Augmented Reality (AR) has undergone rapid evolution since its inception. Initially conceived as a tool for video games and interactive media, AR has since transcended these origins, offering revolutionary applications across diverse industries. It merges the digital realm with our tangible world, overlaying digital information on real-world objects to enhance user perception and interaction.
In the realm of maintenance and repair, AR has emerged as a beacon of innovation. The sectors that traditionally grappled with time-consuming procedures, intricate manuals, and extensive training sessions are now finding solace in the efficiency and precision of AR. These enhancements, catalyzed by AR, have been instrumental in transforming troubleshooting and diagnostics, making maintenance and repair more streamlined and accessible.
While its roots may be steeped in entertainment, AR’s transformative potential in practical, real-world applications is undeniable. Whether assisting technicians in remote locations or guiding homeowners through DIY repairs, AR stands poised to redefine our approach to maintenance and repair, ushering in an era of unprecedented efficiency and accuracy.
The transformation of maintenance and repair with AR
Historically, maintenance and repair professionals had to grapple with hefty manuals, memorization of intricate procedures, and often a reliance on trial and error. Such traditional approaches, while reliable to some extent, were also time-consuming, error-prone, and could be inefficient. However, with the introduction of AR, these challenges have been considerably mitigated. Technicians can now access overlaid digital instructions on real equipment, enabling them to pinpoint problems and solve them without unnecessary delays or mistakes.
AR’s role in this transformation cannot be understated. For instance, in complex machinery repairs, technicians can leverage AR glasses to display a machine’s internal components without disassembling it. This aids in diagnosing issues faster. Furthermore, in remote areas where expert help might not be readily available, AR can bridge the gap by allowing experts to guide novices through the repair process virtually, in real-time.
These technological leaps, supported by AR, aren’t mere incremental improvements. They represent a seismic shift in how we approach maintenance and repair. By drastically reducing the time taken for tasks and minimizing errors, AR ensures that the sector is more efficient and responsive to the demands of modern-day challenges.
Key applications of AR in maintenance and repair
AR for maintenance
Predictive maintenance, a method to predict when equipment will fail, has gained significant traction in recent years. Incorporating AR into this approach has further augmented its benefits. For instance, maintenance personnel wearing AR glasses can view a machine and instantly receive data on potential wear and tear, ensuring preemptive action before a complete breakdown occurs. This not only preserves machinery longevity but also saves costs related to significant repairs and downtime.
Additionally, AR provides an avenue for remote assistance during maintenance tasks. Suppose a technician in one location encounters a machine model they’re unfamiliar with. In that case, an expert from another location can virtually guide them through the necessary procedures using AR, ensuring the task is completed efficiently. This virtual “over-the-shoulder” guidance can drastically cut down on travel costs and time.
Lastly, training new maintenance personnel has traditionally been a lengthy process, involving theoretical lessons followed by hands-on practice. However, with AR, trainees can engage in interactive simulations, learning to handle various scenarios in a controlled, risk-free environment. This accelerates the learning curve, ensuring that they are job-ready faster than traditional methods would allow.
AR repair tools and augmented repair solutions
AR has initiated a paradigm shift in repair methodologies, fostering a more intuitive and guided approach. Overlaying digital information directly onto physical equipment offers technicians real-time guidance. Imagine working on an intricate piece of machinery and having step-by-step instructions, with visual indicators, highlighting the exact components to be addressed. This not only expedites the repair process but also minimizes the likelihood of errors.
Coupled with real-time analytics and diagnostic capabilities, AR provides instant feedback to repair personnel. For instance, if a technician is addressing an engine issue, AR can simultaneously analyze engine performance data, pinpointing anomalies and suggesting appropriate remedies. Such integrations elevate the accuracy and efficiency of repair tasks.
The evolution doesn’t stop there. With the increasing integration of the Internet of Things (IoT) and machine learning, AR systems can offer enhanced repair solutions. Imagine a machine that can communicate its own wear and tear or a malfunctioning part to the AR system. The AR system, in turn, suggests the best possible solution, taking into account the machine’s history, usage patterns, and known vulnerabilities.
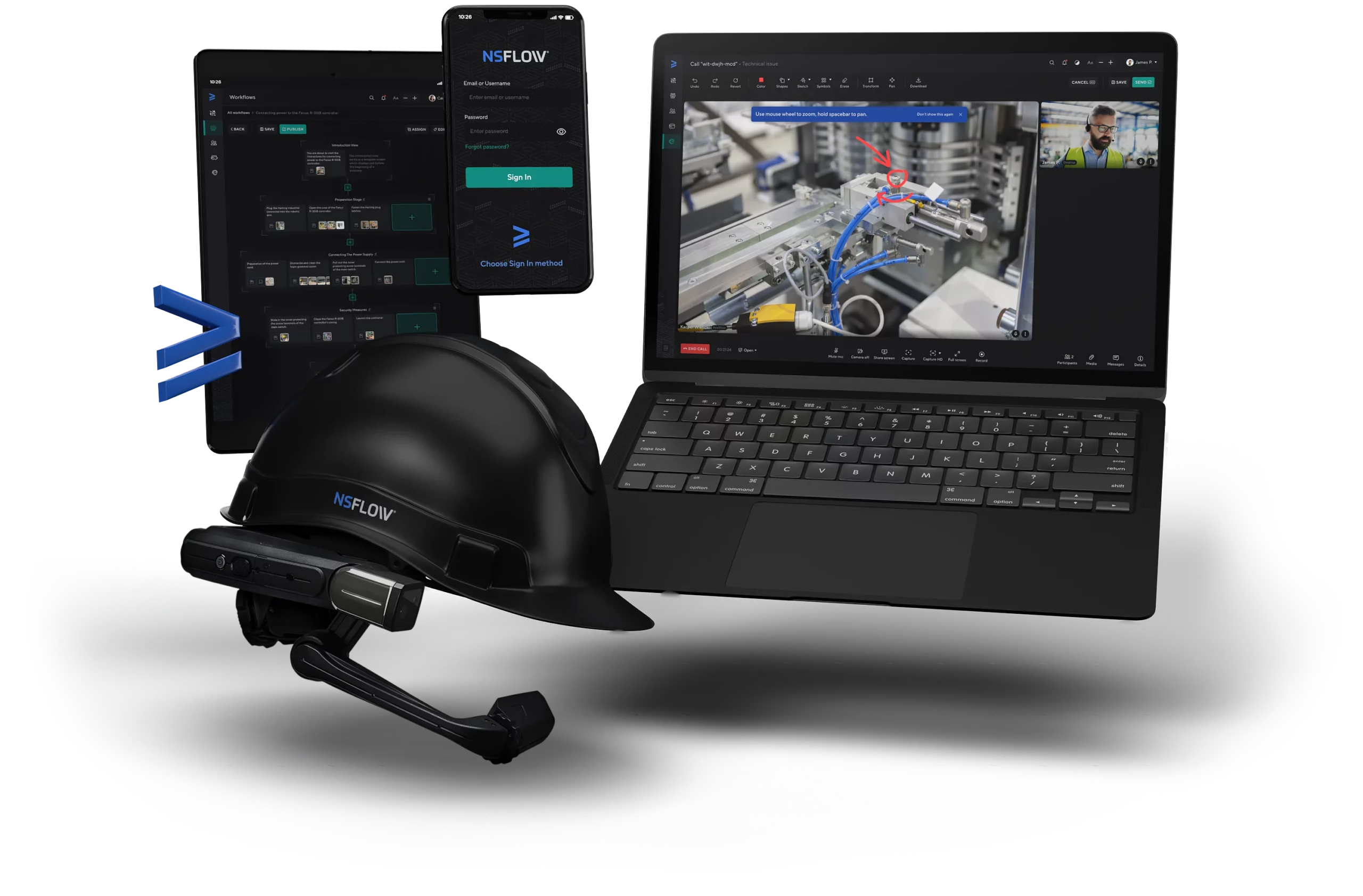
presentation to try
Nsflow in action
Benefits of AR in maintenance and repair
Enhanced efficiency
The age-old saying, “time is money,” holds true, especially in the realms of maintenance and repair. With AR, repair processes are significantly sped up. Technicians no longer need to sift through cumbersome manuals or rely on memory. AR provides immediate, context-sensitive guidance, drastically reducing the time taken for tasks.
Another noteworthy benefit is the reduction of machine downtime. For businesses, every minute a machine is non-operational, it equates to lost revenue. But with AR’s quick diagnostics and repair guidance, downtimes are minimized, ensuring that businesses can operate with minimal interruptions.
Furthermore, AR systems can provide data analytics post-repair, analyzing the efficiency of the repair and suggesting areas of improvement. Over time, this iterative feedback can further optimize repair processes, saving both time and money.
Increased accuracy
Human error remains a persistent challenge in manual repair tasks. However, AR’s guided procedures ensure that mistakes are drastically reduced. By providing precise instructions and visual indications, technicians are guided meticulously through each step, ensuring that the repair is accurate the first time around.
Moreover, AR systems can be integrated with databases containing the latest repair methodologies and best practices. This ensures that technicians are always using the most up-to-date information, further boosting the accuracy of their work.
In scenarios where precision is paramount, like aerospace or medical equipment repairs, AR proves invaluable. A minor mistake in these sectors can have significant repercussions. However, with AR’s meticulous guidance, the chances of such errors are greatly diminished.
Safety and compliance
Safety remains a primary concern in maintenance and repair tasks. Especially when dealing with high-voltage equipment or heavy machinery, the margin for error is minimal. AR aids in ensuring that safety procedures are consistently and rigorously followed. It can provide real-time safety alerts, ensuring that technicians are always aware of potential hazards.
Moreover, in regulated industries, documenting repair and maintenance activities is crucial for compliance. AR can automatically record procedures, ensuring that all actions are well-documented and can be reviewed if required. This not only ensures regulatory compliance but also provides valuable data for training and quality assurance purposes.
The takeaway
Augmented Reality, while initially a novelty in the realms of entertainment and media, has proved its mettle as a transformative tool in maintenance and repair. The union of the tangible and digital worlds has ushered in an era of enhanced efficiency, accuracy, and safety. The applications of AR in this domain, from predictive maintenance to intricate machine repairs, showcase the technology’s versatility and potential.
By embracing AR’s potential and navigating its challenges, the maintenance and repair departments in the industrial field stand to benefit immensely, ensuring that our machines and infrastructures are not only well-maintained but also future-ready.