Cost reduction in the manufacturing sector is a serious matter. Developing Nsflow, we strive to provide manufacturing entities with a comprehensive solution to improving their operations and fostering cost savings.
Cost reduction in manufacturing
The manufacturing sector is characterized by high competition, complex supply chains, and constantly evolving market dynamics. This places immense pressure on organizations to control costs and optimize their operations. Cost reduction in the manufacturing sector is a serious matter as it directly influences a company’s bottom line, affecting profitability, growth potential, and long-term sustainability. High costs not only affect profit margins but can also make a company’s products less competitive in the market, potentially leading to a loss of market share and diminished revenues.
Another reason cost reduction is critical in the manufacturing sector is due to the cyclical nature of the industry and the impact of external factors such as fluctuations in raw material prices, labor costs, and energy costs. Manufacturing companies often have to manage these variable costs, which can be unpredictable and significantly impact their operations and profitability. By focusing on cost reduction strategies, companies can better navigate these challenges, ensuring operational efficiency, and mitigating the impact of potential cost increases. This allows for a more predictable and stable financial outlook, supporting strategic planning and decision-making.
Last but not least, cost reduction is essential in the manufacturing sector because it frees up resources that can be invested in innovation and technology adoption – two critical aspects of staying competitive in today’s digital age. By reducing costs, manufacturers can invest more in research and development, adopting advanced technologies such as artificial intelligence, robotics, and automation, and upskilling their workforce. These investments can drive further efficiencies, enhance product quality, and enable the development of new products and services, reinforcing a company’s competitive position in the marketplace and setting the stage for future growth and success.
Understanding manufacturing overheads
Manufacturing overheads refer to indirect factory-related costs necessary to run manufacturing processes but cannot be directly traced back to specific units. Examples include utility costs, maintenance and repair of equipment, depreciation, factory supervision, and quality control. High overhead costs can dent a company’s profitability. They inflate the total production cost, leading to higher pricing of products, which may impact competitiveness in the market. Consequently, businesses must find effective strategies to keep these costs under control.
Traditional cost reduction techniques in manufacturing
Traditional cost reduction strategies in manufacturing have focused on areas like process improvement, resource optimization, and supply chain management. Techniques include just-in-time production, lean manufacturing, and value engineering. However, these techniques may not be enough in today’s rapidly evolving industrial landscape. They might pose challenges such as limited scope for cost reduction, potential quality compromise, or adverse impact on employee morale due to cost-cutting measures.
The role of digital transformation in reducing manufacturing costs
Digital transformation refers to the integration of digital technology into all areas of a business, fundamentally changing how you operate and deliver value to customers. It’s about transforming business processes and corporate culture to meet changing market and business requirements. The adoption of digital technologies can lead to substantial manufacturing cost savings. From automating repetitive tasks to improving product quality through precise machinery controls, digital transformation is an effective cost reduction strategy in the manufacturing industry.
Augmented Reality as a part of a cutting-edge cost reduction strategy
Augmented reality has gradually made its way into the manufacturing sector, aiding in areas like training, maintenance, and design. The integration of AR in manufacturing processes can help companies cut costs significantly. It can reduce machine downtime, streamline complex assembly processes, provide real-time assistance, and improve the safety and efficiency of workers.
Industrial-grade augmented reality platforms
AR can play a significant role in reducing direct costs in manufacturing. For example, AR can enhance machine maintenance processes. By superimposing a digital layer of data onto the machine, AR can guide technicians, helping them fix issues faster. Augmented reality can also significantly cut costs in training and skill development. Traditional training methods often involve extensive time and resource investment. However, AR-based training can allow employees to learn at their own pace, minimize training time, and reduce the costs associated with mistakes in a controlled, virtual environment. Furthermore, AR platforms can offer remote assistance. This feature reduces the need for on-site experts, saving travel expenses and time, thereby lowering operational costs.
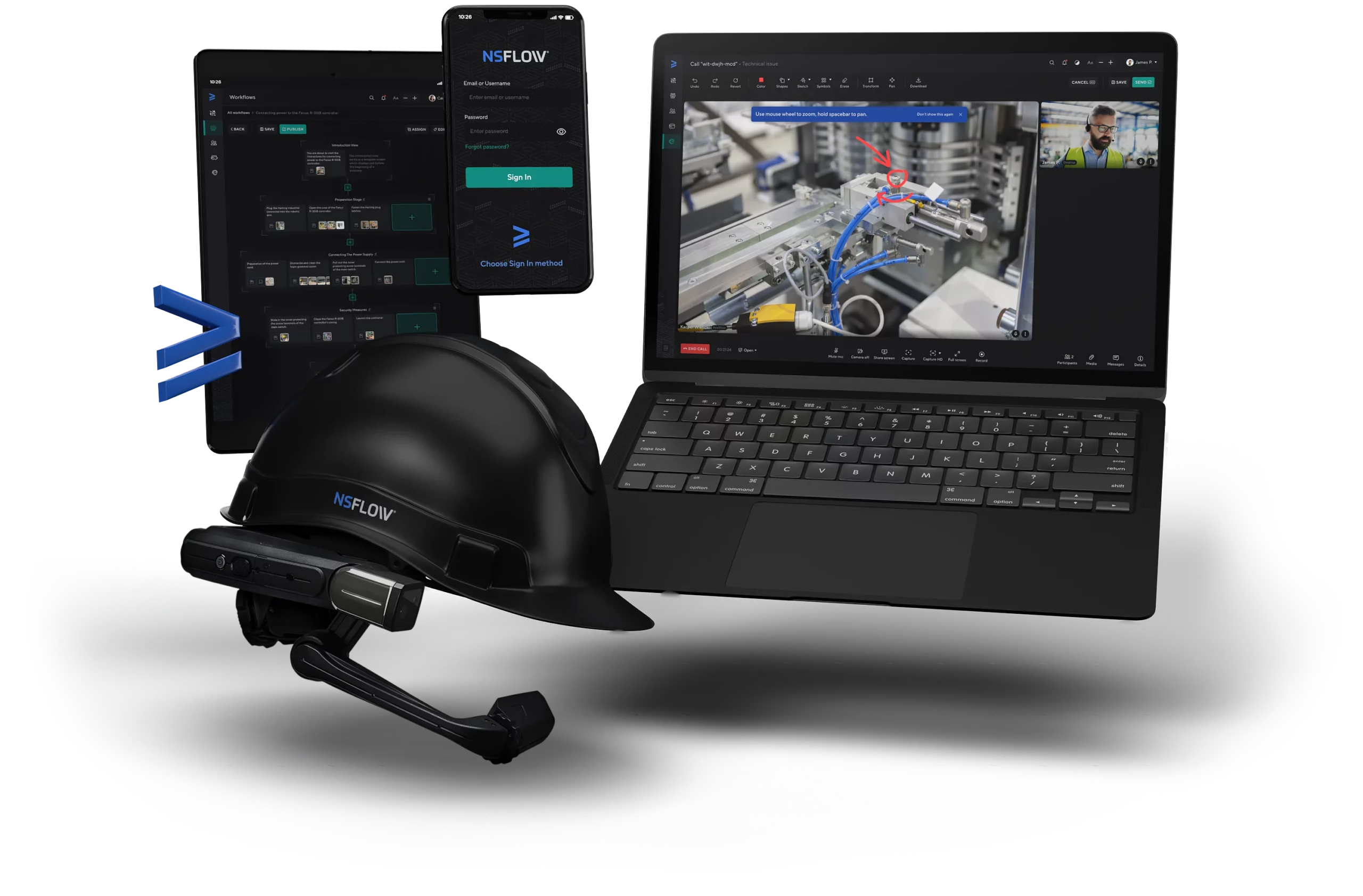
presentation to try
Nsflow in action
The intersection of AI and AR in manufacturing
The combination of Artificial Intelligence (AI) and AR in manufacturing can create a synergy that significantly boosts efficiency and cost savings. AI can analyze complex data and make precise predictions, while AR can visually present these insights in a user-friendly manner. AI can enhance AR applications by making them more adaptable and responsive. For example, AI can analyze a worker’s performance in an AR-based training module, provide real-time feedback, and tailor future training based on the worker’s progress. AI and AR together can improve predictive maintenance, a practice that anticipates failures and schedules maintenance accordingly. By coupling AI’s predictive power with AR’s visual guidance, workers can proactively address potential issues, reducing downtime and repair costs.
How to measure the impact of AR on cost reduction
Quantifying the impact of AR on cost reduction involves tracking key performance indicators (KPIs) before and after AR implementation. This may include metrics related to productivity, error rates, training time, and machine downtime. Businesses can also calculate the return on investment (ROI) of their AR initiatives. This involves measuring the net benefits (cost savings and additional revenues generated) against the total cost of implementing and maintaining the AR platform. Periodic review of these metrics can provide valuable insights, helping businesses tweak their strategies for optimal results.
How to cut costs with Nsflow?
Tools like Nsflow allow companies to create digital workflows for training, monitor progress, and promptly address training needs. Standardizing these digital training materials saves time, reduces costs, and ensures consistency across different locations. Additionally, augmented reality training can help simulate high-risk scenarios, further reducing costs and risks. These digital training contents can be easily updated as new regulations or equipment come into play, eliminating the need for printing and dispatching paper copies. Furthermore, AI can help automate certain aspects of the onboarding process and improve the accuracy and effectiveness of training programs. All these methods contribute to lowering onboarding costs, enabling companies to invest more in areas like research and development or marketing.
Importance of cost reduction and optimization in manufacturing
In the age of digital transformation, traditional cost-reduction strategies might not suffice. Technologies like AR and AI offer promising avenues for manufacturing firms to optimize costs and stay competitive. As the manufacturing industry continues to evolve, the early adoption and intelligent application of these technologies can be a game-changer. They not only help reduce costs but also boost productivity, improve product quality, and enhance worker safety. Ultimately, the integration of AR in the manufacturing process is not merely a cost-cutting strategy but a step towards building a smarter, more efficient, and resilient manufacturing sector.
Taking into consideration the fast pace of the market and high competitiveness, cost optimization is crucial. It helps manufacturers streamline their processes, improve efficiency, and ultimately increase profitability. Cost reduction significantly contributes to a business’s market position and its profitability. By reducing production costs, businesses can price their products competitively, improve margins, and reinvest in their operations. Companies that effectively manage and reduce their production costs gain a competitive edge. They can navigate market volatility better and are better positioned for long-term growth and success.