With the growing adoption of digital solutions, remote collaboration tools have revolutionized the way industries function, particularly in the industrial sector. The pandemic only intensified this shift. Tools like Zoom and Microsoft Teams have transitioned from office-centric platforms to ones that are just as integral on the factory floor. This shift has been particularly profound in the scope of remote assistance, where experts are now assisting technicians from anywhere globally, eliminating the need for their physical presence. Nsflow underscores this evolution, noting how such technological advancements have led to enhanced problem resolution, significant cost reductions, and more timely interventions.
The importance of remote experts
In some sectors, companies use online support teams remotely to assist their customers around the clock and at a low cost. Until recently, the industrial sector has typically not been able to enjoy the same benefits since physical machinery usually needs to be examined by experts via onsite visits and repairs carried out by specialists. However, Industry 4.0 brought many developments that have made many processes involved in running, maintaining, and repairing industrial equipment much more effective.
The importance of remote experts in the modern and dynamic industrial field cannot be overstated. As industries evolve and grapple with challenges both old and new, remote experts stand at the intersection of technological advancement and operational efficiency, offering solutions that transform the way operations are carried out.
Understanding industrial remote support
A significant leap in maximizing the efficiency of remote experts comes with the adoption of wearable devices. Devices like RealWear have transformed the dynamics of remote assistance. They facilitate a ‘see-what-I-see’ experience, enabling experts to guide technicians in real-time, offering a vivid, shared perspective on tasks. This hands-free approach not only boosts efficiency but also enhances the safety of technicians. Shifting from conventional methods such as phones and laptops to these wearable devices ensures that documentation can be viewed while working on a task, photos can be captured without manual intervention, and training becomes a live, immersive experience.
However, simply integrating advanced tools isn’t enough; the processes that accompany them are equally crucial. The Nsflow app is an exemplary tool that makes reaching out to remote experts faster and more streamlined. Unlike traditional methods where establishing contact can be cumbersome, this AR-powered solution significantly reduces the time taken to connect with an expert, enhancing overall efficiency. In essence, to truly harness the potential of remote experts in industrial settings, companies must not only invest in advanced tools but also in efficient systems that optimize these tools. This holistic approach ensures improved safety, cost efficiency, and overall superior quality of work, which is why Nsflow answers industrial needs comprehensively.
The importance of remote expertise in the industrial field
With AR, the expert, essentially, sees through the eyes of the operator, ensuring that the instructions are tailored to the exact situation. This not only spares the time that experts would spend traveling but also translates into significant cost savings and convenience for operators.
Elevated efficiency and cost-effectiveness
With remote support, companies can drastically reduce labor costs and travel times. Previously, a simple repair might warrant a full day’s commitment from a technician due to travel, regardless of the task’s actual duration. Now, technicians can assist multiple clients in a day without geographical limitations. The support isn’t merely restricted by distance; language barriers are broken down with translation features in smart glasses. Furthermore, the system’s flexibility is paramount. Technicians can prioritize tasks, handle multiple queries simultaneously, and even loop in other specialists during a single call, ensuring that problems are addressed with the utmost expertise. This ensures swift problem resolution, which is crucial for the fast-paced industrial environment where every minute counts.
Enhancing quality of service and reducing errors
Remote assistance doesn’t just offer solutions; it’s a proactive approach to problem prevention. Immediate access to guidance reduces the chances of errors that can arise from guesswork or incomplete knowledge. If operators attempt to rectify issues without adequate expertise, it can lead to machinery malfunctions or even accidents. However, with instant support, they can be accurately guided, simultaneously enriching their understanding of the equipment. Such hands-on learning empowers them to handle minor issues independently over time. Furthermore, the technology facilitates on-the-go training for operators, ensuring they’re updated with the latest equipment knowledge. This continual learning environment not only reduces the scope for errors but also minimizes the load on support teams, paving the way for a more streamlined and efficient industrial workspace.
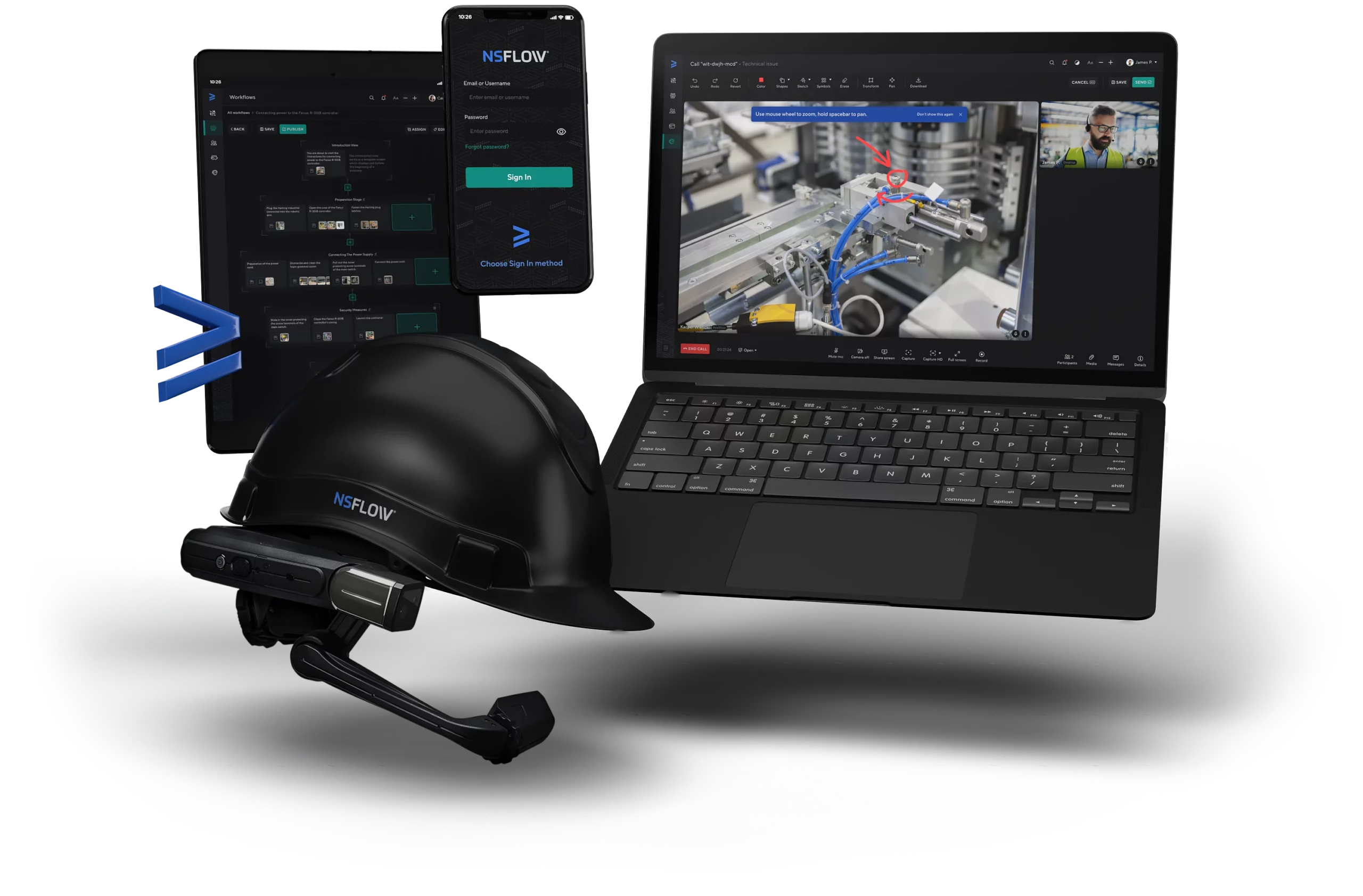
presentation to try
Nsflow in action
What are the benefits of remote support?
Globalization and decentralization
With companies operating in multiple regions or countries, it’s neither feasible nor cost-effective to have experts travel constantly to different locations. Remote experts can provide their expertise regardless of geographical constraints.
Rapid problem resolution
In the past, equipment malfunctions or process breakdowns might have waited for an expert to arrive on-site. Now, with remote experts, real-time solutions can be delivered, significantly reducing downtimes and increasing operational efficiency.
Cost-effectiveness
The cost of sending an expert to a location includes travel, accommodation, and daily allowances, among other things. Remote consultations eliminate these expenses, saving companies substantial amounts of money.
Safety and health considerations
Especially after the COVID-19 pandemic, minimizing physical contact and travel is a safety and health priority. Remote experts can offer their insights without the risks associated with travel and face-to-face interactions.
Access to a wider pool of experts
Sometimes, the best expertise might be in another country or continent. Remote collaboration tools allow industries to tap into global knowledge without geographical limitations.
Continuous learning and training
Remote experts can also play a pivotal role in training local teams, ensuring knowledge transfer and skill upgradation without being physically present.
Optimizing digital transformation
As industries increasingly integrate digital tools into their operations, remote experts, familiar with the latest technological advancements, can guide and accelerate this digital shift.
Flexibility
Remote expertise offers flexibility. Experts can be consulted outside of typical business hours, and in emergency situations, ensuring that operations run smoothly around the clock.
Enhancing quality control
With advanced tools like augmented reality, remote experts can conduct inspections, quality checks, and even audits from afar, ensuring that standards are maintained consistently.
To keep it short, since time is money, the rise of remote experts in the industrial field is a testament to the power of technology and its potential to reshape traditional operational approaches. They are not just a temporary solution but a long-term strategy to enhance efficiency, reduce costs, and leverage global expertise.
Remote support – case study
We walk our talk and present the platform just the way it is – a proven, working solution that brings value to industrial companies in need of remote cooperation solutions. One of our case studies covers the need to execute remote Factory Acceptance Tests (FAT) during pandemic-brought travel bans.
The project in question was nearing its critical FAT phase. During FAT, the customer assesses the machine’s functionality, ensuring it operates as expected in both standard and emergency situations, and adheres to the User Requirements Specification (URS). Typically conducted on-site at the supplier’s location, FAT evaluations can occur in multiple rounds. This phase is pivotal, determining the progression to the implementation stage and influencing the issuance of invoices based on the test outcomes. Postponing the tests could heavily impact our partners’ and their clients’ operational continuity, which is why the decision to employ AR-powered remote FAT was taken.
For three weeks, the companies utilized the Nsflow platform, successfully approving all URS elements. This timely completion of acceptance testing allowed the project to progress to the implementation phase. Given the efficiency of remote FAT execution, both parties adopted the method for future projects, valuing its convenience, cost savings, and time efficiency without sacrificing test quality.
For more real-life examples of Nsflow supporting remote experts and fostering knowledge-sharing in companies, visit the case studies tab.
The takeaway
State-of-the-art technology has made it feasible to tap into the expertise of professionals, irrespective of their location. As industrial companies increasingly adopt these tools, the traditional barriers posed by distance are rapidly dissolving, ensuring that expertise is always within reach.
The future of industry belongs to advanced tech solutions, enabling collaboration regardless the distance. Employ augmented reality in your operations, support your workers with real-time access to expert knowledge, and see how your processes can flourish. Book your free demo and embrace the future of your industry.