a deeper understanding and proficiency in the tasks at hand.
Benefits of integrating AR into manufacturing
The integration of augmented reality into manufacturing is more than just a technological upgrade; it’s a strategic investment with a plethora of tangible benefits. One of the most pronounced advantages is the reduction in operational downtime. With AR-guided maintenance and repairs, issues can be identified and resolved faster, ensuring that production lines experience minimal disruptions.
Another significant benefit is the enhancement in worker efficiency and accuracy. With AR’s real-time guidance, workers can execute tasks with more precision, reducing errors and rework. This translates to higher-quality products being produced at a faster rate.
Moreover, the cost savings are notable. While the initial investment in AR technology might seem steep, the returns in terms of reduced wastage, optimized operations, and decreased downtime ensure a favorable ROI. Additionally, the potential for remote collaborations and consultations saves travel and associated costs, further underscoring the financial viability of AR in the manufacturing landscape.
The takeaway
Augmented Reality is undeniably reshaping the manufacturing landscape. From its applications in safety and quality assurance to its role in fostering collaboration and customization, AR is a game-changer. Manufacturers embracing this technology are not only optimizing their current processes but are also paving the way for a more innovative and interconnected future.