Embracing digital transformation in manufacturing
In the vast landscape of the manufacturing industry, the challenge isn’t just about producing items but doing so efficiently, swiftly, and of the highest quality. The race to optimize processes and output isn’t new, but the tools and strategies have evolved, reflecting the rapid advancements in technology and shifts in global market dynamics. As industries burgeon and consumer demands become more intricate, the call to enhance manufacturing productivity and efficiency resonates louder than ever.
However, enhancing productivity isn’t just about modern machinery or advanced software. It’s a holistic endeavor, intertwining the threads of technological innovation, human expertise, and proactive strategy. From the digital revolution redefining operational methods to the critical role of well-trained personnel, the journey towards improving productivity in manufacturing is a multi-faceted pursuit, demanding a blend of innovation, foresight, and adaptability.
Efforts to increase productivity in manufacturing
The manufacturing sector stands at the crossroads of innovation and tradition, with increasing pressures to amplify output without compromising quality. As global competition intensifies and consumer demands evolve, the relentless pursuit to boost manufacturing productivity has become a central theme, prompting industries to integrate cutting-edge technologies, refine processes, and invest in human capital development. The goal is clear: produce more, faster, and better, all while navigating the complexities of a rapidly changing industrial landscape. How to improve productivity in manufacturing? While there are plenty of various approaches seen industry-wide, most include the following measures:
Implementation of Industry 4.0 technologies: IoT, AI, and machine learning
The Fourth Industrial Revolution, frequently termed Industry 4.0, marks the convergence of physical manufacturing processes with digital technologies. At the heart of this transformation are tools like the Internet of Things (IoT), Artificial Intelligence (AI), and machine learning. By incorporating these technologies, manufacturers can create intelligent systems that communicate, analyze, and use data to drive further intelligent action back in the physical world.
IoT devices in factories, for instance, can monitor machine performance in real-time, predicting maintenance needs or optimizing energy use. Meanwhile, AI can analyze the vast amounts of data generated to identify inefficiencies, forecast issues before they arise, and recommend corrective actions. This synergy between the digital and physical realms of production offers unprecedented levels of insight and control, leading to improved manufacturing productivity.
Machine learning, a subset of AI, is particularly powerful for its ability to adapt and improve over time. As it processes more data, its predictive capabilities become more refined. This means that the more it’s integrated into the manufacturing process, the better it gets at foreseeing potential hitches and proactively suggesting measures to optimize productivity.
Real-time data collection and analysis to predict and solve inefficiencies
In the digital era, information is the lifeblood of any industry, and manufacturing is no exception. Real-time data collection, facilitated by sensors and interconnected systems, gives manufacturers an instantaneous view of their operations. This immediacy can be pivotal in detecting issues as they arise or, better yet, before they even occur. But merely collecting data isn’t enough – the true value lies in its analysis. With advanced analytical tools, manufacturers can discern patterns, correlations, and trends that might be invisible to the human eye. This can lead to actionable insights that can address inefficiencies, minimize waste, or optimize resource allocation.
In a world where market demands can change rapidly, real-time data analysis allows manufacturers to remain agile. By understanding shifts as they occur, manufacturers can adapt their processes, making swift decisions that align with both immediate and long-term strategic goals, fostering greater productivity in manufacturing.
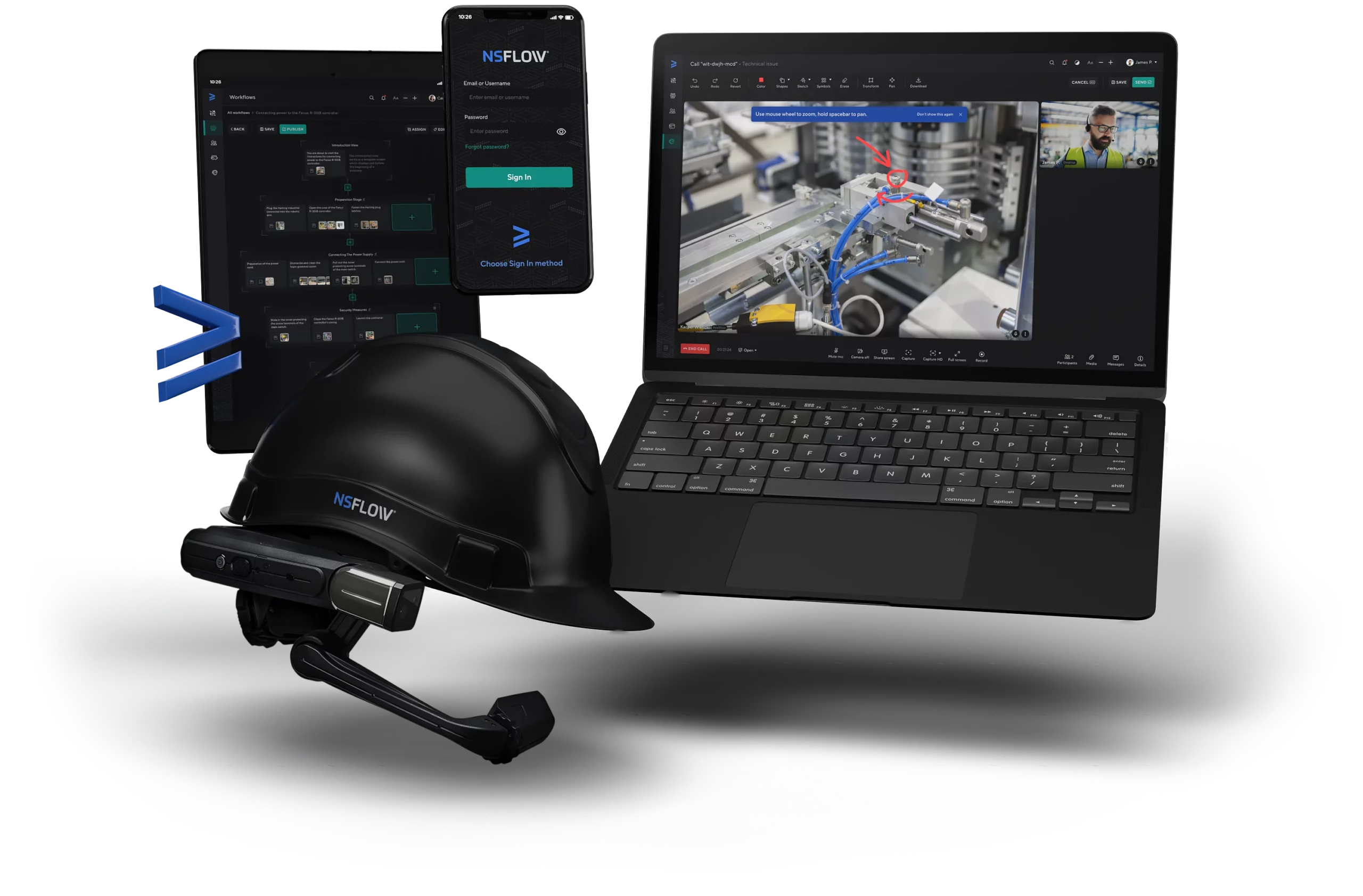
presentation to try
Nsflow in action
Digital twin technologies for virtual testing and optimization
The concept of a “digital twin” might sound futuristic, but it’s fast becoming a reality in modern manufacturing. Essentially, it involves creating a virtual replica of a physical product, process, or system. This allows manufacturers to run simulations, test new ideas, and troubleshoot issues in a risk-free, digital environment.
One of the main advantages of a digital twin is its ability to predict failures before they happen in the real world. By mirroring real-world conditions within the simulation, manufacturers can see how different variables might affect a product’s performance or a machine’s operation. This means fewer real-world tests, faster time-to-market for new products, and reduced costs due to fewer failures or recalls. As technologies evolve, the fidelity and accuracy of digital twins are only set to improve. In the future, it’s easy to envision manufacturing scenarios where products are perfected in the virtual realm long before the first physical prototype is ever produced, ensuring both efficiency and excellence in production.
Workforce training and upskilling
At the heart of any manufacturing operation lies its workforce. While machinery and technology play crucial roles, it’s the human element that often determines the success or failure of any given process. A well-trained workforce not only ensures that tasks are completed efficiently and accurately but also contributes to a safer and more harmonious work environment. Trained employees can better utilize equipment, reducing wear and tear and prolonging machinery lifespan. They can also identify and rectify minor issues before they escalate into more significant, more costly problems. This proactive approach not only saves time and money but also enhances product quality and consistency. Moreover, a well-trained workforce feels more engaged and valued. When employees understand their roles, the importance of their tasks, and the broader objectives of the company, they are more likely to take pride in their work, leading to increased morale, reduced turnover, and a stronger sense of team cohesion.
Adapting to new technologies and methodologies
As mentioned, the manufacturing industry is in a constant state of flux, with innovations altering the landscape regularly. While adopting new technologies can be a game-changer, the real challenge lies in ensuring that the workforce can adeptly utilize these tools to their full potential. Upskilling is the answer here. Beyond just basic training, upskilling focuses on expanding the capabilities of employees, equipping them with new skills that align with emerging technologies or methodologies. For instance, as automation becomes more prevalent, training workers in robot maintenance or advanced machine interfaces becomes essential. The adaptability of a workforce isn’t just about skills but also mindset. Cultivating a culture where change is embraced, where learning is seen as an ongoing journey, and where innovation is celebrated ensures that transitions to new technologies or processes are smoother, more effective, and yield the desired outcomes in productivity and efficiency.
Adoption of automation and advanced technologies
Automation has revolutionized the manufacturing industry, offering unprecedented levels of precision, consistency, and efficiency. From simple tasks like sorting and packaging to more complex operations such as assembly or quality control, automation solutions are transforming how factories operate. By minimizing the human intervention required for repetitive tasks, automation not only boosts productivity but also reduces the risk of errors. Consistency is another significant advantage. Automated systems ensure that every unit produced meets the same high standards, leading to improved product quality and customer satisfaction. But beyond operational benefits, automation also empowers manufacturers to be more flexible. Automated systems can be reprogrammed or recalibrated to handle different tasks or products, allowing factories to adapt swiftly to changing market demands or diversify their product offerings.
Augmented reality contributes to the increase productivity in manufacturing by streamlining industrial processes. AR can be used on various stages of manufacturing processes, from onboarding and training employees, to executing maintenance and service procedures, to conducting factory acceptance tests (FAT).
The integration of IoT and smart manufacturing
The Internet of Things (IoT) is driving the next wave of innovation in manufacturing. By embedding sensors and connectivity into machinery, tools, and even products, manufacturers can gather a wealth of real-time data about their operations. This data, when analyzed, offers insights that can be leveraged to optimize processes, predict maintenance needs, and even develop new product features. Smart manufacturing, a subset of the broader Industry 4.0 movement, sees factories becoming interconnected hubs of data and intelligence. Machines communicate with each other, automatically adjusting operations based on inputs from other parts of the production chain. This level of interconnectivity and autonomy creates a manufacturing environment that’s not just productive but also highly adaptive and self-optimizing. Moreover, with IoT in play, remote monitoring and control become possible. Manufacturers can oversee operations from anywhere, intervening only when necessary. This new paradigm shifts the role of human operators from direct intervention to supervision and strategic decision-making.
Embracing AI and machine learning for predictive analysis
As factories become more data-driven, artificial intelligence (AI) and machine learning emerge as crucial tools for extracting value from this data deluge. Rather than just providing a snapshot of current operations, these technologies enable manufacturers to forecast future trends, predict potential issues, and proactively address them.
Machine learning algorithms can analyze patterns in machinery operations, predicting when a particular component might fail and prompting preemptive maintenance. Such predictive maintenance drastically reduces downtime, ensuring that production isn’t halted due to unforeseen equipment failures. Beyond maintenance, AI can also assist in optimizing supply chains, forecasting demand more accurately, and even aiding in product design. By analyzing historical data, market trends, and consumer feedback, AI tools can offer recommendations on product features, materials, or production methods, ensuring that products are not just high-quality but also market-fit.
The takeway – 8 ways to improve manufacturing productivity and efficiency
The modern manufacturing industry faces numerous challenges, making the quest for enhanced productivity and efficiency paramount. Strategies spanning from the embrace of digital technology to the implementation of lean methodologies aim to streamline processes and maximize output. Human resources, integral to these strategies, benefit significantly from focused training and skill development. Additionally, with today’s expansive global networks, efficient supply chain management is indispensable. The complexities of contemporary manufacturing require a balanced approach, blending technology, human expertise, and strategic management to achieve optimal results and remain competitive.
Manufacturers should be encouraged to foster a culture of continuous learning and innovation. This not only aids in adapting to current challenges but also in anticipating future shifts, ensuring long-term success in an ever-evolving industry landscape.
Improving manufacturing efficiency doesn’t end with technological integration. The future of manufacturing productivity and efficiency lies in the combination of technology, human capital development, strategic foresight, and an ingrained culture of adaptability and innovation.