Augmented reality (AR) has already gained recognition as a game-changing technology, poised to redefine various industries. However, while it has been rapidly embraced in modern sectors like gaming, entertainment, and the automotive sector, traditional industries have been slower in their AR adoption. In this article, we delve deeper into the potential challenges hindering this process and explore solutions to effectively overcome these roadblocks.
As we explore this topic, it is essential to understand the vast gap in AR’s distribution across sectors. Modern industries often have the potential to build their infrastructures around new technologies, but traditional industries, with their deeply rooted practices, face a more challenging path. Yet, the potential rewards from AR integration in such industries promise transformative results.
The promise of AR in industry
Augmented reality, at its core, entails the integration of digital information with the user’s physical environment in real-time. In an industrial context, this could mean overlaying real-time data on machinery or assisting a worker with real-time instructions during a complex task. The implications are profound; improved safety, enhanced efficiency, and innovative solutions that redefine operational processes.
But why should traditional industries, with their tried-and-tested methodologies, be interested? The answer lies in the potential efficiency gains, cost savings, and the proactive problem-solving ability AR brings. A malfunctioning piece of machinery could be diagnosed and repaired more efficiently, workers could receive real-time feedback on tasks, and complex training could be made more accessible with interactive AR guides.
Yet, even with these apparent benefits, traditional industries face significant challenges in adopting AR. The reasons span from infrastructural issues to workforce adaptability and economic constraints. Let’s dive deeper into these challenges.
Barriers to AR integration in traditional sectors
Technological infrastructure challenges
Traditional industries, built over decades, often rely on legacy systems and machinery. Integrating state-of-the-art AR tools with these existing infrastructures poses a significant challenge. Whether it’s software incompatibility or the need for additional sensors and equipment, the path to integration is riddled with hurdles.
Retrofitting older machinery or systems to be AR-compatible is another challenge. Not only is this process expensive, but it also requires expertise in both traditional machinery and modern AR systems, a combination that is often hard to find. Furthermore, full-scale infrastructure overhauls might disrupt operations, leading to short-term productivity losses.
Moreover, the rapid pace at which AR technology evolves means that any integration done today might become obsolete in just a few years. For industries that are used to machinery and processes that last decades, this is a significant departure from the norm and a challenge in its own right.
Organizational culture and workforce adaptability
Change is often met with resistance, especially in sectors that have operated in a specific manner for years or even decades. Employees, particularly those who have been part of an industry for a long time, might be hesitant or even outright resistant to adopting new technologies like AR, viewing it as an unnecessary complication. The learning curve associated with AR can’t be overlooked. While younger generations might be more tech-savvy, older employees might find it challenging to navigate AR interfaces. This creates a need for intensive training programs, further stretching already tight operational budgets.
Moreover, there’s an underlying fear among many workers that technology, including AR, might render their roles redundant. This fear, even if unfounded, can act as a significant barrier to AR’s adoption, as employees might see it more as a threat than an aid.
Economic considerations
While AR promises significant long-term benefits, its immediate implementation requires a substantial financial outlay. For traditional industries that often operate on slim margins, this initial investment can be daunting. Purchasing AR hardware, investing in AR software development or licensing, and training staff – all these steps require capital. On top of that, the prospect of ongoing costs associated with updates and maintenance can be intimidating for industries that are accustomed to once-off machinery purchases.
It’s also worth noting that the ROI (Return on Investment) for AR might not be immediately apparent. It may take months or even years for the efficiency gains and operational improvements to translate into tangible financial benefits. This deferred return can be a hard sell for stakeholders and investors looking for quicker paybacks. Moreover, in the case of unforeseen technological glitches or failures, the cost of downtime in traditional industries can be substantial. If an AR system fails and disrupts a production line, for example, the associated losses could outweigh the benefits the technology promises in the short term.
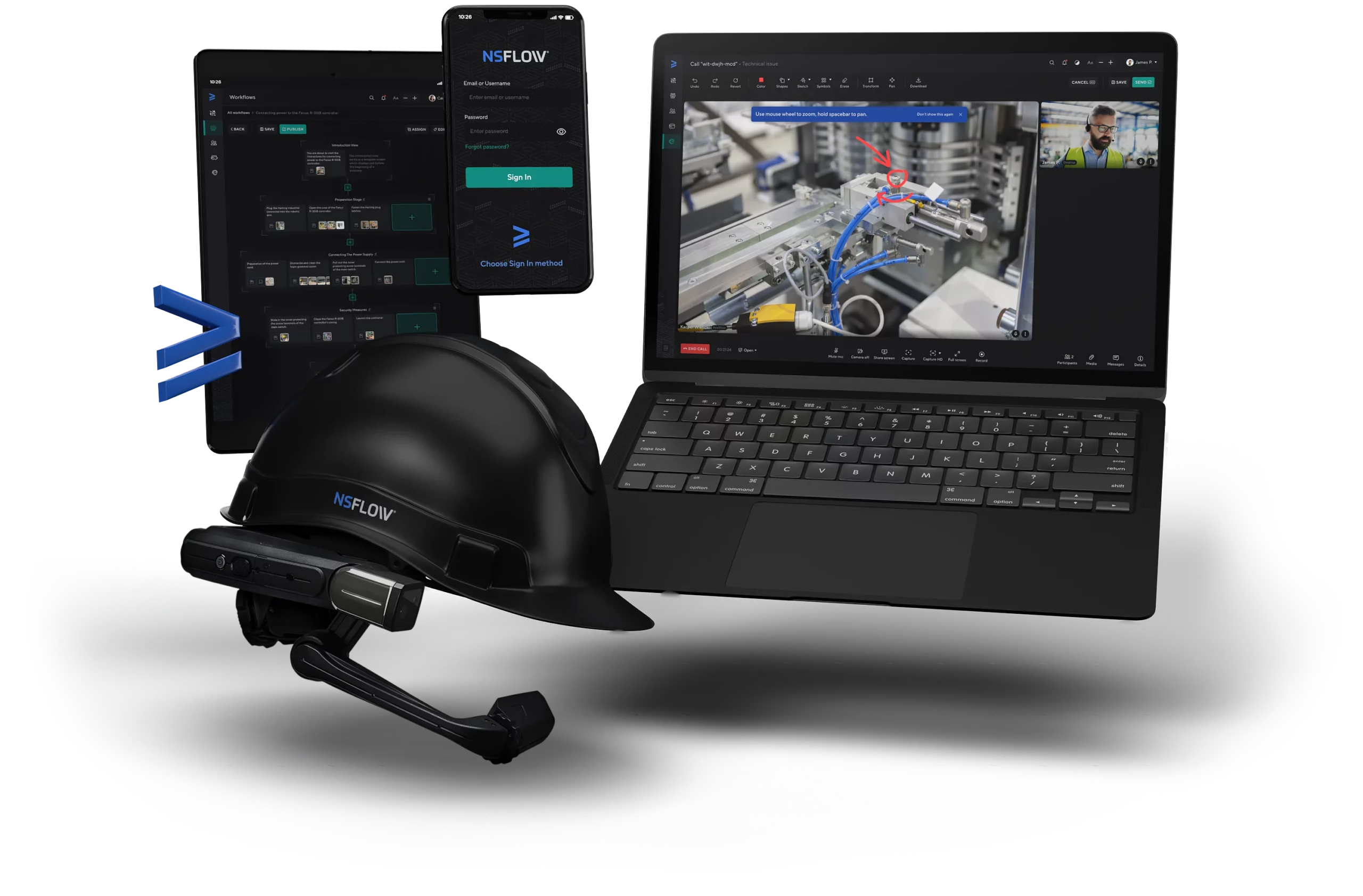
presentation to try
Nsflow in action
Strategies to overcome AR implementation barriers
Phased integration and pilot programs
Instead of a wholesale, immediate integration of AR, industries can adopt a phased approach. By implementing AR in stages or specific departments, organizations can gauge its effectiveness and identify potential issues on a smaller scale. This approach also helps in mitigating the risks associated with large-scale disruptions.
Pilot programs can act as testbeds for AR adoption. By trialing AR in specific projects or departments, companies can gather real-world data on its efficacy, understand the training requirements, and fine-tune its implementation strategy based on this feedback.
Collaborations and partnerships with AR experts
Traditional industries can significantly benefit from collaborations with AR tech companies. Such partnerships can facilitate smoother integrations, with AR companies offering bespoke solutions tailored to the unique needs of the industry in question. These tech companies can provide guidance on best practices, potential pitfalls, and effective implementation strategies.
Tapping into the expertise of AR professionals can significantly reduce the learning curve for in-house teams. By relying on external experts, companies can ensure that they’re leveraging the full potential of AR while also sidestepping common mistakes that can hamper its effectiveness.
Continuous training and skill development
For AR to be effectively adopted in traditional settings, an ongoing commitment to training is essential. This shouldn’t just be a one-off induction into AR but should involve regular refresher courses, updates on new features, and forums where employees can share their experiences and challenges.
To foster a more receptive environment, companies can also champion AR ‘ambassadors’ or early adopters within their teams. These individuals, enthusiastic about AR’s potential, can help their colleagues navigate the technology, acting as in-house experts and advocates. This peer-led approach can be instrumental in breaking down resistance and fostering a more tech-forward organizational culture.
Practical approaches towards AR
Traditional manufacturing industry
There are several instances where traditional industries like manufacturing have successfully implemented AR to address specific challenges. Even companies with decade-long traditions have started using AR for intricate assembly processes, reducing errors and improving efficiency. By overlaying digital instructions directly onto physical components, assembly workers can better understand complex procedures, resulting in fewer mistakes and product defects.
Agriculture and AR
Even in agriculture, traditionally seen as a hands-on, earth-connected industry, AR is making its mark. Farmers can use AR glasses to receive real-time data about soil health, plant diseases, and weather conditions, directly superimposed on their real-world view of their fields. This offers a more intuitive approach to leveraging technological insights, leading to more effective decision-making.
The road ahead: sustainable AR integration
Periodic evaluations and feedback loops
For AR to be a long-term asset, continuous evaluation is key. Traditional industries need to periodically assess the effectiveness of their AR tools, taking into account feedback from the ground up. This iterative approach ensures that the AR solutions in place evolve in tandem with the industry’s needs.
Integration with other emerging technologies
AR, while powerful on its own, can be further amplified when combined with other technologies. Think about integrating AR with AI for predictive maintenance in manufacturing or combining AR with drones in agriculture for better field analysis. Such integrations can keep traditional industries at the forefront of technological advancements.
The takeaway
The intersection of augmented reality with traditional industries is a testament to the adaptive nature of technology and how it can bring about transformative changes even in the most unexpected areas. While challenges are inevitable, with a proactive approach, clear strategies, and a vision for the future, these barriers can be surmounted. As we stand at this crossroads of tradition and innovation, it’s clear that the future holds immense potential for those willing to embrace change and look ahead with an open mind.